Freely programmable encoder for EtherNet/IP
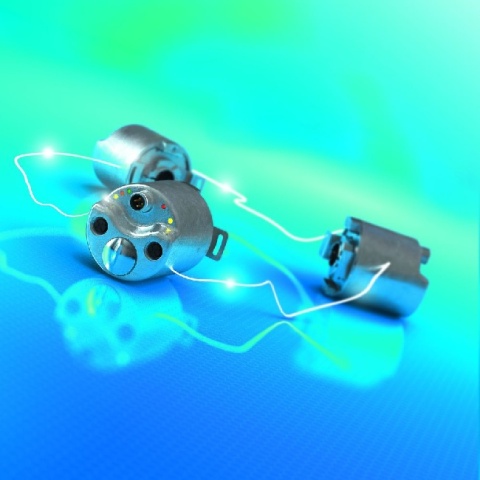
Intelligent, powerful, precise – the freely programmable absolute encoder in the AFS60/AFM60 EtherNet/IP family of products from SICK offers flexibility combined with fieldbus connection. In addition to comprehensive diagnostic possibilities and the integrated transmission function for rotary axes, its Device Level Ring functionality (DLR) allows active and continuous monitoring of network ring topology and its participants.
The AFS60 EtherNet/IP single-turn encoder and the AFM60 EtherNet/IP multi-turn encoder are the first EtherNet-based fieldbus encoders in SICK’s portfolio. In sensor terms, they are charac-terized by their great robustness and precision. Worthy of special mention, because unique to this extent, are their comprehensive diagnostic possibilities with which they optimize security against failure and increase plant availability.
Added value through diagnosis
The diagnostic functions integrated in the EtherNet encoder from SICK include monitoring of the temperature within the encoder. On reaching the defined minimum or maximum limit value it generates a message to the controller indicating the start of a potentially critical operating state. In addition, all encoders are equipped with two operating hour counters – one starts when power is supplied while the second counts the time of actual shaft rotations. A total of five dual LEDs on the encoder show the current operating state of the two ports, encoder functions and data transfer. Programmable position limit values can also be monitored – an important example of cam switching functions. Finally, the detection of speed or rpm protects the encoder and the entire plant from overloading. The individual messages are hierarchically structured in the form of so-called flags, alarms and warnings, depending on their importance for the current operating state.
Active recognition of device and network faults
SICK’s absolute encoder with the fieldbus interface EtherNet/IP complies with the current speci-fications of the ODVA (Open DeviceNet Vendor Association). The highlight is its DLR functio-nality (Device Level Ring). With this network monitoring system information packages, so-called beacon frames, are sent from the encoder via its dual port switch at brief intervals. In this way, the sensor carries out continuous and active availability tests on the network participants as well as on the connections between them. In the case of a fault, a change in direction of the beacon frame transmission in less than 3 ms restores communication between the devices and the controller.
Rotary axis function in the multi-turn version cuts programming and hardware costs
The AFM60 EtherNet/IP multi-turn encoder has another feature that reduces the time and cost of machine integration: the rotary axis function. It is necessary for, among others, rotary tables and drives with transmission or reduction gears. The rotary axis function allows the steps per rotation to be represented as a fraction. For this purpose, the total number of steps in the en-coder is set, i.e. the resolution of an application in relation to the gear transmission ratio (e.g. a rotary table drive). In the case of the resolution per rotation, position values can also be displayed in a non-binary form in this way. Regarding the number of rotations, it is possible to display the resolution in decimal form. The rotary axis function saves the machine constructor complicated drive calculations and control programming – and thus cuts costs during installation, maintenance and service.
Why an encoder with EtherNet-based fieldbus interface?
As is now common for sensors, the topic of fieldbuses is also gaining in importance for encod-ers. New controllers on the market increasingly do without an auxiliary port and are instead ex-clusively equipped with, for example, an EtherNet/IP interface. At the same time, controller pro-ducers offer their EtherNet-based fieldbus interfaces at relatively attractive prices. Consequent-ly, many machine constructors are also retrofitting existing machine generations with EtherNet-based fieldbus systems. Simultaneously they expect special, improved, performance from this upgrade. Because, in communication terms, sensors can offer added value as participants in fieldbus networks, EtherNet-based fieldbus components, in particular – for example the encod-ers of the AFS60/AFM60 product family from SICK – are becoming increasingly important.
Universal fields of application
The AFS60 absolute single-turn encoder and the AFM60 absolute multi-turn encoder from SICK are rotative sensors for path, angular, speed and position detection. Because the encoders are freely programmable they are the ideal solution for producers and integrators of production processes, handling systems, production machines, print systems, as well as measurement and inspection equipment.
More EtherNet encoders from SICK will follow shortly for PROFINET and EtherCAT.