On the Way to Sustainability in the Protective Workwear Industry
Sustainability is the keyword of the company strategy that the Swedish protective workwear manufacturer Fristads follows. The long-established manufacturer wants to reduce its greenhouse gas emissions by half by 2024, and to lead the way for the transformation of the clothing industry. GIT SECURITY spoke about this with Lena Bay Højland, Product Director Fristads.
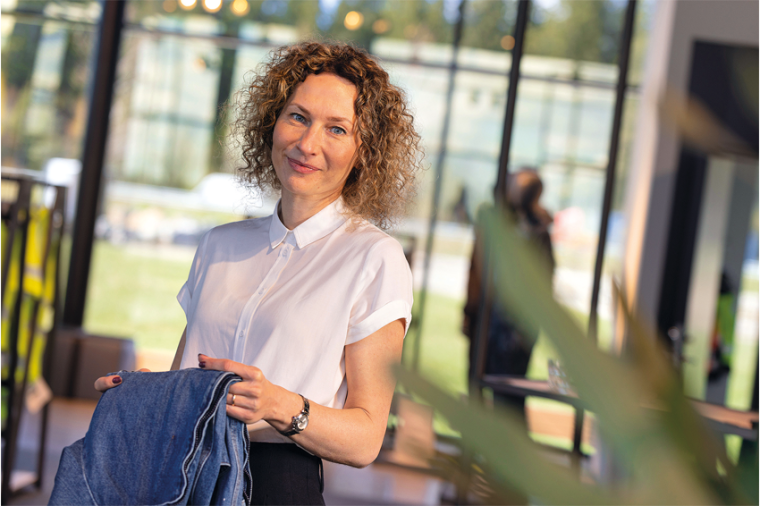
GIT SECURITY: Ms. Højland, Fristads is almost 100 years old and a traditional part of Swedish commercial history: the company has been manufacturing workwear since 1925 – and it was even the first Swedish manufacturer of jeans. Could you tell us what is in the product portfolio these days – in particular the PPE range?
Lena Bay Højland: I can tell you in three words: a broad portfolio, innovation and sustainability. We supply various different industries – and for us, innovation means that we work with modern and innovative cloths that meet the needs of our customers. Our products, which are defined by our customers themselves, speak the language of the end-user and are always up-to-date in their functionality and protection.
The aspect I mentioned last, sustainability, is particularly important for us. Our product portfolio is strongly oriented towards benefits for the wearer. Although we concentrate on providing a modern appearance in a contemporary design, we do not add unnecessary, fashion-motivated variations that stress our climate. For example, all trades will find a wide product choice in our Corporate Wear for industry and tradespeople, such as in the Skarup or the new Forsbo collections that have appealing colors for almost every activity and company. But they are still workwear that has to fulfill a purpose.
Innovations such as new types of cloth have been a driver of your business from the beginning – is this still the case?
Lena Bay Højland: Definitely. Innovations in the development of raw materials are even more important today than before. The materials should be lighter and more comfortable, but also hardier than ever at the same time. Wherever possible, we follow every element of the rules on sustainability. The bar is set high, and we therefore invest a lot of time and resources in the search for new materials and testing them. We also convert used workwear into new items. We investigate new methods and work together with our suppliers who, for their part, follow environmentally friendly aims and practices.
Then sustainability is a fundamental aspect of innovation, as you just said. It is perhaps even the most important strategic target. What exactly do you try to achieve here?
Lena Bay Højland: We try to offer the most sustainable portfolio in the industry – not only in relation to the materials, which means high longevity. We develop models whose style and appearance will fit in our world for the longest possible time. They should be current for at least ten years and be selected over and over again because they completely meet the requirements of our users. We aim to produce designs that last, and that simultaneously fit the ‘Corporate Look’. We are certain that we have everything in our range that end-users need, but nothing more. Less is more. Short-lived fashion trends are different to workwear that has a different purpose, in our opinion. For all that, it has to be said that there is actually no such thing as sustainable working clothes. However, we try to make them more sustainable, and our aim is that around 50 % of our styles are made from more sustainable materials by 2025.
Sustainability has to be applied a various points – it is not just the materials but also the manufacturing processes, the use of energy, transport, etc. What can be most easily adjusted to reach the goal of sustainability?
