Security at the Largest European Airfreight Hub
The DHL Air Hub Leipzig has been in operation at Leipzig/Halle airport for almost five years. Along with Hong Kong and Cincinnati (USA), this is the central European hub of the wo...
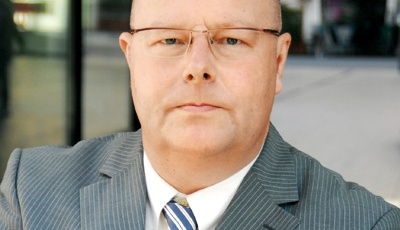
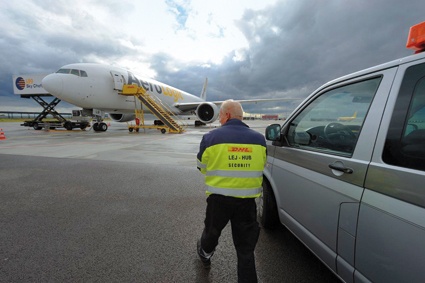

The DHL Air Hub Leipzig has been in operation at Leipzig/Halle airport for almost five years. Along with Hong Kong and Cincinnati (USA), this is the central European hub of the worldwide airfreight division of the Deutsche Post. Just the building complex alone covers 23,000m² of hangar area and 48,000m² of warehouse space. A further 200 hectares is taken up by the apron and numerous properties. The enormous logistics center is the destination for more than 50 DHL freight aircraft every day and each night over 1,500 tonnes of freight are handled. Comprehensive and very special security solutions are necessary here. Our Scientific Editor, Heiner Jerofsky, spoke with the Head of Security of the DHL Hub Leipzig GmbH, Philippe Bauer, about logistics security and about the special challenges of efficient personnel and technology management at the largest European airfreight hub.
GIT-SECURITY.com: The entire DHL Air Hub Leipzig system has been in operation now for five years. What experience have you had with the original security architecture? Where did something have to be improved or modified?
Philippe Bauer: Right from the beginning, the specialty of our airfreight hub here in Leipzig/Halle has been that we have direct access to the air-side area. Our airline EAT (European Air Transport) operates a so-called discretionary area here according to §9 of the Air Transport Law. This demands an appropriate security plan that has been approved by the LBA (Federal Civil Aviation Office) and is regularly checked. The security technology chosen at the project stage has provided reliable service. Only a few components such as video servers have been exchanged. The independent security network has proven itself and here too a few additions have been made. Only a new ID management system has been introduced so far and we are currently looking at a possible comprehensive security management system. The right choice of security technology service provider and maintaining a strict maintenance agreement contribute greatly to the reliability of the systems.
The shifting and storage of large amounts of freight also attracts the attention of criminals. And such an air transport hub must be protected against terrorist attacks. What precautions are in place in your security planning?
Philippe Bauer: The parcels that arrive at our hub are not stored at all but forwarded the same night. Up to 250,000 parcels are redirected every night in our warehouse. All our employees are checked with the police before starting and receive their contract only after confirmation of the so-called ZÜP (reliability check). Every new employee goes through a training program on the subject of security even before he receives official access to the security area. In addition, we carry out checks when employees and visitors leave our air-side area. As from 2013, DHL will also be rolling out the ‚Certified International Specialist Program‘ with an 8-hour security training session for all employees worldwide. With regard to theft, we definitely employ preventative measures. After the events in Yemen, the DHL directors decided to check all incoming parcels as they enter the airfreight network. This decision was accompanied by a large investment plan to increase detection capabilities at the various locations. We are very proud to have integrated an automatic X-ray machine here in Leipzig that allows us to check significant volumes of freight in a very short time. The system helps us to efficiently implement the current requirements of EU law as well as those of other air security authorities. Again, the focus here is on prevention by detection, deterrence and delay. We work closely together with the security authorities in this area and practice for emergency situations. Last year we were able to increase the number of authorized personal goods screening staff with an additional ‚Freight‘ training by 80%. As well as this training effort, we also have X-ray machines with so-called ‚dual-view technology‘ and numerous explosives detections machines.
Do you use your own security personnel and, in the light of experience, which jobs have you assigned to external resources?
Philippe Bauer: Security is the be-all and end-all in our division. For this reason DHL Hub Leipzig GmbH employs almost 200 of its own people to cover all the security tasks, including safety at work and our company fire brigade. If we occasionally have staff shortages we will use qualified personnel from temporary employment agencies.
How and at what central location do you coordinate all the operational messages such as burglary and equipment failure reports, video analyses or access control and do you have response teams on site?
Philippe Bauer: We have an internal security center and over 600 surveillance cameras installed around the site. Predominantly the borders of the secure area are watched and all the aircraft and freight on the apron are also protected. The security center also acts as the emergency control room where all failure reports and emergency calls are received and the responses coordinated. All responses are carried out by our own response teams and supported if necessary by the authorities and the airport fire brigade. As well as the security center, there is also an ID point that carries out access checks 24/7 and is responsible for issuing the ID badges.
Over 600 cameras are used to monitor the area, the buildings and the freight. Have dome and fixed cameras proved their worth with regard to image quality, speed, sensitivity and reliability and can intelligent systems be recommended in a logistics environment?
Philippe Bauer: We are very happy with our choice of various types of camera. In some exceptional cases we have considered replacing dome cameras by fixed ones. This has usually been due to building alterations. If we install new cameras they will definitely be HD-capable devices. We have observed a continuous development in the market of intelligent systems. However, any upgrading will happen piecemeal simply because of the above-average dimensions of our sorting system.
