How to Choose Protective Garment for Working With Hazardous Substances
Linting and particle shedding of protective garments contaminate products during the manufacturing process. These particles can come from the workers or from the protective garments themselves.
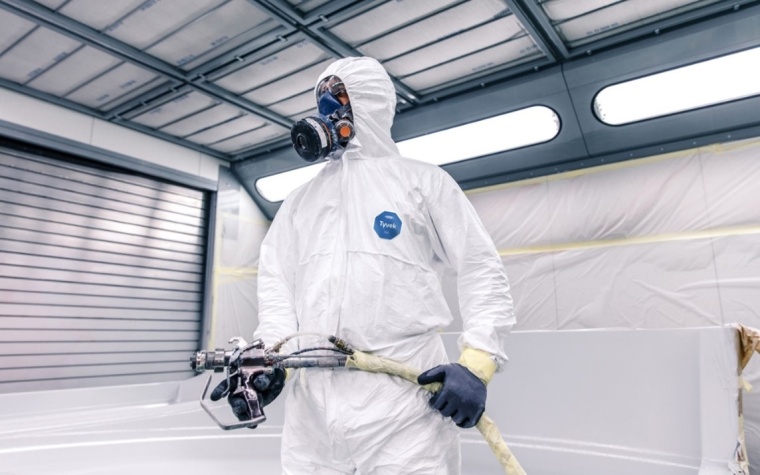
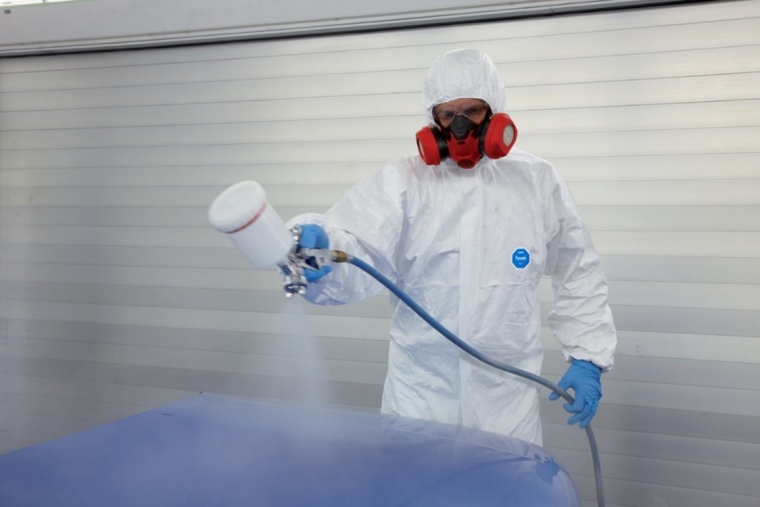
There are regulatory requirements for protective garments and PPE that specify their safety features and properties for use in different applications. Nevertheless, there are still performance differences between garments that meet the same regulatory requirements.
Several factors differentiate one protective garment from another, including the material used, the design of the garment, and the quality of manufacturing. Choosing which protective garment is the best solution for each application requires an assessment of the safety needs as well as the garment features that meet those needs. Here are seven key factors to consider when selecting protective garments:
1. Three Material Types to Consider: SMS, MPF, and Tyvek
There are three common material types used for protective garments.
- Spunbond Meltblown Spunbond (SMS) fabrics, which is a trilaminate non-woven fabric.
- Microporous Film (MPF) is also a non-woven laminate fabric
- Tyvek is a nonwoven fabric consisting of ultrafine continuous flash-spun polyethylene fibers
DuPont Tyvek fabric offers an ideal balance of protection, durability, comfort, and contamination control versus SMS and MPF materials and therefore acts as a breathable barrier against particles and infective agents. For instance, permeation rate is an important factor when evaluating protective garments against liquid and gaseous chemicals and is a key measure when comparing the performance of garments. A generic permeation test is of limited value because different liquid chemicals may permeate a garment at different rates.
Some manufacturers provide tables with more detailed information about permeation properties for a variety of chemicals. These tables show the Actual Breakthrough time (BT Act) when the first molecule passes through the fabric for each type of garment they produce. They also show the BT 1.0 (which is the time taken to reach 1 mg/cm2/min of permeation) as required by European Standards. Other parameters shown may include the highest permeation rate known as the Steady State Permeation Rate (SSPR) and the minimum detectable permeation rate known as the Minimum Detectable Permeation Rate (MDPR).
2. Linting Properties: Characteristics of Particle Shedding
One of the challenges with protective garments is the contamination of products due to particle shedding. These particles can come from the workers or from the protective garments themselves. Different materials have different characteristics when it comes to particle shedding. DuPont Tyvek 500 fabric, for example, is inherently low-linting and abrasion resistant.
Particle shedding is particularly vital in industries like pharmaceutical manufacturing where foreign particles can contaminate a product causing substantial losses to the manufacturer. Specifically, the Cleanroom environment of pharmaceutical companies has strict regulations for particle shedding and must be tightly controlled to prevent contamination.
3. Anti-static Treatment: Dissipation of Possible Electrostatic Charging
While many industries require the use of protective garments, some industries are more hazardous than others. For example, some protective garments are worn in explosive environments, which have the dual risks of exposure to hazardous materials and the possibility of explosion. In all cases, PPE must be dissipative and shall be worn in combination with conductive or antistatic shoes to provide the necessary earthing for a good dissipation of possible electrostatic charging.
