Sick: how EU Directives relate to Machine Safety – Part 5
Sick: how EU Directives relate to Machine Safety - Part 5. Whether switches or protective fences, whether light curtains or laser scanners: components alone do not make machines an...
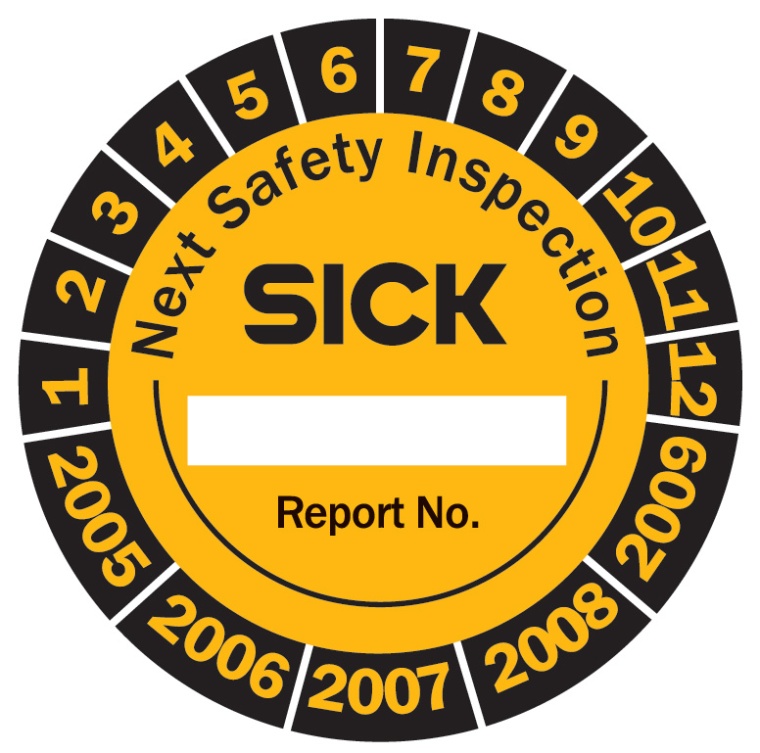
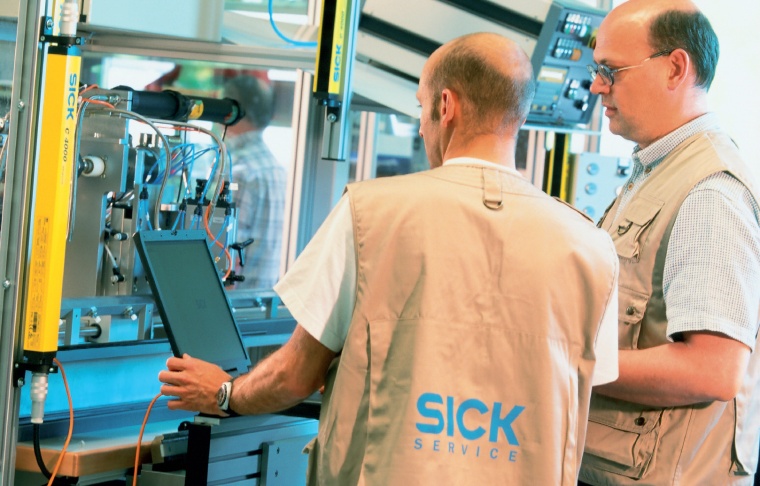
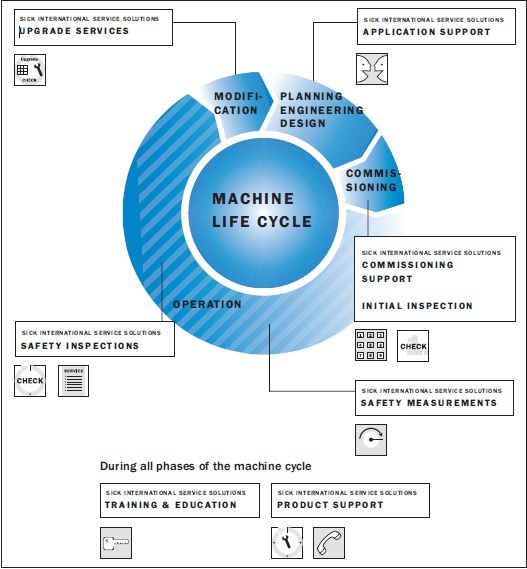
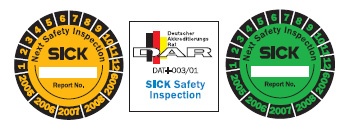
Sick: how EU Directives relate to Machine Safety - Part 5. Whether switches or protective fences, whether light curtains or laser scanners: components alone do not make machines and presses safe – the overall technical safety solution must be correct. Statistics compiled by Sick on the basis of several thousand inspections show, however, that more than half of all safety systems are incorrectly integrated. The training of machine producers and users; a range of specialised services; and accredited safety inspections are available to provide assistance.
