Merck Headquarters with Electronic Locking System and Flexible Access Organization
The oldest pharmaceutical/chemical company in the world has its headquarters in Darmstadt, Germany. This site of Merck has now been partially modernized with an electronic locking ...
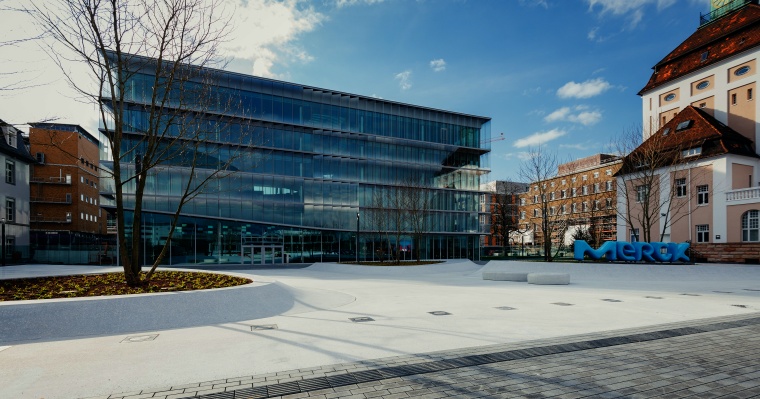
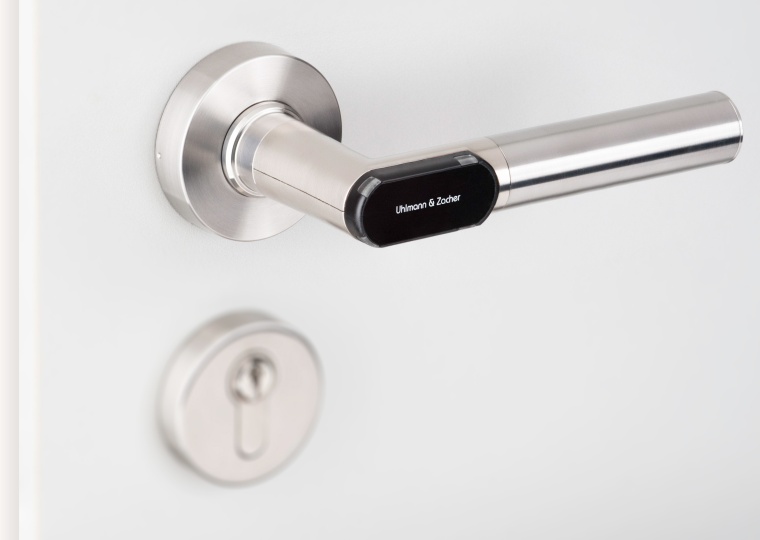
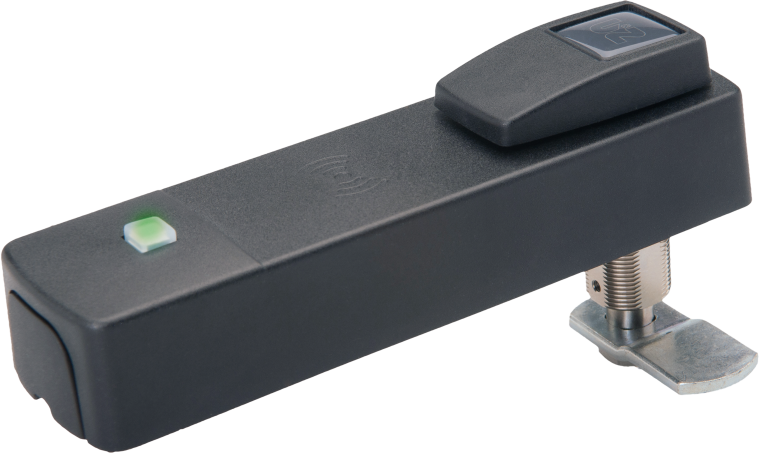
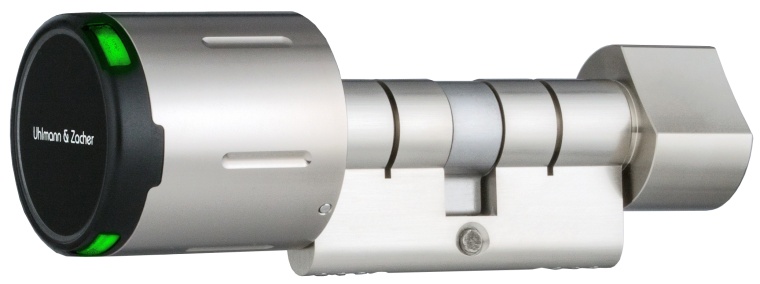
The oldest pharmaceutical/chemical company in the world has its headquarters in Darmstadt, Germany. This site of Merck has now been partially modernized with an electronic locking system from Uhlmann & Zacher to meet the needs of a modern, dynamic working environment. The aspect of access control has gained in administrative flexibility and convenience in daily use through the new electronic locking system. The electronic and the mechanical systems are running in parallel and complement each other.
