Passive Fire Protection: “Cost Shouldn’t Come First”
Following the disastrous fire at Grenfell, it was reported that the intumescent cavity closers, installed as part of the external elevation, were the wrong way around. This meant t...
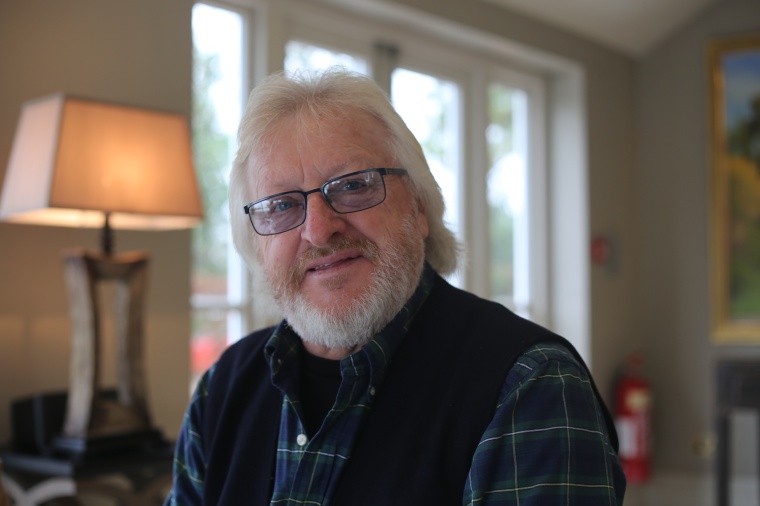
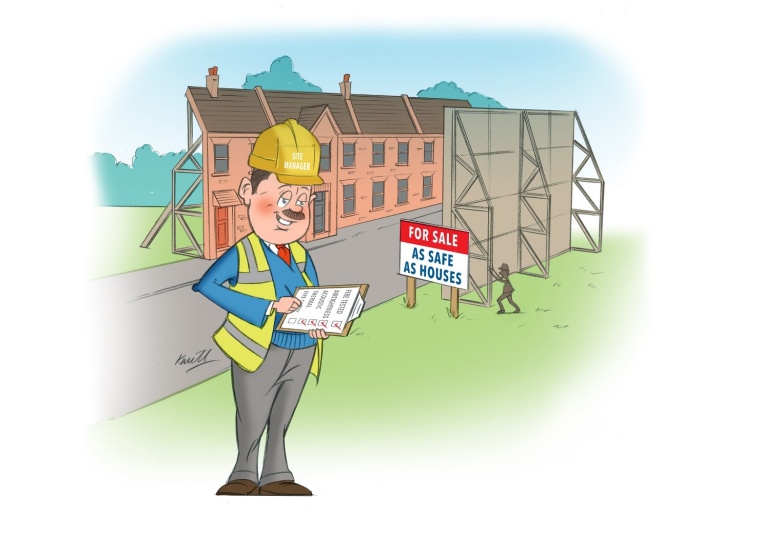
Following the disastrous fire at Grenfell, it was reported that the intumescent cavity closers, installed as part of the external elevation, were the wrong way around. This meant that the under-fire barrier could not react to the fire in the right way and close the cavity to prevent it from moving upwards throughout the building. This mistake throws into question how it actually happened, if the fire protection or cladding company were qualified and doing their jobs competently, and whose responsibility was it to check the sub-contractors’ work?
There appears to be a glaring problem in the industry. There’s clearly insufficient policing of what is being installed and how it’s being done. In times gone by there would be a Clerk of the Works, however it seems that this role has almost died out because of a cost cutting exercise – so does the responsibility now lie with the project or site manager, sub-contractor or main contractor? The truth is, nobody knows the answer – and that’s the problem. Liability dodging, cost cutting and pure lack of organisation in the chain of command between specification, installation and maintenance is for me, the biggest challenge and the biggest problem our industry faces and is currently ignoring – which is lethal.
Do Standards Fall Short?
