Box Clever: How to Secure Goods in Logistics Centers while Maintaining Transparency
The department store or logistics center is the pivotal point in the supply chain and ranks among the most complex areas in the economic system. With so many shipments, however, a ...
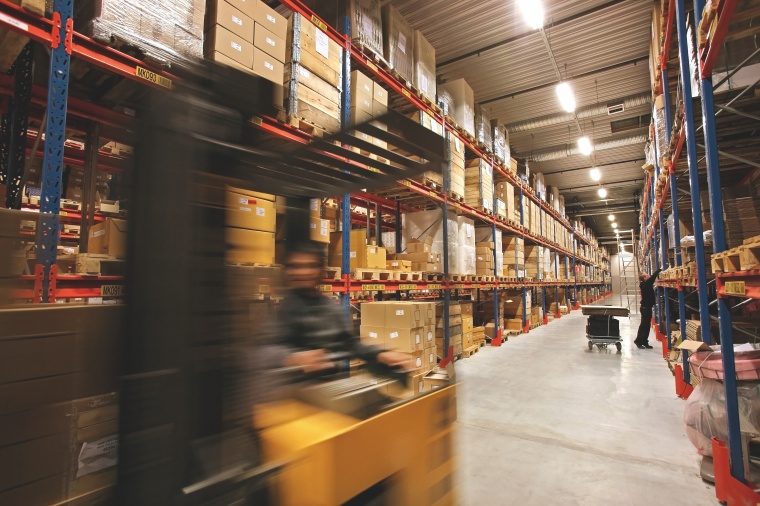
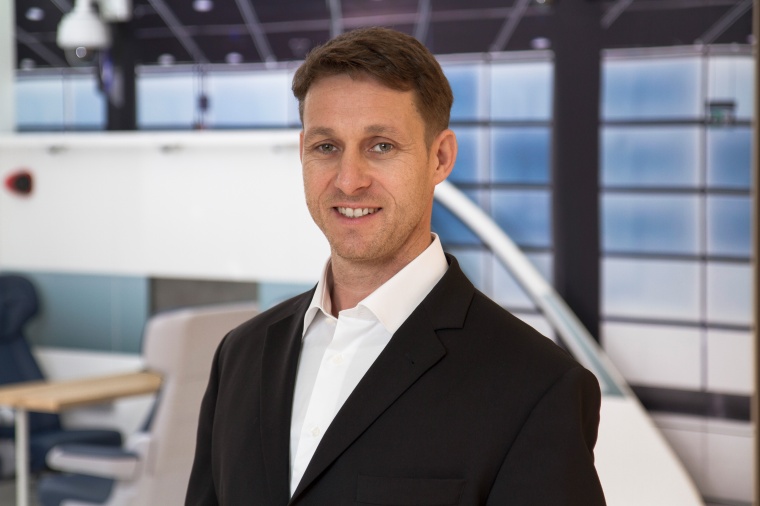
The department store or logistics center is the pivotal point in the supply chain and ranks among the most complex areas in the economic system. With so many shipments, however, a logistical nightmare can quickly arise, because in practice, goods are either damaged, inadequately packaged, incorrectly dispatched or stolen. It is therefore crucial that the path of a parcel can be traced (back) seamlessly. Jan Engelschalt, Business Development Manager Transportation at Axis Communications, looks at some solutions.
The entire global economy depends on goods being reliably transported from A to B. However, the management, assignment, storage and forwarding of goods that take place between these two stations represent a highly complex overall process, which requires the exact tracking of each individual item – especially because third-party suppliers or other companies are usually involved in the supply chain. This inevitably raises the question of how transparency is possible in this complex environment. How are goods secured? How is a customer complaint clarified?
Securing Buildings, Premises and Vehicles
First and foremost, it is necessary to ensure that the buildings, premises and vehicles are secured against unauthorized access and theft. Physical security is achieved with an intelligent network video system, which generates high resolution pictures around the clock, no matter what the weather or lighting conditions. In this way, deviations can be detected quickly. Secondly, IP access control solutions, which can be integrated into the video system, provide comprehensive security for the premises and buildings. In this way, access can be granted only to authorized persons or vehicles with a registered license plate. In the event of unauthorized access in certain areas, automated warning signals can be sent.
Tracking Goods
Goods might be stolen from a logistics center or get damaged due to negligence or errors in the process sequence. If they get damaged, are wrongly packed, misdirected or stolen, this may result in complaints.
Logistics centers usually have modern Warehouse Management Systems (WMS) which are, in most cases, connected to a software program for automatic identification and data collection (AIDC), such as RFID technique (Radio Frequency Identification). This transmitter-receiver system is able to identify and locate objects using radio waves automatically and without any contact. This means products are scanned on arrival in the warehouse and are thus traceable over time. However, this method quickly reaches its limits, since scanned data do not allow subsequent visual inspection of the goods. They do not provide information about what happened after the scanning process, resulting in a loss of transparency and time-consuming and costly investigations with unclear results in the event of complaints.