Both safety at work legislation and the EU’s directive on works safety demand that a user determines, or employs someone to determine, whether the safety technology of equipment commencing operation is in order. This not only involves the actual protective systems, but also their installation and integration in the higherranking control level. Here, however, incorrectly integrated safety systems are found again and again. This is proven by random inspections which focused on power-driven machinery (44 % of all equipment tested) and hydraulic presses (39 %). This article completes the five-part series on the subject of safety technology, which has already looked at legal conditions, standard-compliant use, the concrete implementation of safety during the planning, construction and operation of a machine, and an introduction to the various safety approaches available.
Statistics Confirm: Safety Is More than a Product
The accredited safety inspections carried out by Sick experts on more than 10,000 machines over Europe formed the basis for the random sampling. The machines were equipped with a variety of protective equipment from differing producers. Results show that only 47 % of inspection seals were granted unconditionally, i.e. over half the machines failed to fulfil the requirements of the Machine Directive – and were thus not CE-compliant.
35 % of the machines received the inspection seal conditionally, and granting of the inspection seal was actually refused for 18 % of the safety systems inspected. Conclusion: 53 % meaning more than half of all safety solutions were unsafe at the time of the inspection.
The five most common reasons for refusing to award the inspection seal for powerdriven machinery were:
- incorrect integration of the safety sensors in the machine controller (28 %),
- the protective equipment did not affect all hazardous movements (26 %),
- the safety distance to the hazardous pointof- operation was too short (12 %),
- despite protection, the hazardous point-ofoperation could be accessed by reaching around, under or over (23 %),
- the control switch of the protective sensor could be actuated from within the hazardous area (11 %).
The results for the hydraulic presses were similar:
- incorrect integration in the control system (26 %),
- hazardous point-of-operation could be accessed by reaching around, under, over or from behind (35 %),
- the hazardous movement did not stop when the protective equipment was activated (10 %),
- safety distance to machine too short (10 %),
- protective equipment not effective during entire period of hazardous movement (19 %).
These faults cannot always be detected at first glance.
A Variety of Causes
There are various reasons for these shocking technical safety results. The most important include the increasing complexity of machines and plant, and thus the hazardous points-of-operation that are present, which are often not easily understood either by the user or the safety officer.
In addition, safety technology is continuously developing as a result of technological changes or amendments in the standards – necessitating appropriate personnel resources as well as regular updates in their knowledge. The most serious cause, however, is tampering with machines and their protective systems – often by the operators themselves! This was documented in a study called “Tampering with protective equipment on machines” published by the Trade Association of Industrial Safety (BGIA) in 2005, in which more than 900 companies participated.
These admit that, from their own experience, almost 37 % of all protective equipment is permanently or temporarily tampered with. The most frequent cases involve tampering during the correction of problems with the machine; during setting up, adjustment, modification or re-equipping during operation; and during cleaning and maintenance work. Those who carried out the tampering gave what they considered to be “good” reasons: to gain time and work more rapidly, to meet time and performance targets, to simplify certain operating modes, poor ergonomy of the protective equipment and more comfortable work.