Perimeter protection is essential for such a large and important compound. How should our readers imagine the compound security along its very long edges?
Philippe Bauer: We have a security fence built according to ICAO standards that is protected by regular personnel rounds as well as by a combination of video and alarm reporting technology.
An ID card system with reliable identification and access control is an important element of the whole security concept. How do you prevent unauthorized people entering the area with a stolen or forged ID card?
Philippe Bauer: Every employee ID card is uniquely associated with a corresponding picture. If one is lost it can be remotely barred so that access to the site without being noticed is no longer possible. Visitors have to register with us by showing a valid form of identification. Access to the secure area is also only possible with this ID card in combination with a biometric comparison. This is done with a vein scan of the person assigned the ID card. This very efficiently prevents any misuse of ID cards.
The entire security hardware is dependent upon the emergency power supply. How do you ensure the necessary failure protection and at what expense?
Philippe Bauer: Like many other companies of our size, we also have emergency power generators that maintain the power in our house for a while. In addition, the critical elements of the security infrastructure are equipped with their own uninterruptable power supplies. The effort is very comprehensive and costly, but unavoidable however in order to ensure complete security of the location.
To what extent are you responsible for Aviation Security and how are you able to ensure the security of the aircraft that are parked in the area, the staff and equipment?
Philippe Bauer: We have a team of employees that carry out checks on the aircraft with every loading or unloading procedure. In addition, the aircraft stands are secured by light sensors and will raise the alarm if crossed without authorization.
Shifting enormous amounts of freight from aircraft to trucks and following the load requires a very high level of logistics effort. How and with what personnel and technical resources do you manage to keep the logistics chain intact?
Philippe Bauer: On six nights every week up to 60 aircraft land here and 80 trucks arrive to transport more than 200,000 parcels to and from our hub. The loading and unloading of aircraft and trucks together with sorting and the customs formalities requires close cooperation between all sections. Around 500 employees work on the apron who, together with more than 1,000 employees in the warehouse per shift, ensure the smooth flow and timely forwarding of all the freight. The processes are supported by various EDP systems that are being constantly developed further to meet the operational requirements.
The security team ensures as trouble-free and interruption-free operation of the DHL Air Hub Leipzig as possible. How do you estimate the current security situation to be and how well are you prepared for unusual interruptions and crises?
Philippe Bauer: We evaluate the current security situation on the basis of all the information that is available to us. We receive this not only from official sources but also from the airline industry. In addition, our colleagues from the worldwide security network are able to supply us with topical information. An employee in our quality and control department is responsible for emergency and crisis management, right through to ‚business continuity management‘. Exercises are regularly carried out across various departments and different scenarios are tested. These can be, for example, a breach of the security fence, a bomb threat or incidents involving aircraft. Of course, there are plans in place for this critical location to minimize the effects of such an event.
Many thanks for the open discussion and the interesting insight into your difficult daily job. We wish you continued good luck and the necessary intuition for these important tasks.
most read
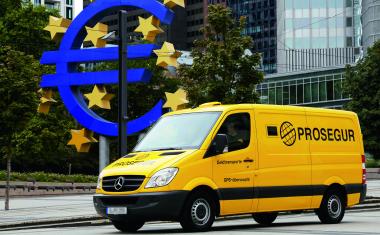
Prosegur‘s Commitment to Cash Management and Security
Interview with Michael Leppler, Prosegur Germany Head of Sales & Marketing
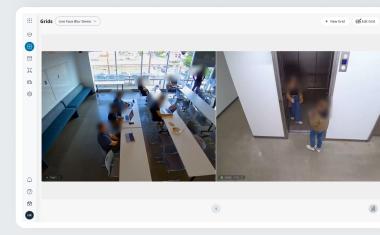
AI-Powered School Security: Verkada Now Trusted by 20 Million Students Worldwide
Verkada Secures 20 Million Students: How AI Is Transforming School Safety
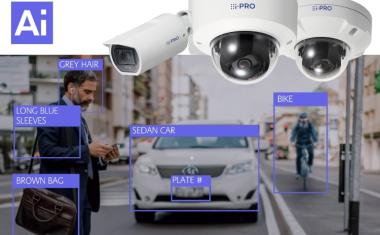
i-Pro on the Path to ISO/IEC 42001: AI Governance for Physical Security
i-Pro is the first company in the security industry to pursue certification for AI management systems under ISO/IEC 42001.
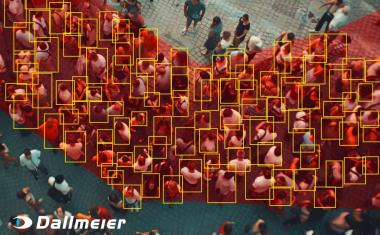
The Benefits of AI-based Video Surveillance Solutions for Sports Venues
Dallmeier Interview: Artificial intelligence Makes Stadiums Smarter
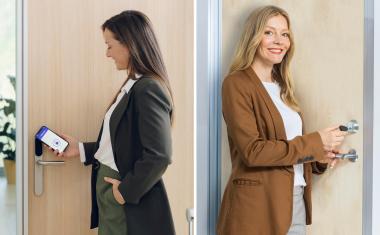
Assa Abloy's Commitment to Sustainability
How Sustainability Inspires Innovation and Product Design