Lena Bay Højland: The environmental product declaration EPD has shown that the factors with the most influence on sustainability are in the production and the coloring of material. The EPD is a very important instrument for our work. It brings light into the darkness in the form of measurements and everything that enables us to take sustainable decisions.
For example, a material that consists of recycled polyester is not necessarily more sustainable than one from new polyester if it has been manufactured using sustainable energy sources and coloring methods. That is why we need this information and the measurements; otherwise, you are misleading the end-users. This can be compared to buying an ice cream – you know that it has more calories than a piece of fruit. If the manufacturer says it is a low-calorie ice cream though, he has to prove it by stating the number of calories. This allows the consumer to make a comparison. But what is the situation with recycled polyester compared to new? How much emissions does each one cause? How can the consumer know?
How can the functionality of PPE and sustainability go together? Where do you see the limits of sustainability?
Lena Bay Højland: The decisive aspects here are quality and reusability. Not all recycled materials have the same level of quality – but we have to be 100 percent sure. When looking at the reusability, you have to consider that workwear consists of many different elements, strengthening and the like. We are faced with the challenge of making it possible to convert all that into new workwear. Stretch elements are very important – but they are difficult if not impossible to recycle. A further challenge is the percentage of refuse that we can use for new material: it has to be brought up to the level of quality that we normally deliver and not force us to make compromises. On the contrary, we must still deliver a high quality product.
The quality of our workwear actually gives us another opportunity – namely to reuse previously worn products again. Many items are not completely worn out, and so we can recondition them and put them into use once again in the company for which they were designed.
Trofta and Stiby are the current heat protection ranges from Fristads. Could you tell us about them?
Lena Bay Højland: These are the first heat protection ranges on the market without PFAS. They can be industrially washed and meet the EPD standard. They come in semi-stretch and stretch versions of natural and sustainable materials. They were developed together with end-users and given the required characteristics. They were also developed in close cooperation with laundries to make sure that they would survive numerous washing cycles and that they can be easily repaired, which lengthens their lifetime. We have also developed an intelligent sizing system that enables you to find the perfect size with the maximum comfort.
How many washing cycles are possible then – and how can that be increased?
Lena Bay Højland: That depends on the type of clothing. Winter jackets should be washed once a year at the most. Some are never washed, but we test such garments for up to 25 cycles, and up to 50 cycles for trousers. This is based on the available statistics. We test the workwear simultaneously on the job and in the laundry to reach as many cleaning cycles as possible. That is why it takes around two years to develop a new range of clothing. It is not a business for the impatient!
To finish, let us take a look at the forthcoming months. What new products can we expect from your company in the near future?
Lena Bay Højland: We launched another, completely new and sustainable workwear collection in spring. It is called Forsbo, and it was developed for industry, service and tradespeople. This has doubled our activity in environment-declared workwear in the corporate wear sector. It is a workwear design that is lighter, more comfortable clothing with a distinct design and modern fit. Forsbo is particularly suitable for larger companies where uniform workwear helps the teambuilding process. It works in exactly the same way as its bigger brother Skarup but at a significantly lower price. We are demonstrating that a sustainable company solution does not have to be expensive.
In fall, we will be launching a new multinorm collection with particularly high protection against electric arcs and with first-class comfort. Employees who are in areas where there is a danger of arcing deserve not only the highest protection but also highly comfortable clothes. The new multinorm collection called Talberget, approved to arc protection class 2, provides both. We have set ourselves the target of developing the most comfortable multinorm collection with arc protection class 2 on the market. The new collection is inherently flame suppressing, and was specially developed for electricians, electrical engineers and others working in the energy sector.
