Diamant Zucker: a Fire Protection Solution using Oxygen Reduction
Icing sugar, brown sugar, rock sugar, sugar in packets and tins: sweetness is all around you in the factories of the sugar suppliers Pfeifer & Langen. The company has been supplying sweet products made from beet and cane sugar to the food industry and end users for 150 years, and sells them under the Diamant Zucker brand. The company, founded in Cologne, has numerous locations throughout Europe and is one of the largest sugar suppliers. Mid 2020, a new high-rack warehouse was put into operation at the factory in Poland – with an appropriate fire system from Wagner Poland.
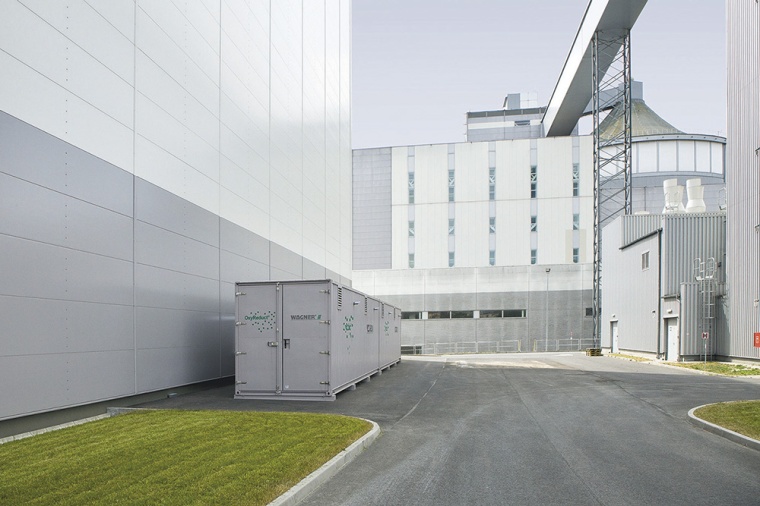
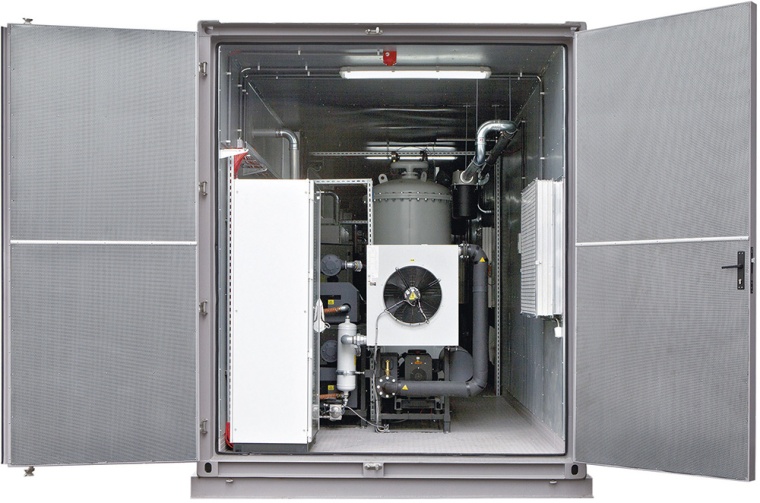
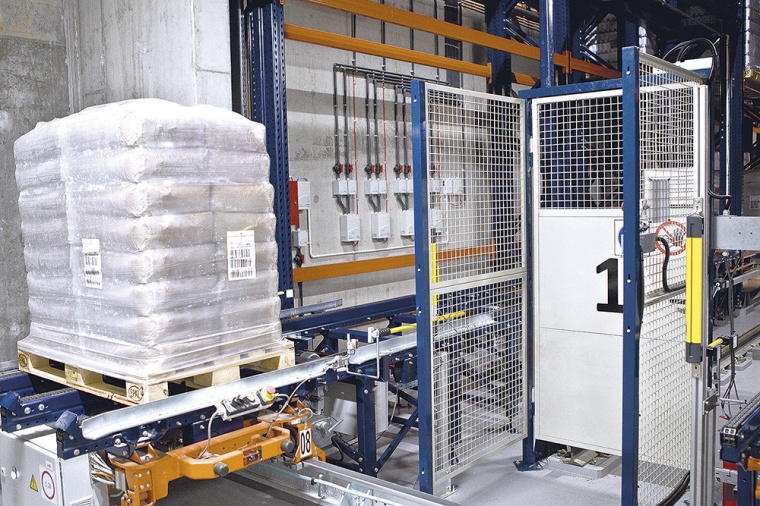
Pfeifer & Langen Polska S.A. has built a new high rack warehouse at the Środa Wielkopolska factory near Poznań. This is where sugar specialties such as cinnamon sugar or syrup are stored. Up to 24,000 palettes can be put into the 35 meter high, 140,000 cubic meter warehouse. It is directly connected to the sugar factory via an air lock. The storage and removal of goods as well as their consignment takes place automatically.
But not only the newly-built warehouse itself – and the investment tied up in it – needs special protection. „The most important thing in this case is the stored sugar“, says Andrzej Biedulski, project leader at Pfeifer & Langen Polska. That is why the company decided right from the beginning against a water or foam-based solution. This is because the extinguishant itself almost inevitably causes damage, and so an alternative fire protection solution had to be found. The company found the Wagner Group and its expertise in active fire prevention.
