Pilz: support for the new Machinery Directive
Pilz: support for the new Machinery Directive. As the European Union has grown closer together there has been increasing harmonisation of laws, regulations and provisions. The Mach...
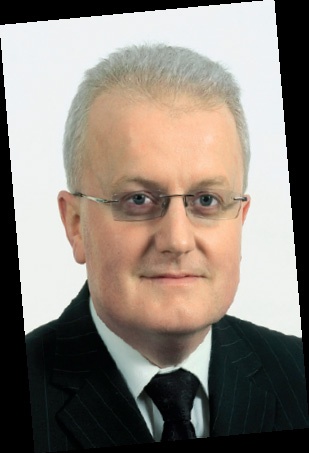
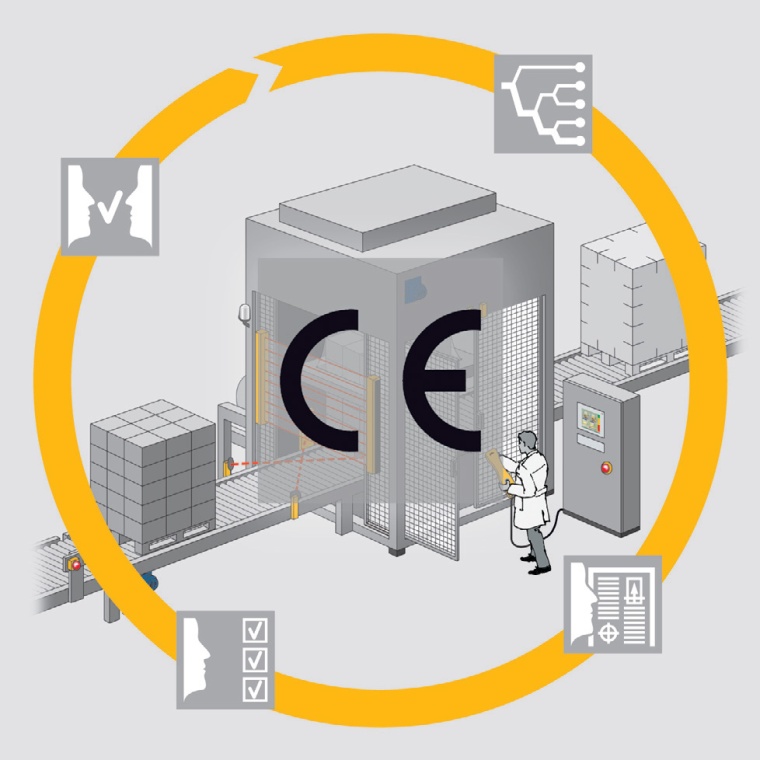
Pilz: support for the new Machinery Directive. As the European Union has grown closer together there has been increasing harmonisation of laws, regulations and provisions. The Machinery Directive has special significance in terms of the functional safety of machinery. Essentially it defines the standardisation of the European machine safety requirements and, along with other directives, aims to guarantee freedom of movement within the EU. With effect from 29.12.2009, the current version of the Machinery Directive – 98/37/EC – will be replaced by the new version – 2006/42/EC – and there‘s no transition period. That will mean a number of changes for manufacturers and operators.
According to estimates, approximately 500 million working days plus the corresponding turnover are lost each year in the EU as a result of industrial accidents. Even if industrial accidents occur only rarely when operating machinery, they still entail very high costs in terms of their effect on individual staff, the employer and the company. Studies produced by the Swiss organisation SUVA and the German Institutes BGIA (Institute for Occupational Safety and Health) and BAuA (Federal Institute for Occupational Safety and Health) describe how these major accidents still happen in our high-technology environment, with its strict safety requirements. Their report states that from more than 680,000 accidents involving machinery, 380 were fatal and 25 per cent of the accidents were attributable to manipulation of the safety systems.
Further studies showed that:
- Safety concepts that do not obstruct machine operation are not normally defeated.