In particular, there appears to be a lack of understanding in relation to fire control and what is required to reach even the most minimum standards. Whether the necessary performance is 60 minutes, 120 minutes or even higher, there is very little understanding of the differences between reaction to, and resistance to, fire and the nuances between the two. For example, specifying a Euroclass A.1 doesn’t mean that it will achieve a 60-minute performance. There needs to be more education around reaction and resistance and how both need to be considered during the early stages of design.
If we take insulation as an example, there has been a big focus on CO2 reduction and thermal properties by both the construction industry and by government, and cuts were largely achieved by adding combustible insulation to the building envelope, particularly in high rise structures, without proper focus on the safety implications in terms of fire. This is where fire protection considerations lack the priority they deserve. It should be thought of as something as essential as the foundation of the building or the envelope, and built into initial designs and within products, not just an after-thought near the end of the process to make sure a box is ticked. It’s putting people’s lives at stake and it’s hard to understand why it’s not taken as seriously as it should be.
Interrogating the Industry
When it comes down to it, it could be argued that there are two parts of the build program that require immediate attention:
- The overall design, especially ensuring that the priced project with the ‘equal and approved’ reference meets the performance requirement on all levels, and in particular against fire.
- The necessity to supervise and police the construction program to ensure that nothing less than the correct products are being installed in the correct way by the correct and qualified contractors and that they are then maintained correctly.
It seems like a mammoth task, particularly to an industry that is notoriously slow and resistant to change, but as the situation needs improvement, we need to consider how we can remove as much risk as possible with a few simple alterations. Don’t forget, breaking it up into smaller tasks all adds up. So, greater levels of control are needed across:
- Materials – ensuring they’re part of an umbrella accreditation and testing system to ensure consistency and compliance from all manufacturers.
- Cost shouldn’t come first – this goes for material substitutions and contractors. This mindset does and will continue to risk people’s lives.
- Control over quality – there needs to be a clear chain of authority on builds to ensure that there is a central role overseeing the products, installation and construction methods across all trades on-site to ensure everything is correct.
- Traceability – All components in fabricated systems need to be marked and logged to ensure if the worst does happen, the sub-contractors and manufacturers involved are held accountable and can work to resolve the problem, so it doesn’t happen again.
- Flexibility in design – Architects and clients need to have a greater understanding over the limitations of certain materials and their costs so there is less chance of specifying something that will need to be altered at a later date.
Controlling Off-site Activity
We can begin to achieve these smaller changes from the very beginning of the construction process, and I believe we can take some important learnings and lessons from off-site manufacturers. They use monitored and checked components to make sure their products meet the performance specification, and by introducing quality checks and tests during component assembly in the factory environment. It is fairly simple to develop and implement industry-standard certifications - particularly with everything managed in one place and dealing with fewer suppliers. And of course, when taken to site for installation, the workforce is skilled, qualified and have up-to-date knowledge of the products, but most importantly, they should consider the building as a ‘system’ not just individual components. I believe this is the key. We need to work towards developing a complete solution using off-site construction or at the very least, those using traditional methods of construction need to learn from new methods, rather than push against it. Staying stuck in our ways is costing people their lives – is anyone prepared to say that’s OK just because that is the way it has always been done? I’m not.
Successful Construction
Whether the method of construction is simple panelized or through-wall construction detail, inner or outer face, the most important thing is that the products used are certified and have been fully tested for thermal, acoustic, fire, airtightness and environmental certifications. Properly certified through a third party not self-certified. Marking your own homework was always easier!
Looking to the Past to Inform the Future
Back in 1996, an article was published by The Royal Academy of Engineering titled ‘Where is the Henry Ford of Future Housing Systems?’ This is a question some of us in the industry are still asking today. Although the market has been slow to change, partially because that’s the nature of the industry, offsite manufacture seems to be heading in the right direction. Expanding this thinking into all construction market sectors could happen, but measures need to be taken to ensure that quality control over components being manufactured develops ahead of the game, so that clients and specifiers can have peace of mind over what they’re buying. Let’s face it, we’ve got a lot of catching up to do!