Merck develops products and services that find application in almost every aspect of life: from medication and foodstuffs through environmental analysis to new materials for architecture and technology. The scientific and technology company was founded in 1668 by Friedrich Jacob Merck in Darmstadt – today, it counts among the most important pharmaceutical and chemical companies worldwide. Around 51,000 employees work for the organization, 12,800 of those in Germany. The headquarters of Merck, the holding company for the operative business of the Merck Group, is in Darmstadt.
Partial Modernization with an Electronic Locking System
In 2018, Merck celebrated its 350-year company anniversary. The partial modernization of the headquarters with an electronic locking system fits well with this event. Apart from the mechanical locks, there was also an electronic system with around 1,000 cylinders. This has now been replaced and significantly expanded. Around 6,000 electronic components have been installed over the past few years.
An electronic locking system is a sensible alternative to a mechanical one for the company because some departments relocate within the available buildings at regular intervals. Flexible adaptation of the access system is enabled by the Keyvi administrative software from Uhlmann & Zacher and thereby a quick reaction to changes. The individual authorizations can be changed simply with a few clicks of the mouse. In total, the locking system at the headquarters now incorporates around 35,000 cylinders. It is in fact a combination of mechanical and electronic systems – this provides optimized access control for the site.
Consultancy and Project Support
It was important for those responsible for implementing the changes that there should be competent advice and support throughout the project. The local company Georg Jungblut Sicherheitstechnik was in attendance at Merck from the planning stage right through the implementation of the mammoth task. Merck‘s system administrators were given corresponding training on the use of the new locking system.
Out of approximately 6,000 already installed electronic locking units about 4,000 were electronic knobs, double knobs and half-cylinders. The latter are used in the padlock version. In addition, electronic door handles and door fittings are in use, which provide a great deal of flexibility because of the wide range of types. The electronic locking system, however, is not limited just to doors and gates; furniture can also be integrated into the system. Lockers and cabinets have also been secured by electronic cabinet locks – and they can be included in the Keyvi administration with a few clicks of the mouse.
Authorization Linked to the Staff Number
A specialty of this particular installation lies in the software. In the software from Uhlmann & Zacher, normally the serial number of the transponder is obtained by the readers, to which the relevant access authorization is stored in the Keyvi software. This is how access is granted, or not as the case may be. Uhlmann & Zacher has made some customer-specific changes though in the software for Merck.
In this case, the authorization is not linked to the serial number of the transponders but instead to the staff number stored on the ID card. So every staff ID card that also works as a transponder contains the respective staff number, with which the corresponding authorization group can be determined by a reader in the Keyvi software. This is effectively an interface to staff management with many advantages for efficient workflow. The staff ID cards are cards with the Mifare Desfire transponder technology. They conform with the latest security standards and are therefore the preferred transponder technology of Uhlmann & Zacher.
As all the electronic staff ID cards had first to be changed from Mifare Classic to Mifare Desfire, Uhlmann & Zacher also developed a special solution for this. A tool was compiled that buffered the data so that it could be reliably transferred from the old cards to the new ones. The staff ID cards are also used in third-party systems for time and attendance recording and canteen accounting.
Flexible Management of Authorizations
Of the already ca. 26,000 issued transponders, around 15,000 also have an electronic authorization and can therefore also be used by staff for time and attendance control and canteen accounting. Meanwhile, the number of electronic locking units at Merck has been growing at an enormous rate – in 2018 about 2,000 to 3,000 locking cylinders were fitted in just the one year and incorporated into the system.
Every transponder card is assigned to a group that contains individual authorizations. The system administration is carried out using the Keyvi software by employees of the company itself after undergoing training by Georg Jungblut Sicherheitstechnik. This administration software enables changes to be easily made to authorizations. And of course, lost or missing transponders can be rapidly barred and new authorization quickly and simply transferred to another transponder.
External service companies and staff who are visiting the site for maybe just a day are also issued with an ID card and will be registered in the software. They are added to a group in the system and granted the corresponding access authorization. This allows them to move around the corresponding parts of the site flexibly and simply.
