Personal Protective Equipment: Safety Up, Cost Down
An integrated, cross-location concept for Personal Protective Equipment identifies potential savings and strengthens compliance with regulations
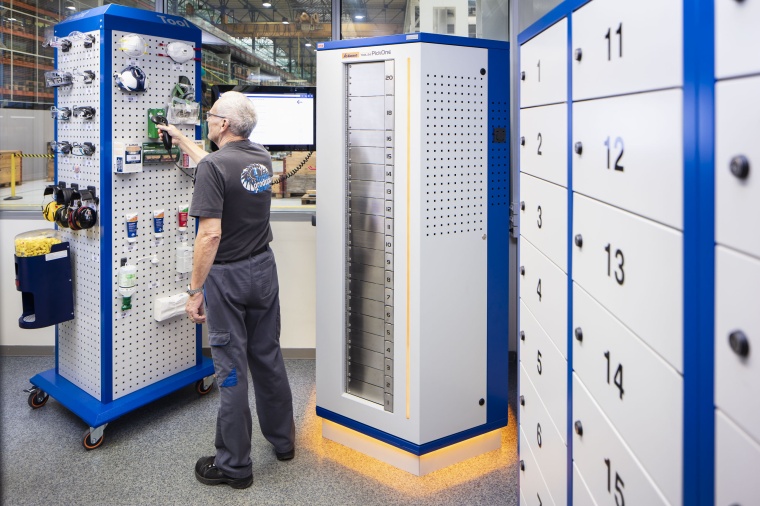
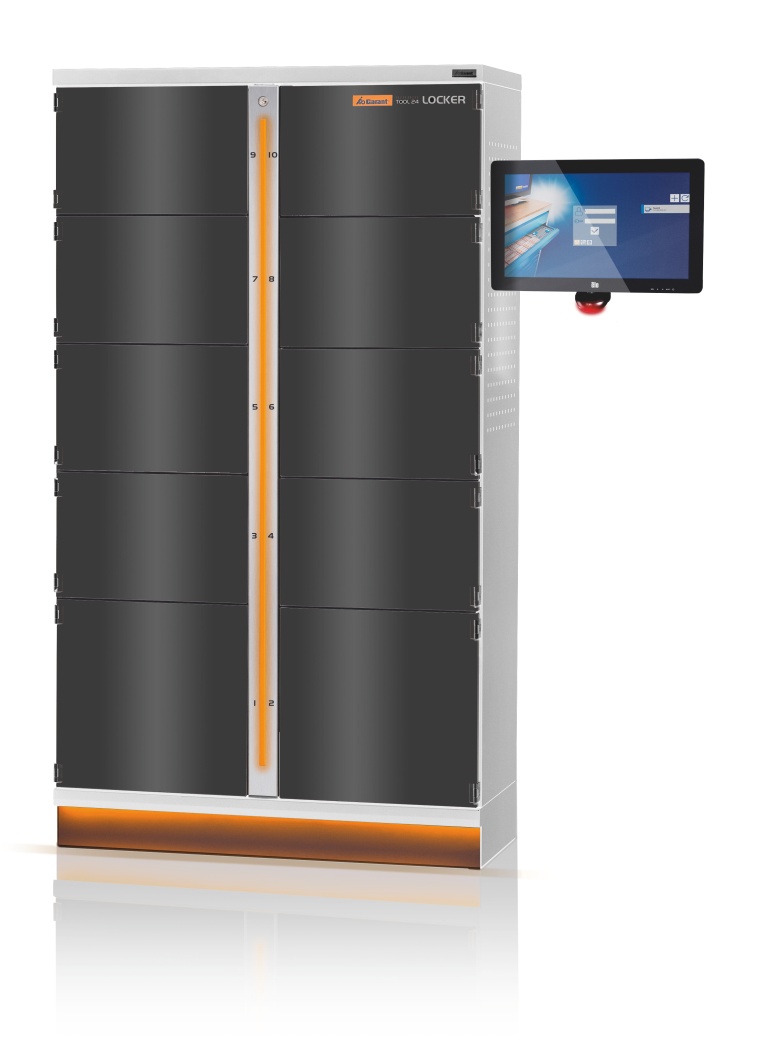
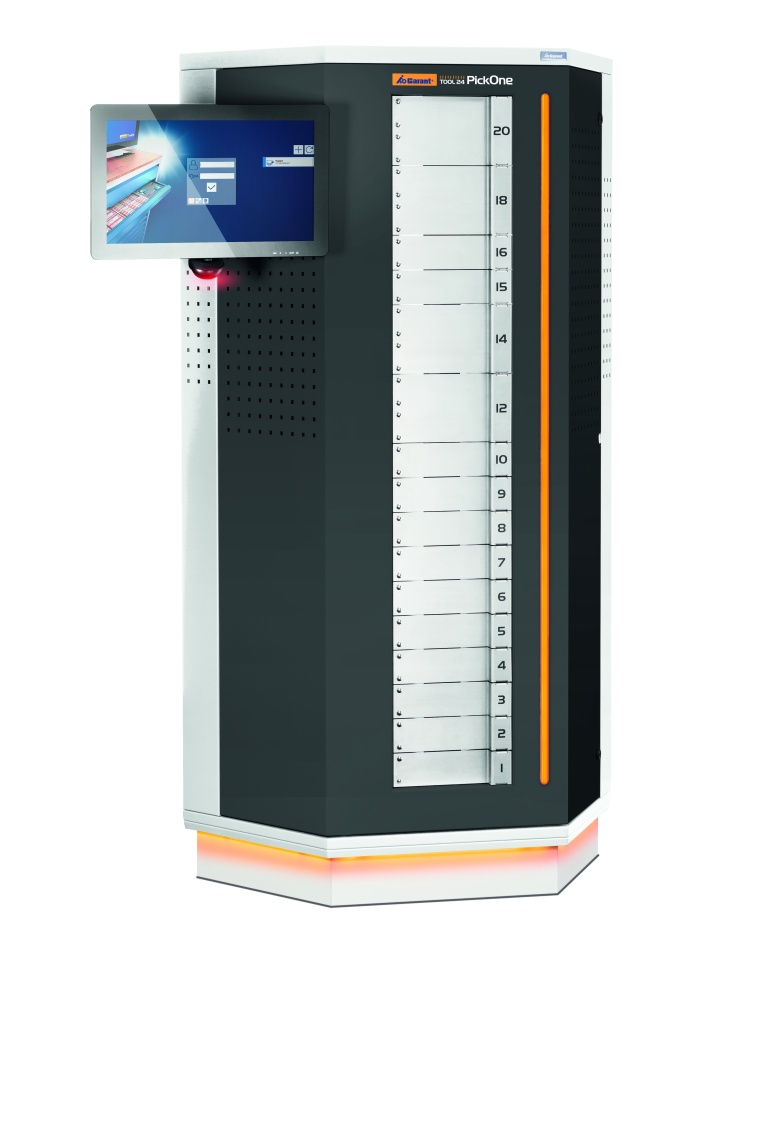
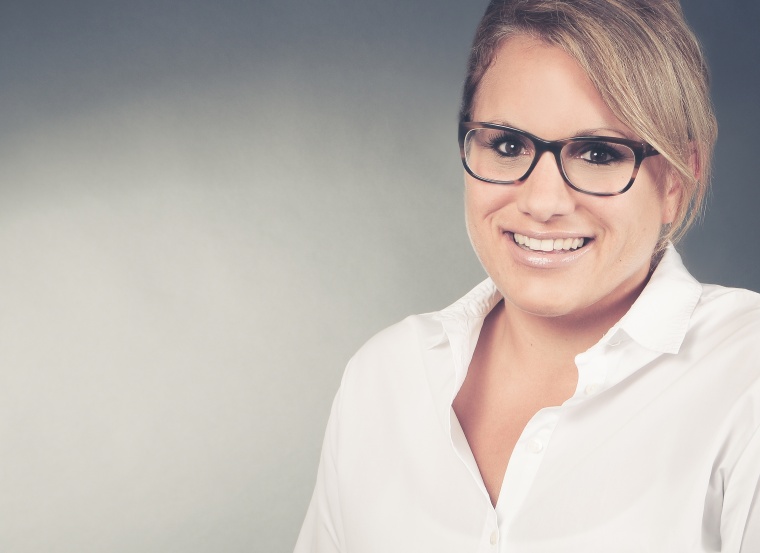