European Standards for performance classification of protective clothing against chemicals are covered by EN 14325. However, this standard does not require electrostatic properties. EN 1149-5 covers this additional requirement. Companies purchasing protective garments for EX zones must therefore ensure that the garment they purchase meets both these European Standards, as a minimum.
4. Zipper Design: How to Prevent Liquits and Solid Particles to Migrate
The zipper is a point of vulnerability for protective garments because liquids and solid particles could migrate through the zipper and come into contact with the worker. However, several features can help to prevent this possibility.
- Zippers made with liquid-tight DuPont Tyvek fabric are far superior to textile zippers as they do not allow the migration of particles or liquids through the zipper.
- Auto-lock zippers do not allow the zipper to open by itself while wearing the garment thus preventing an accidental opening where hazardous materials could pass through.
- Diagonally sewn zipper flaps direct liquid drops away from the garment seams.
5. Ease of Movement: Squatting or Streching Possible with Right Design Feature
Whenever the wearer of a protective garment moves, they could expose weaknesses in the garment by stretching them to the point of tearing or by creating a gap between the garment and the worker. Simple motions like squatting or moving the head are typical examples. This challenge can be overcome through design features.
Garments made using 3D designs with gussets give more freedom of movement than flat 2D designs and avoid tears that could occur when squatting. A three-piece hood design helps to minimise risk of exposure by ensuring the hood moves with the head. This design is more effective than a two-piece hood, which does not move when the wearer turns their head.
6. Stitching and Gluing: Every Stitch Bears a Risk
Every stitch on a protective garment makes a hole in the garment where dust or liquid can accumulate, especially at the seam of the waist elastic. The type of seam significantly influences its protective capability. External seams offer higher levels of protection from ingress of foreign materials than internal seams. Other options include taping. Overtaping a stitched seam makes it even tighter and may even offer protection against the permeation of chemicals. But only a tight seam will maintain the garment’s integrity and protect workers from hazardous materials. If the seams are not overtaped, it is recommended to reduce the number of stitched seams. Using a glued-in waist elastic rather than a stitched-in waist elastic preserves the benefit of better fit while eliminating the need for a very long stitched seam in the back.
7. Quality Control for PPE: Manufacturers Must Have Quality Systems with Multiple Layers of Protection
Protective garment manufacturers must have strict quality control measures to ensure that every garment coming off the production line meets the specifications and will protect workers from hazards in accordance with their rating. The best manufacturers have quality systems with multiple layers of protection:
- The first level of quality assurance is achieved through checks performed by the production facility itself.
- The second level of quality assurance is achieved through checks performed by resources from the same company but from outside the production facility.
- A final level of quality assurance is achieved by inviting third party resources from outside the company to check the quality of protective garments. These tests are normally unannounced to increase their effectiveness.
The European PPE regulation and the CE certification for chemical protective garments require that the manufacturers implement strict quality controls and are therefore a guarantee of protection and performance for the wearer of such garments, unlike non-CE certified white coveralls.
DuPont Tyvek garments have excellent performance as protective garments for workers in various industries. This performance stems from the properties of Tyvek material, the design and manufacturing of the garments, as well as the strict quality control procedures we adopt.
Business Partner
Dupont de NemoursRue Général Patton
2984 Luxembourg
Luxembourg
most read
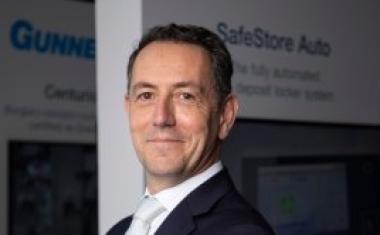
Protecting Valuable Items from Theft, Fire, and Unauthorized Access
GIT SECURITY Exclusive Interview with Emmanuel Harir-Forouch, Global Business Development Director at Gunnebo Safe Storage
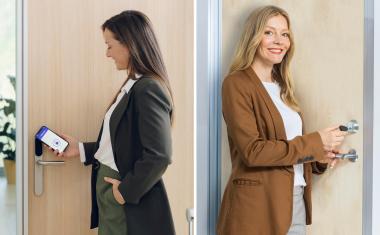
Assa Abloy's Commitment to Sustainability
How Sustainability Inspires Innovation and Product Design
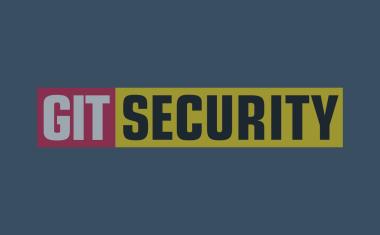
Prepare for the CER Directive
Securing Critical Infrastructure through Regulation
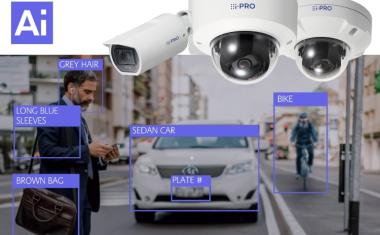
i-Pro on the Path to ISO/IEC 42001: AI Governance for Physical Security
i-Pro is the first company in the security industry to pursue certification for AI management systems under ISO/IEC 42001.
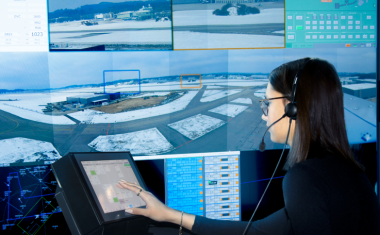
Airport Security and Efficiency with Dallmeier
Interview with Industry Expert Karlheinz Biersack