- The probability that an inappropriate protection system will be defeated is directly proportional to the benefit that a machine operator expects to achieve from the manipulation.
The new Machinery Directive calls on machine manufacturers to consider the existing hazards and potential manipulations from the outset and deal with them appropriately in the machine design. Effective machine safety depends on compliance with directives and standards and on machine designers and manufacturers co-operating with those responsible for the safety concept, as well as machine operators and their supervisors. Pilz has always followed this approach, which incorporates the whole process as well as everyone involved. This approach is also evident in many of the changes in the new Machinery Directive.
Changes in Fundamental Areas of Safety
The new Machinery Directive involves some fundamental changes. These relate to the risk analysis procedure, technical documentation, safety system requirements, conformity assessment procedure and changes for machine manufacturers outside the EU.
Risk Assessment
The process of risk assessment has now been incorporated into the Machinery Directive: the machine manufacturer must ensure that a risk assessment is carried out. Through an iterative process of risk assessment and risk reduction, the manufacturer is called upon to exclude hazards and associated risks by taking the appropriate safety measures. This assumes that the machine’s risk assessment is carried out by a member of staff with an appropriate level of technical competence, who is able to perform the risk assessment and risk estimation as intended. Machine manufacturers must guarantee that this process is implemented effectively, record this in the machine’s documentation and refer to it in the operating manual.
Documentation
The safe operation of machinery depends on having clear instructions. From 29.12.2009, the machine manufacturer must not only describe the machine’s intended use in the technical documentation but also consider each foreseeable misuse. The documentation must be changed on the effective date, 23.12.09.
Projects occurring around the time of the effective date will generally need double documentation; at the very least, certificates will need to contain references to both directives.
Control Systems
One requirement of the Machinery Directive is that a failure or fault in the control system must not lead to a hazardous situation. A new feature is that potential “foreseeable human errors” are also considered. The resulting demand for ergonomic operation is to be considered at the safety system’s design stage, so that operators do not feel the need to defeat or manipulate the system.
Harmonised Standards
In a new article on “Presumption of conformity”, the new Machinery Directive highlights the benefit of achieving conformity through the standards. The standard EN 954-1 that describes the design and application of safety components in control systems is actually scheduled to cease on 29.12.2009. The final decision whether the transition period will be extended for three more years will not be reached before December 2009.
To be on the safe side machine manufacturers should apply either of the two standards EN ISO 13849-1 or EN/IEC 62061 to achieve compliance with the new Machinery Directive. The new standards take into account the increasing tendency to use electronic and programmable control systems within safety systems.
New Procedure for CE Conformity Assessment
New conformity assessment procedures have been defined for machinery listed in Annex IV of the Machinery Directive and for “partly completed machinery”. Manufacturers of machinery listed in Annex IV can now carry out self certification on the basis of the new, harmonised standards EN ISO 13849-1 and EN/IEC 62061.
Machine Manufacturers
Outside the EU Machine manufacturers outside the EU who wish to import machinery into the EU must commission a person established in the EU to compile the machine’s technical documentation. The easiest way for machine manufacturers without a base in the EU to meet this requirement is to name an “authorised representative”. So the authorities have a better way of following the conformity procedure and machine operators have greater security.
Timely, Careful Preparation
The new Machinery Directive shows operators and machine manufacturers a way to avoid serious accidents. In the initial phase, however, the legal changes are bound to cause some uncertainties. As there is no transition period, machine manufacturers and operators as well as manufacturers of partly completed machinery must start to prepare themselves now for the amended provisions and procedures. It’s also important to consider the new standards such as EN ISO 13849 in parallel.
Pilz provides services in CE marking and certification as well as training. These help machine manufacturers and operators to meet the requirements of the new Machinery Directive and ensure that machinery will comply on 29.12.2009. As machinery safety expert Pilz offers a comprehensive range of services for all phases of the machine lifecycle: from identification of the danger points through to implementation of safety concepts and integration of safety measures.