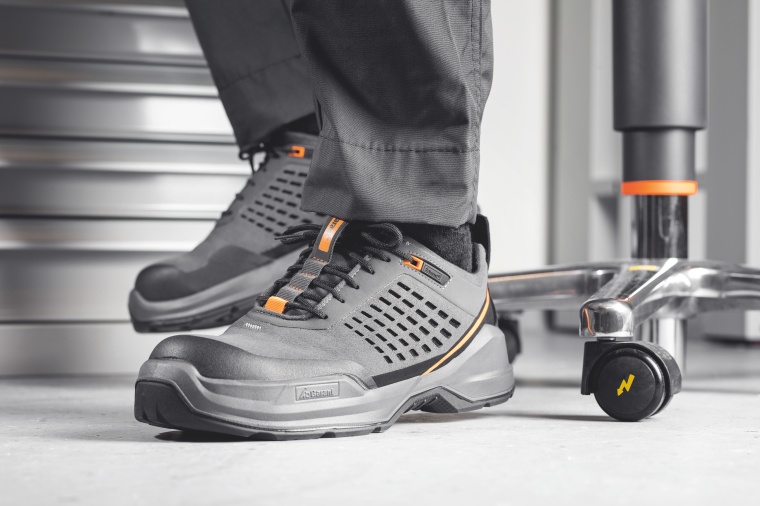
Many companies are starting to cut costs. Major expenditure is being scrutinised, including personal protective equipment (PPE). This is because consolidating PPE items and streamlining the associated procurement processes can reduce costs and increase safety at the same time. A holistic, cross-location concept is forming the foundation for this.