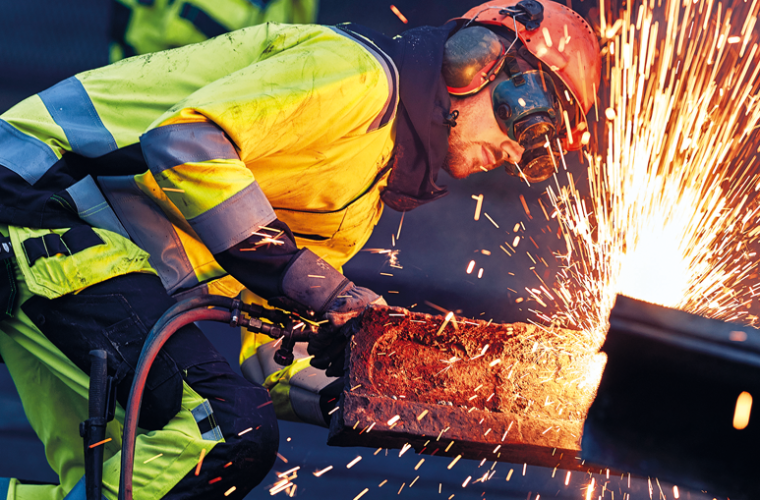
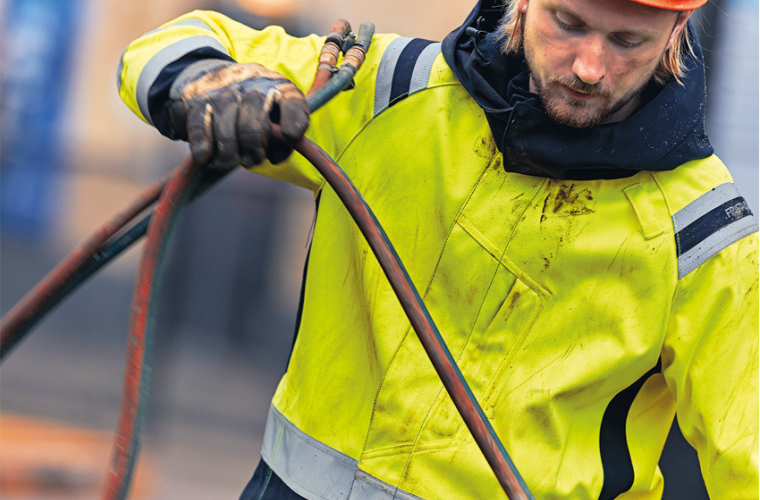
Business Partner
Fristads GmbHSüdportal 1
22848 Norderstedt
Germany
most read
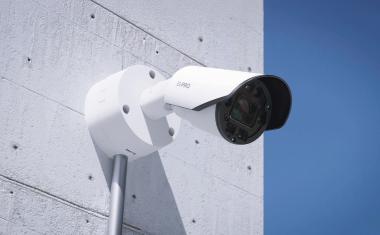
Visual Intelligence: i-Pro Combines Edge Analytics and AI with Quality and Integrity
Interview with Jose Riolobos, President of i-Pro EMEA, and Oliver Lincoln, Senior Sales Manager UK and DACH, about the company‘s evolution into a leader in AI-driven surveillance.
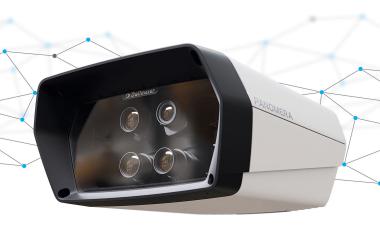
Panomera S4 Perimeter: For Sterile Zones and CRITIS Applications
Dallmeier has introduced the Panomera S4 Perimeter. The ‘Perimeter Panomera’ combines four sensors in one optical unit, which provides a resolution of 200 effective megapixels – MPe – per camera.
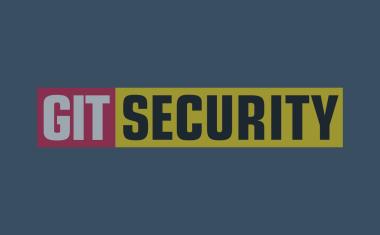
Prepare for the CER Directive
Securing Critical Infrastructure through Regulation
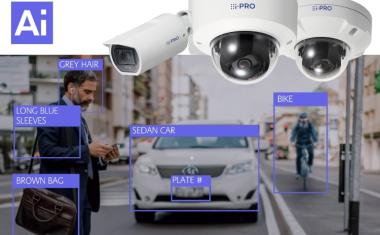
i-Pro on the Path to ISO/IEC 42001: AI Governance for Physical Security
i-Pro is the first company in the security industry to pursue certification for AI management systems under ISO/IEC 42001.
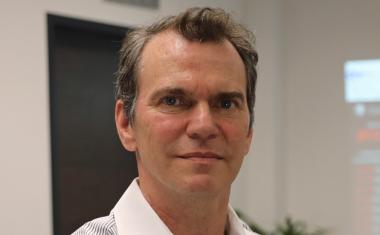
Global Security Strategies of the DHL Group
Frank Ewald (DHL Group) on Global Security Strategies and the Challenges of the Logistics Industry