Extra Groups
Another peculiarity of this installation is that, apart from the standard 296 usable groups that are almost all in use, a large number of the optional additional 5,000 extra groups are also being used. Currently this amounts to some 3,500 extra groups. So basically every necessary authorization group can be formed that is required. Last year, a total of 220,000 electronic authorizations were issued, both individual and group authorizations. It is also possible to react quickly to lost transponders. As soon as one is reported, the corresponding ‚key‘ can be barred in the software. Then the authorizations are written onto a new transponder and this is issued. Misuse of the lost transponder can thereby be easily prevented.
In total, 167 buildings were partially upgraded from a mechanical locking system to an electronic one, or the old electronic system replaced. The electronic locking system from Uhlmann & Zacher makes the administration of locks at Merck particularly flexible. Prompt and rapid adaptation of authorization is available at any time. This enables the whole locking system to be adapted to current daily requirements in accordance with the security plan.
Those responsible for the system are very flexible – in spite of which, the highest security standards will be maintained. The regular relocation of accommodation doesn‘t present a problem, whereby the most differing needs of the various departments can be met. The existing mechanical locking system is very well supported by the electronic locking units.
User-friendly for Employees and Visitors
A further intention of the upgrade was to make the electronic locking system as user-friendly as possible for both external visitors and staff. So the electronic locking cylinders, door handles and door catches, programming terminals and cabinet locks could be used intuitively and the introduction phase from mechanical to electronic could run smoothly. The whole locking system is set up to meet the needs of a modern working environment through the partial upgrade and the demand-oriented interaction of mechanics and electronics.
The high level of flexibility in the application of an electronic locking system convinced the staff responsible for security at Merck. The company uses all the capabilities that the Keyvi administration software has to offer the user. The standard available software from Uhlmann & Zacher was tailored to the individual needs of the company, and further adaptations of the software are possible.
The electronic system will be progressively expanded. After completion of the upgrade at the headquarters in Darmstadt as well as at two further locations, further projects of this type at company locations around the world are possible. The successful cooperation with Uhlmann & Zacher and Georg Jungblut Sicherheitstechnik will be continued to this end.
most read
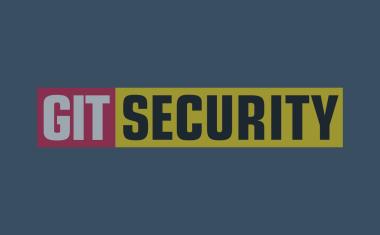
Prepare for the CER Directive
Securing Critical Infrastructure through Regulation
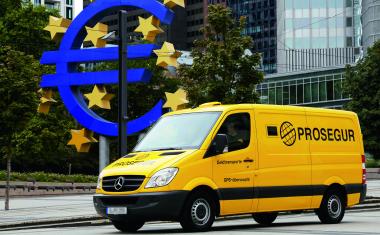
Prosegur‘s Commitment to Cash Management and Security
Interview with Michael Leppler, Prosegur Germany Head of Sales & Marketing
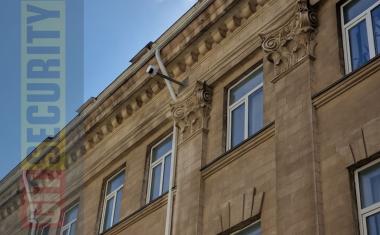
Why Building Façade Security Is Critical to Preventing Intrusions
Beyond the Perimeter: Strengthening Building Security Through Façade Protection
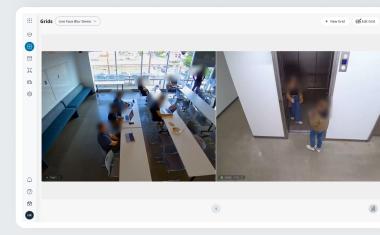
AI-Powered School Security: Verkada Now Trusted by 20 Million Students Worldwide
Verkada Secures 20 Million Students: How AI Is Transforming School Safety
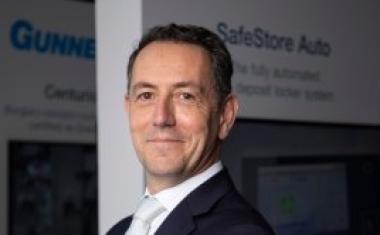
Protecting Valuable Items from Theft, Fire, and Unauthorized Access
GIT SECURITY Exclusive Interview with Emmanuel Harir-Forouch, Global Business Development Director at Gunnebo Safe Storage