No More Greenwashing in Workwear Production
The textile industry impacts severely upon the environment worldwide. Fristads wants to promote work on sustainability in the industry, which means taking account of the entire product life cycle. This involves making production processes and the environmental impacts of garments transparent for consumers. GIT SECURITY spoke with Marcus Gotthardt, Digital Sales Manager for the DACH region in January 2022.
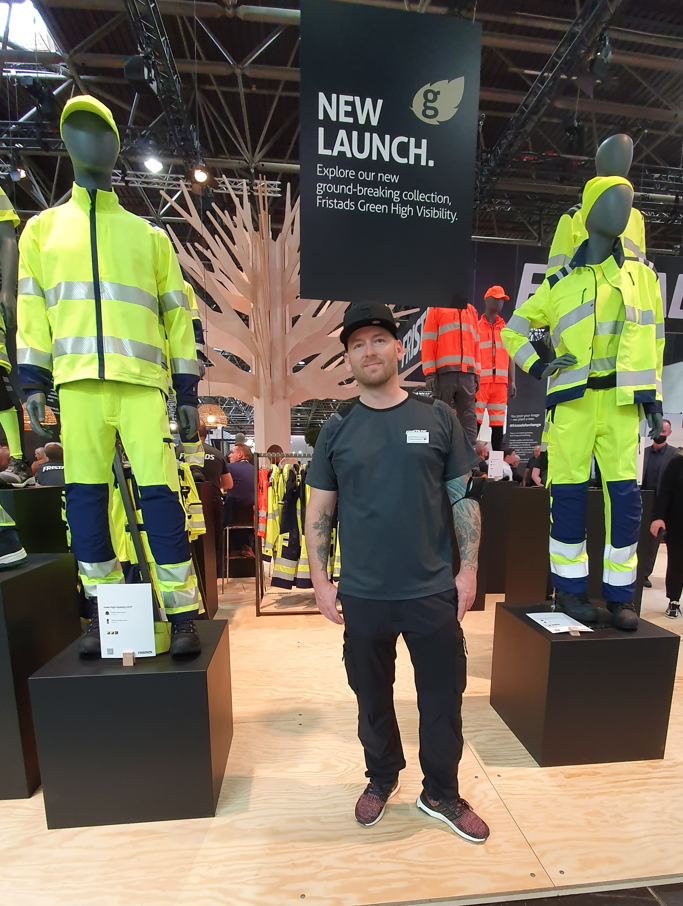
GIT SECURITY: How do you interpret “sustainability” – in terms of your company philosophy?
Marcus Gotthardt: As far as Fristads is concerned, “sustainability” means minimising environmental impacts as far as possible and in all aspects of what we do. In order to do that, we use lifecycle analysis and gather data for all areas in which improvements can be made – from the design process and then production right through to delivery and eventually disposal.
Honesty and transparency are guiding principles for our work on sustainability, since we are determined to avoid greenwashing. This includes being open about the fact that the textile industry is a sector with major environmental impacts which it needs to reduce significantly. At present, production of clothing accounts for 4–8% of greenhouse emissions worldwide, generating some 20% of the world’s water pollution. We want to accept responsibility and rise to the challenge of promoting work on sustainability in the textile industry.
The best way to reduce the environmental impacts of clothing is to manufacture less of it. At Fristads, we take great pride in manufacturing high-quality workwear which is resistant to wear and tear and does not go out of fashion. And on those occasions where garments do get damaged, we would rather repair them than replace them with new ones.
To ensure that consumers can make informed decisions when they buy clothing, manufacturers must also assume responsibility for ensuring transparency in relation to the production process and the environmental impacts of every garment. We would even go so far as to say that measuring the environmental impacts of clothing should be made mandatory. Development of our EPD was a crucial step in the right direction and we hope that other clothing manufacturers will follow our example. Because as far as our planet is concerned, we are all responsible.
How have you implemented this?
Marcus Gotthardt: We are particularly proud of the fact that all our green products come with an EPD (Environmental Product Declaration) and that we can therefore prove that they are manufactured sustainably. For each green product, we produce an EPD report detailing the environmental impacts of the product in question and explaining the extent to which it is more sustainable in comparison to a conventionally manufactured product, e.g. how much CO2 or water is saved during the manufacturing process. Our fristads.com Website has a “green calculator” which allows customers to work out how many tons of CO2 and how many litres of water can be saved if they opt for green clothing.
Our green products implement sustainability in all four main aspects of the product life cycle:
- Design: Even during the design process we pay attention to developing products in such a way as to reduce sewing times and waste as little material as possible. The small amount of scrap material which is still produced is processed to make other products, such as comfort pads – zero waste.
- Raw materials & choice of materials: For Fristad’s green products, we only use products with a higher level of sustainability, such as bio cotton, recycled polyester made of recycled PET bottles and Tencel Lyocell (cellulose from sustainable wood).
- Production: The e.dye process, also known as the waterless dye system, is used to dye most products. In comparison to traditional dyeing, water consumption is reduced by 75%, since the dye is added to the raw materials.