When it comes to construction, the lowest cost shouldn’t be the first consideration. Yes, cost-effectiveness is important, it’s a business after all, but it shouldn’t take precedence over building safety, quality or performance. Research and due diligence are key to helping the industry improve its standards and refusing to work with sub-quality contractors and manufacturers is one simple step on the journey to change.
I have worked in the construction industry for 40 years and it’s easy to see where things have, and more importantly, have not moved forwards. But it’s only when I think about this as a family man that it really starts to hit home. Would I let my kids drive a car that hadn’t been properly safety tested, and regularly serviced? No. Would I want to fly in a plane where cost-down was the primary focus when it was built? Absolutely not - no-one would. So, why do we accept anything less than properly constructed, safe buildings to live and work in?
We know what needs to be done, it’s now about making the change happen. Drawing inspiration from more modern methods of construction and similar industries, particularly where manufacturing and installation is present, means that we can translate the same high standards and way of working so that we move away from being driven by cost, to be driven by quality and safety.
Doing nothing because making change is hard has never been, and will never be, a good enough excuse. No builder goes to work to try and build a second-rate building – so let’s go back to basics and change the foundations, literally, of how we work.
Sources: https://interestingengineering.com/25-extremely-embarrassing-architectural-failures
Business Partner
Zeroignition102-1819 Granville Street
B3J 3R1 Halifax
Canada
most read
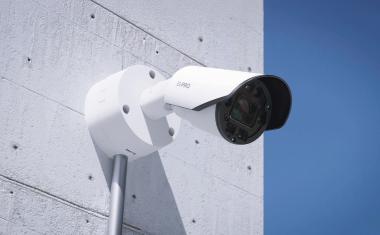
Visual Intelligence: i-Pro Combines Edge Analytics and AI with Quality and Integrity
Interview with Jose Riolobos, President of i-Pro EMEA, and Oliver Lincoln, Senior Sales Manager UK and DACH, about the company‘s evolution into a leader in AI-driven surveillance.
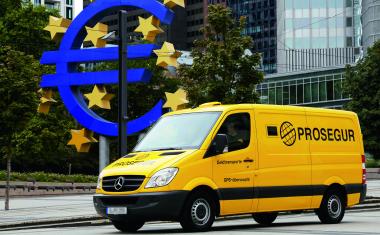
Prosegur‘s Commitment to Cash Management and Security
Interview with Michael Leppler, Prosegur Germany Head of Sales & Marketing
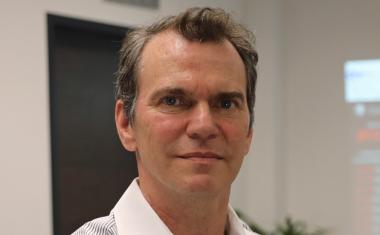
Global Security Strategies of the DHL Group
Frank Ewald (DHL Group) on Global Security Strategies and the Challenges of the Logistics Industry
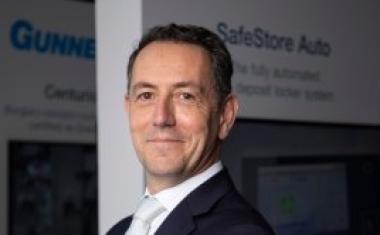
Protecting Valuable Items from Theft, Fire, and Unauthorized Access
GIT SECURITY Exclusive Interview with Emmanuel Harir-Forouch, Global Business Development Director at Gunnebo Safe Storage
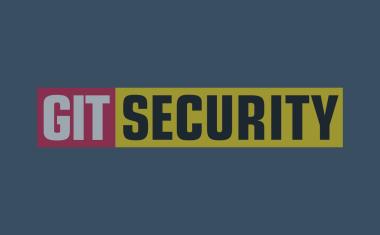
Prepare for the CER Directive
Securing Critical Infrastructure through Regulation