But there was also a lack of awareness of the hazards. In almost 10 % of cases the tampering was even described as “necessary for the work process”. And tampering is quickly carried out: according to the BGIA study, the modifications only took an average of less than 12 minutes. This 12 minutes, however, saved the operator an average of almost 60 % of the time required for, say, correcting a problem. And in three out of four cases no great technical effort was required for the tampering.
Although in 90 % of the cases it would have been easy enough to reverse the changes to the safety technology, this was actually only carried out in less than one-third of the cases. This could have serious consequences – though not necessarily for the person who actually did the tampering – if, for example, a colleague operates the machine after a change of shift and he or she relies on the safety of the machine, unaware of the changes made.
Finally, the BGIA study also makes clear that mechanical protective equipment (e.g. cladding, fencing, screens in combination with position switches or pressure mats) are far more often tampered with than non-contact systems based on light, laser, heat, ultrasonic or transponder technology.
Technological change; insecurity about legislation and standards; the failure to consider new, hitherto inconceivable, methods of tampering; and lack of awareness of the health and liability risks brought about by tampering have prompted Sick to offer a wide range of training courses, safety inspections and service options, in addition to its safety products and system solutions, on the basis of the principle that “Safety is more than a product”. This is made possible by more than 50 staff – trained experts on Qualification Level 2 (according to §10 of the Safety at Work Directive) and with many years’ experience.
Technical Safety Training: Sensitisation and Knowledge Transfers
Constructors, Project Managers, Managing Directors or users – safety technology affects all of them, though with different emphases. Whether hand protection or liability – the steadily increasing interest and need for specific information are met by technical safety user training and specialist seminars for differing target groups. The spectrum ranges from the principles of machine safety and CE-certification during the construction of machines, plants and control systems, to safety at work legislation in daily practice and the liability risks and legal consequences for plant constructors and users.
Additional trainers include experts from Germany’s Federal Ministry for Labour and Social Affairs, the Trade Association of Precision Mechanics and Electro-technology, or the Administrative Corporation (ADCO) of the EU’s Market Supervisory Board for Machines. The target-group-specific events increase the participants’ awareness of the subjects and provides them with access to the complex materials on machine and plant safety appropriate for their needs and questions.
Safety with Inspection Seal Better than a “Safe” Feeling
On the basis of regulations that are valid throughout Europe, users must carry out regular inspections of technical safety systems to check whether the protective equipment provides optimum accident prevention for the plant during operation. Thus an equally regular update of knowledge involving product expertise, advances in applications, and the current regulatory position is vital if one wants to run a machine or plant with lasting safety.
Only in this way can users meet their technical safety responsibilities and simultaneously provide meaningful support for their quality and safety management systems. As such management systems, however, often tie up increasingly limited personnel resources in their works, a significant trend towards employing external safety service providers is becoming evident. In this area, Sick is the first producer of safety systems to offer safety inspections accredited by the Deutschen Akkreditierungsstelle für Technik e .V. (German Accreditation Agency) in line with EN 17020, Type C, for the electro-sensitive protective equipment segment (such as light curtains, photoelectric switches, or laser scanners).
The protective measures directly connected to these safety systems are also examined during these inspections, e.g. emergency stop buttons, two-hand switches, enabling switches or protective doors. The main aspects examined are:
- the effectiveness of the protective equipment with proper use,
- the Safety Category of the protective equipment, with regard to the hazards present,
- the integration of the protective equipment up to signal transfer to the controller in the necessary Safety Category, and
- the potential circumvention of protective equipment.
Whether initial commissioning, regular inspections or stoptime measurement – the Sick inspection seal confirms the successful implementation of the accredited inspection of the protective equipment. Protective equipment inspected with recognised testing methods and objective test reports ensures a high safety standard. The customer or user gains a variety of advantages from this, including:
- CE-compliant safety technology on the machine,
- support for the company’s Safety at Work Department,
- comprehensible, documented results for the company’s own quality management system,
- increased plant availability through early detection of safety risks, and
- reduction of the liability risk, evident from the inspection seal awarded.