- Packaging & delivery: All goods are transported by sea and road. To enable transport capacity savings, green products are packaged using a special folding technology. This has enabled us to dispense with most plastic packaging. Where it is unavoidable, we use plant-based or recycled packaging materials.
As manufacturers, however, we must assume responsibility by manufacturing high-quality clothing which is durable and by being transparent about the ecological footprint of our garments. That is why, in 2018, we joined forces with 40 other manufacturers in the Swedish Textile Initiative for Climate Action (STICA), thereby committing ourselves to precise monitoring and reduction of greenhouse gas emissions. Fristads has managed to reduce emissions by 58% since 2018. This is also the reason why we developed our environmental product declaration, a standard for measuring the environmental impacts of a garment objectively.
Which limitations remain at the moment? In financial terms?
In technical terms?
Marcus Gotthardt: Actually, there are no technical limitations which cannot be overcome. Since the market is large and many manufacturers are all working on or conducting research into ideas for solutions at the same time, many beneficial advances in textiles technology are currently happening at lightning speed.
One example: Up until about three years ago, we were still experiencing technical limitations. In collaboration with our supplier Tencel, we were attempting to take clothing already made of recycled materials and recycle it again by turning it into new clothing. When it came to be recycled for the 2nd or 3rd time, this led to compromises in quality which were unacceptable for workwear. It is difficult to separate out blended fabrics, e.g. those comprising cotton and polyester, and to process them without compromising on durability.
We were finally able to partially close the recycling loop thanks to a pilot project with our partner Post NL, where we manufactured polo shirts partly made from old garments. This was a major step forward for us, but we will continue to look for solutions in order to turn “partially” into “completely”. From 2022 onwards, we will be assisting or co-operating with research institutions and universities across Europe on various studies and research projects on the subject of “Closing the loop”, confident of being able to find a solution.
Can even minor adjustments enable you to make a long-term impact?
If so, what are they exactly?
Marcus Gotthardt: Yes, absolutely – and that goes for both the manufacturer and the consumer. Manufacturing durable, easy-care clothing has a huge long-term impact. It means that less clothing needs to be produced and fewer returns need to be processed.
Consumers also need to understand that clothing should be used for longer. When making purchases, they can prioritise quality over quantity and before throwing clothing away they should check whether it could actually still be repaired. To keep enjoying your clothing for as long as possible, it is absolutely essential to take note of the care instructions (ideally at the purchasing stage).
If the usable life of all the T-shirts on the British market could be extended by just 10%, it would prevent 100,000 tonnes of CO2 being released into the atmosphere every year.
In 2020, Fristads launched the Care & Repair campaign to raise awareness of the fact that repairing clothing – not replacing it – is the sustainable solution. The other point here is that clothing will also last longer if it is cared for properly. Most of the items in the Fristads collections are particularly easy-care and can be washed at 60°C, which also makes them more durable. Many collections can also be washed in industrial machines at 75 °C or 85 °C.
Does a garment really have to travel all around the world?
Marcus Gotthardt: The clothing itself can also be manufactured in European factories, such as our factory in the Ukraine. The raw materials and most of the “components” of the clothing – such as buttons, zip fasteners, thread, and fabric – are sourced from Asian countries, however.
What obligations do employers have? Or has it so far “just” been a question of having the foresight to take voluntary action?
Marcus Gotthardt: Since durability is the key to reducing the environmental impacts of a garment, more employers must also start thinking more about the quality than the price. Viewed in the long term, quality is no more expensive. The time has come to cease promoting our throwaway society and to develop an industry that is genuinely sustainable. And we would like to be part of that solution.
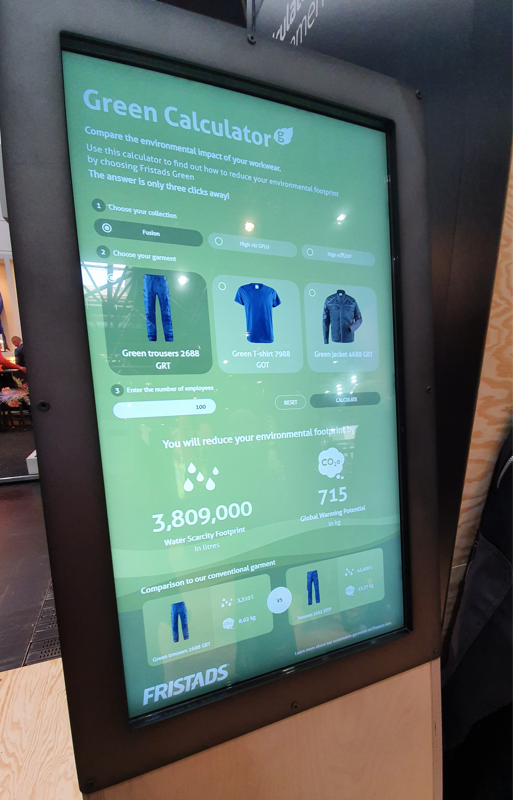