Reducing Uncontrolled Growth
The range of PPE products on the market has grown continuously over the last few years. In many companies, this has made the purchasing lists longer and more confusing. Often new products were added and employees also registered their special requests. Particularly in larger companies with several locations and decentralised purchasing, the lists and costs have grown wildly in many places. A consolidated and company-wide binding PPE standard catalogue and revised purchasing guidelines help to simplify PPE procurement and reduce special request orders down to a minimum. Health & Safety can also benefit from this, as only PPE that has been uniformly tested and reviewed is used.
Keeping Quality Standards High
To implement this successfully, it is important that all stakeholders concerned are involved and consulted in the decision-making process. Depending on the size of the company and its organisation, these may include, for example: strategic purchasers, company doctors, safety engineers, production managers, branch managers and, of course, the employees as wearers of the PPE. Experience has shown that a sustainable consensus can be reached quickly, especially if quality standards are kept high and the employees are not only able to examine the solution but also to test it and wear it. To define the minimum requirements and protection classes, it is necessary to classify and cluster the workplace requirements throughout the whole company. This requires detailed inspections of the workplaces and a risk analysis. In addition, the complete PPE product portfolio as well as the associated ordering processes must be scrutinised to define a standard catalogue and uniform ordering processes.
Multistage Process
Staff should be involved in the project from a very early stage. However, sensitivity and tact are required. To increase the acceptance of the project, start with less critical product areas such as head protection and only deal with those areas that cause more work in the case of an upcoming product change at the end. A more complex topic is, for example, foot protection, because every foot is different. For the perfectly fitting safety shoe, the feet of the employees must be measured exactly and any health requirements must be checked and recorded – this is very time-consuming. When it comes to safety shoes, it often makes sense to offer two models to choose from. Shoes with a multiple-width system and different cushioning classes are particularly comfortable. These will accommodate both narrower and wider feet and can be adjusted to the body weight of the wearer. The design of the shoes also plays an important role. After all, shoes should also be appealing and, if possible, match the corporate design of the company. The situation is different with hearing protection. Here, wearing comfort and quality are the most important factors. This also applies to hand, head, eye and respiratory protection. On the other hand, it is more difficult to choose protective clothing. After all, employees do not only want to be well protected and comfortably equipped, they want to feel comfortable and look good as well.
As wearing comfort is an important criterion for clothing being accepted by employees, all products should also be tested over a longer period by small pilot groups before they are included in the standard catalogue. A wearing test usually lasts four to six weeks. With an international workforce, it should be taken into account that ready-made sizes vary from country to country. For this reason, it is important to involve employees from all countries in the wearer tests and to provide intensive on-site support for European-wide projects. Also, it should be determined how many employees per department will accompany the wearing test to achieve a representative result for the entire workforce.
Individual Look in a Uniform
As uniform work clothing also strengthens the feeling of employee loyalty and togetherness, more and more companies are also providing work clothing for their employees. Particular importance is attached to complying with the corporate design guidelines. However, employees should still have a choice. In the case of outerwear, for example, this could look like this: a T-shirt, a sweatshirt and a polo shirt are available; the employee can choose two tops. To emphasise the corporate identity, the clothing is usually finished off with the company logo. This can be done by direct embroidery, embroidery emblem, transfer printing and laser engraving. Which method of finishing is used depends on the requirements of the textiles: For example, embroidery is not suitable for a soft shell jacket.