Range of Services for Productive Safety
The continuous efforts to minimise a plant’s total cost of ownership through maximum possible availability is also reflected in a rising demand for the provision of services. This starts right at the start of the life cycle of a machine, in the form of support for technical safety projects, because planned safety ensures correct device selection as well as correct integration in a machine concept.
The “Installation and Commissioning” service package includes final installation, adjustment, programming and testing of the installed safety technology, as well as the instruction of relevant personnel. During machine or plant operation, service contracts for regular safety inspections, e.g. during planned machine downtimes, ensure maximum possible protection against unforeseeable problems.
Furthermore, the EU directive on the use of equipment demands regular inspections of protective equipment. Which is why more than 2,000 Sick customers in Germany alone have such a service contract – which also, if the worst comes to the worst, assures them top priority to correct any problems.
Parallel to this, the Repair and Exchange Device Service guarantees rapid repair or the delivery of a replacement device within one working day.
Keep Away from Do-it-yourself
Whether training courses, accredited safety inspections or the provision of specialised services – high-quality services are to be preferred to do-it- yourself, especially in safety technology, if one wants to ensure safety, keep costs under control and minimise liability risks.
There are, however, very few companies worldwide that offer a comprehensive range of safety technology, accredited services and the professional, well-trained personnel necessary for this.
Contact:
Gerhard Dieterle and Simon Köpfer
Sick AG,
Waldkirch, Germany
Tel.: +49 7681 202 0
Fax: +49 7681 202 3863
info@sick.de
www.sick.com
most read
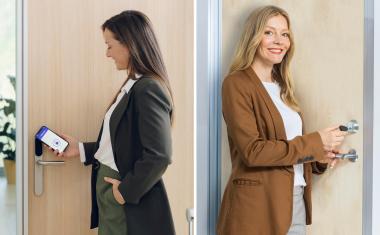
Assa Abloy's Commitment to Sustainability
How Sustainability Inspires Innovation and Product Design
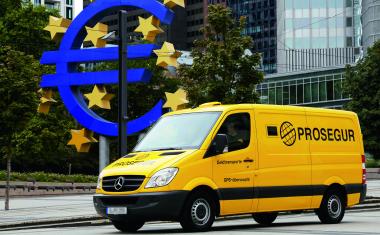
Prosegur‘s Commitment to Cash Management and Security
Interview with Michael Leppler, Prosegur Germany Head of Sales & Marketing
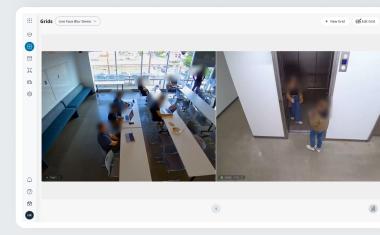
AI-Powered School Security: Verkada Now Trusted by 20 Million Students Worldwide
Verkada Secures 20 Million Students: How AI Is Transforming School Safety
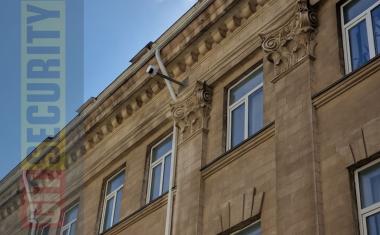
Why Building Façade Security Is Critical to Preventing Intrusions
Beyond the Perimeter: Strengthening Building Security Through Façade Protection
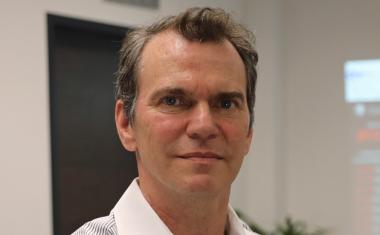
Global Security Strategies of the DHL Group
Frank Ewald (DHL Group) on Global Security Strategies and the Challenges of the Logistics Industry