Honeywell: choosing the right gas detection system
Honeywell: choosing the right gas detection system. There are many gas detection products on the market that might appear to be the same, but a closer inspection of specification, ...
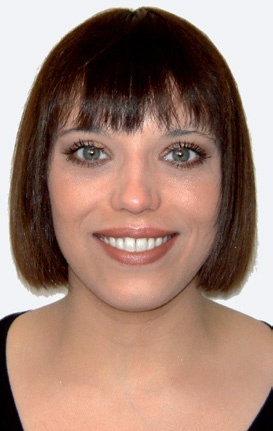
Honeywell: choosing the right gas detection system. There are many gas detection products on the market that might appear to be the same, but a closer inspection of specification, functionality and features reveals major differences in what products can do and the potential benefits they can offer.
Similarly, individual applications, plants and businesses are also unique in their respective designs, unique in their specific needs and processes undertaken and unique in the type of safety system they choose to implement. Any company employing personnel has the obligation to conduct risk assessments to identify potential hazards associated with its field of activity.
These risk assessments may identify potential gas, vapour or Oxygen deficiency hazards and a suggested risk reduction method may be the use of gas detection equipment. As Honeywell Analytics’ Strategic Marketing Manager for Industrial Products, Kevin Dean is well-versed in helping prospective end-users find the best gas detection solutions to meet their needs. “Although there might be similarities between applications, a variety of other variables mean that each plant has unique needs. The key to helping a customer select the right equipment comes down to asking the right questions and ensuring that everything has been considered.”
Identifying the Prime Objective
Gas detection equipment is used to detect flammable and toxic gas releases and also to protect plant and personnel. This type of equipment can undertake a number of tasks including activating audible and visual alarms for building evacuation or initiating plant / process shutdown. Depending on the processes being undertaken and the gases being detected, remote or offsite alarm notification plus event data logging / reporting may also be required for Health and Safety management records. Another factor impacting on the need for enhanced reporting functions might be regulatory compliance or a condition of insurance. Knowing the prime objective and motivation for having such equipment is the first step in selecting the best solution.
Ask the Right Questions
Having identified the primary objective, the suitable equipment is selected by asking a number of key questions. These fall into three broad categories:
- The gases to be detected and where they may come from
- The location and environmental conditions where detection is to take place
- The ease of use for operators and routine servicing personnel
The answers to these questions will have a direct impact on the proposed solution and the associated costs to supply and maintain that solution.
The Gases to Be Detected and Where They May Come From
The gases to be detected should be identified by risk assessment, although experienced gas detection equipment manufacturers are often able to help in this process, based on their experience of similar applications. However, it is important to remember that it is the end user’s responsibility to identify all potential hazards.
There are three main types of gas risk:
- An explosion from a flammable gas
- Poisoning of personnel from a toxic gas
- Asphyxiation from an inert gas
Kevin Dean explains the process used to identify the risks associated with certain gases. “The gas detection vendor uses published data to identify whether a gas is flammable, toxic or an and the relative levels at which it could cause a hazard. An ideally suited gas detection solution aims to detect and alarm prior to dangerous levels being reached. The same published data gives information as to whether the gas or vapour is lighter or heavier than air, as this will affect the selection of sensor positioning at the points of detection.”
It is also essential to identify the potential source of a gas release as this helps determine the number and location of detectors required for a fixed gas detection system. In instances where the source of gas release is not known, portable gas detection equipment worn by site personnel may offer a better solution.
Some typical gas sources include:
- Natural occurrence, e.g. Methane and Hydrogen Sulphide from the decomposition of waste
- Leakage from a supply pipe or storage tank, e.g. piped natural gas supplies Emissions from a combustion process, e.g. Carbon Monoxide from a car exhaust or a boiler flue
- Emissions from a production process, e.g. solvents in the printing and coating industry Emissions from manufacturing plant, e.g. Ammonia from refrigeration plant or Nitrogen from Nitrogen supply plant
The Location and Environmental Conditions Where Detection Is to Take Place
The performance, accuracy and reliability of any gas detection equipment will be affected by the environmental conditions it is subjected to. Temperature, humidity and pressure levels at the location all have a direct bearing on the type of equipment that should be selected. Additional factors such as potential variations resulting from a production process itself, diurnal / nocturnal fluctuations and seasonal changes may also affect the type of device which is suitable.