Tracking Goods with Visual Recording
Visual goods tracking is a useful supplement to bar code scanners. In this way, goods can be captured by high-resolution cameras on arrival at the logistics center and tracked by a seamlessly installed camera network, even in poor lighting or weather conditions. The solution can be easily integrated in the WMS and AIDC system, combining video data with location data to visually track the entire flow of goods and view individual events more closely. To do so, you just need to enter the ID number of the package into the software. This allows the operator to know the exact status of the goods, who came into contact with which products, and when and what effects this may have had.
This makes it clear what happens to a certain packet after the incoming scanning. If a customer has a complaint or repeated deviations in the process are detected, the pictures not only show what happened, but can also serve as evidence. This optimizes processes, reduces losses and increases profits. Furthermore, the cameras can be used for training purposes and to manage personnel deployment more efficiently.
With visual goods tracking, customer complaints about lost goods are quickly processed and facts are completely clarified. This creates trust and demonstrates excellent service and precision, which significantly enhances the brand and image of the company. And both time and money can be saved by processing receivables and complaints quickly and efficiently, reducing the costs of compensation, fines and insurance. Visual goods tracking provides an intelligent and economically sensible supplement to conventional tracking services in logistics centers in every respect.
What Cameras do in a Logistics Centre:
- Cameras show the condition in which goods arrive in your warehouse, before they become your responsibility. Wide Dynamic Range (WDR) and HDTV provide sharp pictures, even in the poor light of loading ramps.
- Cameras that are mounted on the ceiling above the quality control area record the process of unpacking and checking in detail. Irregularities and defects are documented.
- Cameras on the transport belts record the entire route of packets as well as the particulars of packets nearby. Cameras in ‘corridor’ format are ideal for this task. You can save money by optimizing the video and minimizing memory storage requirements.
- Cameras on the ceiling or high on the wall show individual items in detail from above, including labels, damaged packets and missing elements. They also provide a good overview of the entire goods flow.
- Cameras above or beside the workstations record every detail – both the handling of packets and missing parts.
- Cameras also record the condition that goods are in when they leave your premises. You receive clear pictures thanks to WDR and HDTV.
Business Partner
Axis Communications ABGränden 1
223 69 Lund
Sweden
most read
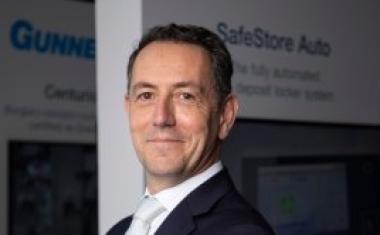
Protecting Valuable Items from Theft, Fire, and Unauthorized Access
GIT SECURITY Exclusive Interview with Emmanuel Harir-Forouch, Global Business Development Director at Gunnebo Safe Storage
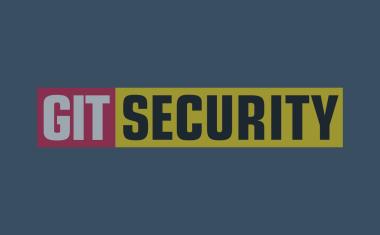
Prepare for the CER Directive
Securing Critical Infrastructure through Regulation
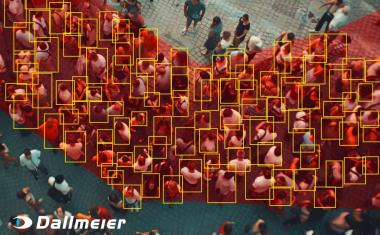
The Benefits of AI-based Video Surveillance Solutions for Sports Venues
Dallmeier Interview: Artificial intelligence Makes Stadiums Smarter
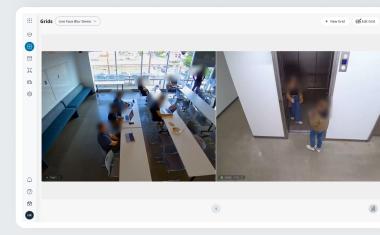
AI-Powered School Security: Verkada Now Trusted by 20 Million Students Worldwide
Verkada Secures 20 Million Students: How AI Is Transforming School Safety
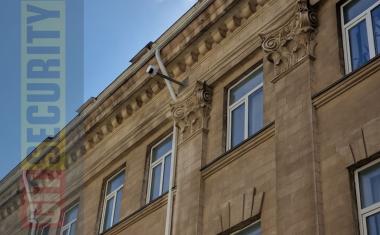
Why Building Façade Security Is Critical to Preventing Intrusions
Beyond the Perimeter: Strengthening Building Security Through Façade Protection