Bundled Orders
After the PPE range, the procurement processes are also scrutinised, because often a greater bundling of the orders can also mean considerable potential for savings on the cost side. Specialist dealers with a very wide product range are ahead of the game here. However, because PPE requires a great deal of advice, the PPE cooperation partner should also have a professional advisor at their disposal. They should be able to answer any technical questions on site and actively support the subsidiaries in carrying out wear tests, be able to help with training and instructing employees. Special orders should also be possible to maintain the necessary flexibility. How the procurement process for Personal Protective Equipment can be made more efficient and accelerated by 75% is shown by the experience of Man Energy Solutions at its Zurich site. There, the Hoffmann Group was listed as the main supplier, orders were consolidated, the Garant Tool24 PickOne single issuing system was introduced and the procurement process for PPE was fully automated.
Fully Automated Processes
When a minimum stock level is reached, Garant Tool24 PickOne automatically sends an order to the Hoffmann Group. This eliminates the need for purchase requisitions and individual orders. There is only one blanket order for a certain amount, which the automatically triggered orders are deducted from. If this amount has been used up, then the next blanket order is placed and the corresponding goods received posting is made. Any discrepancies between the quantities ordered and actually received are detected when the system is filled up. The PPE goes directly from goods received into the machine. The company has shortened the procurement process from five to eight days to two days. The Hoffmann Group delivers the goods within 24 hours after receiving the order. Garant Tool24 PickOne is then refilled by Man employees.
24/7 Availability
Goods issuing systems such as the Garant Tool24 PickOne also ensure that the required PPE is available around the clock. Also, with the help of integrated reporting, they make it possible to prove that each employee was able to remove the PPE required for him/her at any time. In addition to this, user profiles can be created in such a way that the employees only have access to the PPE items approved for their respective area of work. This increases safety in the company.
Conclusion
Standardising the PPE items to be procured in a standard catalogue and consolidating supplier(s) combined with automating the procurement processes even further can lead to significant cost savings. Also, it is possible to ensure that only those PPEs that meet the safety requirements exactly are purchased. This increases occupational safety. In the case of transnational projects and an international workforce, the project should be accompanied by highly qualified local consultants who can assess country-specific characteristics and take intercultural aspects into account.
Author: Alexandra Kovacs,Project Manager PPE, Hoffmann Group
Business Partner
Hoffmann SEHaberlandstraße 55
81241 München
Germany
most read
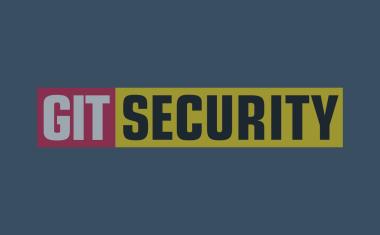
Prepare for the CER Directive
Securing Critical Infrastructure through Regulation
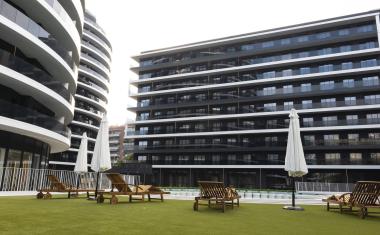
Mobile First is the 21st-Century-Experience
From Offices to Villas, Mobile Access Transforms Facility Security and Management
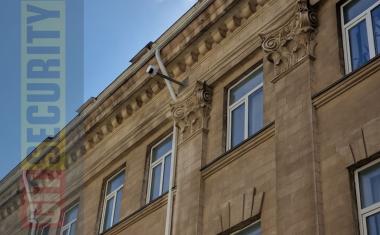
Why Building Façade Security Is Critical to Preventing Intrusions
Beyond the Perimeter: Strengthening Building Security Through Façade Protection
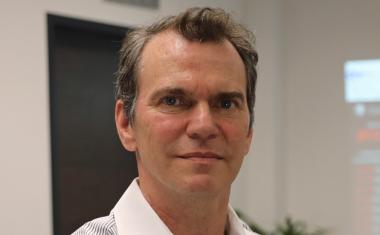
Global Security Strategies of the DHL Group
Frank Ewald (DHL Group) on Global Security Strategies and the Challenges of the Logistics Industry
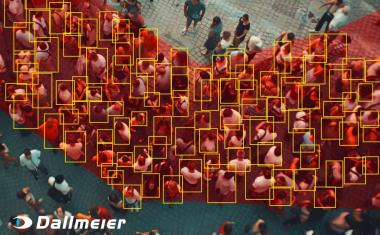
The Benefits of AI-based Video Surveillance Solutions for Sports Venues
Dallmeier Interview: Artificial intelligence Makes Stadiums Smarter