It is important to consider whether the equipment will be used inside or externally as this can greatly affect the design of the device. For example, an external location that is exposed to elements such as wind, rain and salt spray, will require equipment which is resistant to the corrosive affects of that environment. Although indoor locations typically require less robust housing, consideration should be made for internal areas which are hosed down on a frequent basis.
IP Rating
In locations where water / moisture, dust and dirt are prevalent, it is important to get a device that is protected by water / dirt ingress. There is a categorisation for this type of protection known as an IP Rating (Ingress Protection) followed by three digits denoting the actual protection it features. Aside from natural environmental conditions such as weather, there may be other materials in the environment that can have a potential effect on the type of equipment that is chosen.
For example, there may be other compounds such as Hydrogen Sulphide which have corrosive properties or other airborne elements which could have an adverse effect on the reliable operation of some sensing technologies, e.g. Silicones poisoning catalytic bead sensing technologies.
Hazardous Locations
Another important consideration is a device’s suitability for use in certain hazardous locations. Hazard areas are classified according to their perceived likelihood of hazard, graded from Zone 0 (an area featuring a continuous hazard) to Zone 2 (an area featuring a possible hazard).
In a Zone 1 location (where there is an intermittent hazard), it is essential to use equipment that will not cause the “spark to the bang.” What this means is that the device must pose no threat in terms of its potential to ignite a gas cloud. With this in mind, equipment that is Intrinsically Safe (Ex i) or Explosion Proof (Ex d) has been created to provide enhanced safety.
The information gathered in this initial evaluation will help determine which sensing technology is most likely to provide a reliable solution, as Kevin Dean comments. “A competent gas detection equipment supplier will have a range of different sensing technologies available that can be applied to a given application. In addition, the environmental conditions start to determine the best mechanical configuration of the final solution”.
Product Functionality
The next area of consideration relates to additional product functionality. As a rule, high-spec devices tend to cost more money, but some of the additional features themselves often provide long-term benefits regarding the ongoing cost of ownership. There are many variations when it comes to functionality. Aspects like wiring configuration are important, especially when retrofitting into an existing system.
If the apparatus is being integrated into a separate safety system, certain communication protocols may also be required such as HART, Lonworks or Modbus.
Consideration will also need to be given regarding the requirement for local displays on transmitter units and local configuration of the unit and gas displays. Kevin Dean comments that a holistic approach needs to be adopted when looking at the functionality of a device. “There are a large number of variations in products in terms of the spec they offer and their individual functionalities. As you would expect, there is a cost implication with increased functionality. Again, this is where working with a gas detection specialist can help by enabling your business to identify the additional spec that will complement your needs. Things like local displays, local user interfaces, software compatibility, the number of relays and outputs required, remote sensor mounting capabilities, on-board diagnostics, cartridge hot swapping and event logging abilities provide additional benefits to the user and make one product more applicable than another.”
The Ease of Use for Operators and Routine Servicing Personnel
Routine maintenance is an important consideration. Some gases and vapours can be detected with a number of different sensing technologies, e.g. flammable gases with catalytic beads or non-dispersive infrared (NDIR). Catalytic beads do not provide fail-to-safety operation and therefore require a high frequency of routine maintenance, however NDIR based solutions tend to have a higher initial purchase price, but require less routine maintenance.
In-house resource to undertake such routine maintenance needs to be identified and in the absence of such a resource, budgeting for third-party maintenance is an important factor in selecting the right equipment. Detection equipment downtime during routine sensor replacement can lead to the loss of production. If this is a concern, some solutions can provide a fast, simple and safe method of sensor exchange without needing to down-power the system or the plant.
A good gas detection equipment supplier should be able to offer a range of service packages to help maintain equipment. It is worth checking the number of personnel they have and their ability to respond to an incident or emergency call out.
Work with the Experts in Gas Detection
Gas detection equipment can play an important role in reducing the risks to personnel and plant. Careful understanding of the plant and its process is essential to selecting the most appropriate solution. As the definitive Experts in Gas Detection, Honeywell Analytics offers products suited to all types of applications from small boiler rooms to large plants and offshore platforms.
Their range has been specifically designed to meet the varying demands of businesses in a wide array of industries and they have options to suit every budget.
Contact:
Honeywell Analytics
Tel.: 00800 333 22244 or Tel.: 0041 44 943 4300
gasdetection@honeywell.com
www.honeywellanalytics.com