Protect the Sugar, Maintain Availability
Pfeifer & Langen Polska defined their protection requirements right at the start together with the team of Ireneusz Bruski, CEO of Wagner Poland. Apart from the protection of staff, the following aspects had also to be considered: in an emergency, no sugar must be allowed to go up in smoke or soot nor be destroyed by water extinguishant. Operational processes as well as the flow of goods and other logistical processes must by maintained in the case of an emergency and the goods must always remain available for customers.
The sugar products that are made in the production halls are packed and stacked on palettes there before they are brought to the warehouse for onward forwarding. This takes place according to today‘s standards and totally automatically. Shelf rack feeders and conveyors are used for this. These and the packing equipment are potential sources of fire that had to be considered. Only by making a risk analysis can the ideal fire protection solution be found for each individual area to be protected.
Various different types of fire risk must be considered in high rack warehouses. An increased level of automation in den production area and in the warehouse itself, and the consequent higher number of electrical components, presents a higher risk of fire. With a storage height of up to around 35 meters any fire would be accelerated because of the narrow aisles and the chimney effect. Equally, the dense packing of the goods as well as the packaging material made of paper and the storage on wooden pallets has an effect on the speed that a fire spreads. It is also necessary to consider the complex production processes because of the connection to the production area via an air lock as well as the high sensitivity of the goods to smoke and moisture. An applicable solution can be found if all these risk factors are taken into account. And always with first priority is the target of preventing a fire in the warehouse at all.
Solution in a Container
Four Oxyreduct V-Line systems together with a very early fire detection system form the basis of the fire protection solution. The V-Line systems produce nitrogen from the ambient air and feed this in the previously defined area to be protected. This suppresses the oxygen concentration below the specific inflammation level of the materials that are mostly stored there. A fire can neither develop nor spread in this protective atmosphere. But in spite of this, a smoldering fire can still happen and so this solution includes a system with air sampling smoke detectors to provide early detection of fires.
The Titanus extraction points are above the alleys of the high rack warehouse and constantly take samples of the air from there. Even the tiniest pyrolysis particles will therefore be detected as early as possible. The devices are up to 2,000 times more sensitive than conventional single-point smoke detectors.
A special aspect of the solution for Pfeifer & Langen is that a large proportion of the fire protection equipment, such as the nitrogen generators and electrical control cabinets, are not built into a separate room but were built instead into a container positioned beside the high rack warehouse. „Such an external equipment room is ideal for maintenance and service purposes because it is easily accessible. We were also able to save on construction costs because a separate room in the warehouse for the equipment was not required for the fire protection system“, said Ireneusz Bruski, CEO of Wagner Poland of the reasons for the container-based solution.
The high rack warehouse started operation in the middle of 2020. Since then, the various types of sugar products have all been safely shipped to many countries throughout Europe.
most read
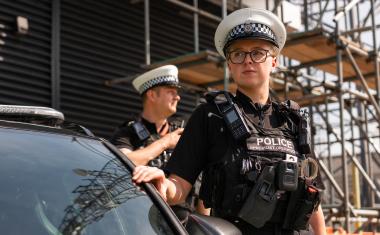
Motorola Boosting Lancashire Police Efficiency
Time-Saving Technology Cuts Paperwork and Keeps Lancashire Constabulary on the Beat
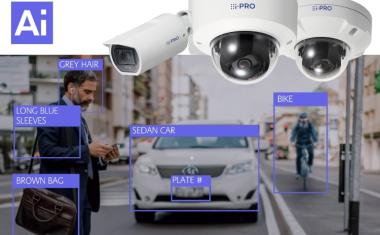
i-Pro on the Path to ISO/IEC 42001: AI Governance for Physical Security
i-Pro is the first company in the security industry to pursue certification for AI management systems under ISO/IEC 42001.
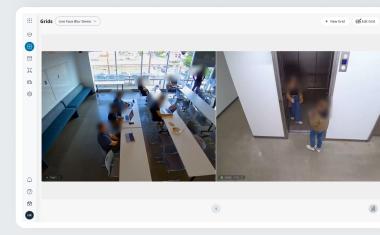
AI-Powered School Security: Verkada Now Trusted by 20 Million Students Worldwide
Verkada Secures 20 Million Students: How AI Is Transforming School Safety
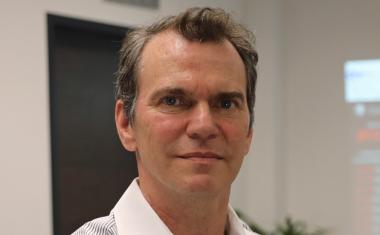
Global Security Strategies of the DHL Group
Frank Ewald (DHL Group) on Global Security Strategies and the Challenges of the Logistics Industry
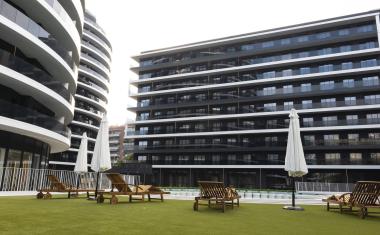
Mobile First is the 21st-Century-Experience
From Offices to Villas, Mobile Access Transforms Facility Security and Management