Working together with a company’s own technical staff, Pilz’s safety experts will guarantee compliance with legal requirements throughout the whole machine lifecycle. Pilz monitors the processes required to generate the necessary compliance strategies, safety designs and documents. As an authorised representative, Pilz takes responsibility for the administrative procedures required by the directive. SPS/IPC/Drives, Hall 9, Stand 350
Practical Example: Upgrading a Production Line
An operator wishes to upgrade his production line and put it into service in 2010. The production line will then consist of existing machinery, new machinery and new robot cells; the latter are to be regarded as partly completed machinery. Operators need to access the plant area for the necessary cleaning and maintenance work, and this represents a potential hazard.
In accordance with the new Machinery Directive, this production line is to be regarded as an interlinked plant comprising machinery and partly completed machinery. As a result, the operator of this production line becomes the manufacturer, and performs a risk analysis for the entire line.
A safety concept must be drawn up in accordance with the essential requirements of the Machinery Directive (Annex 2), and this must guarantee that the control system’s safety components provide a safe concept for the entire interlinked plant. As operators have to access the danger zones and not all areas of the production line are visible from the control station, the safety concept must be designed in such a way that the plant will not start if there is a person in the danger zone.
This can be guaranteed by new technologies such as the safe camera system SafetyEYE. Once the plant is finished, trained personnel must perform the necessary machinery safety risk assessment and risk estimation and produce the documentation.
Contact:
Pilz GmbH & Co. KG,
Ostfildern, Germany
Tel.: +49 711 3409 0
Fax: +49 711 3409 134
www.pilz.com
most read
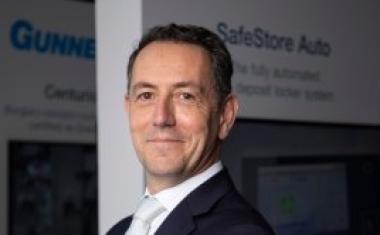
Protecting Valuable Items from Theft, Fire, and Unauthorized Access
GIT SECURITY Exclusive Interview with Emmanuel Harir-Forouch, Global Business Development Director at Gunnebo Safe Storage
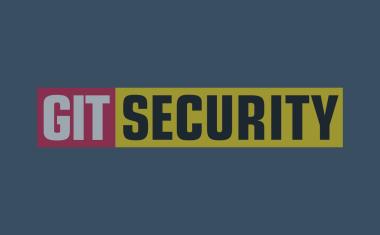
Prepare for the CER Directive
Securing Critical Infrastructure through Regulation
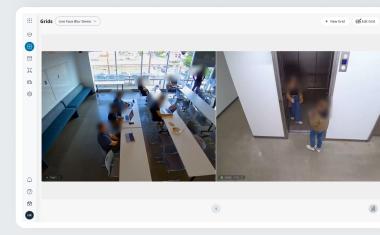
AI-Powered School Security: Verkada Now Trusted by 20 Million Students Worldwide
Verkada Secures 20 Million Students: How AI Is Transforming School Safety
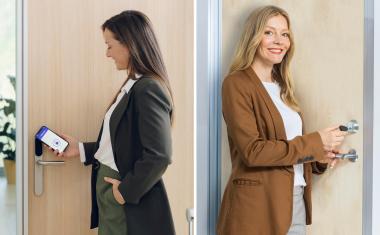
Assa Abloy's Commitment to Sustainability
How Sustainability Inspires Innovation and Product Design
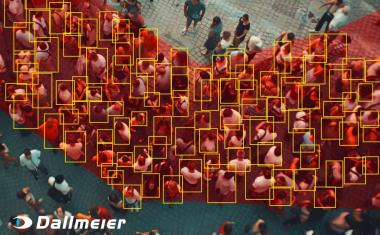
The Benefits of AI-based Video Surveillance Solutions for Sports Venues
Dallmeier Interview: Artificial intelligence Makes Stadiums Smarter