Effiziente Intralogistik mit Sensortechnik von Leuze
Die Zukunft der Intralogistik ist leise und fast unauffällig. Wenn fahrerlose Transportfahrzeuge durch die Werkshallen gleiten und Docking-Stationen präzise bestücken, geht das nahezu lautlos vonstatten. Eine derart effiziente Fertigung, in der Menschen, Maschinen, Flurförderzeuge und Lagersysteme in ein einheitliches sicheres Intralogistiksystem eingebunden sind, ist bereits heute machbar – Trumpf bietet diese Lösung unter dem Begriff „Smart Material Flow“ seinen Kunden an. Mit an Bord ist Sensorexperte Leuze: Dessen Sensoren unterstützen mit Anwesenheitserkennung, Datenerfassung und Sicherheit.
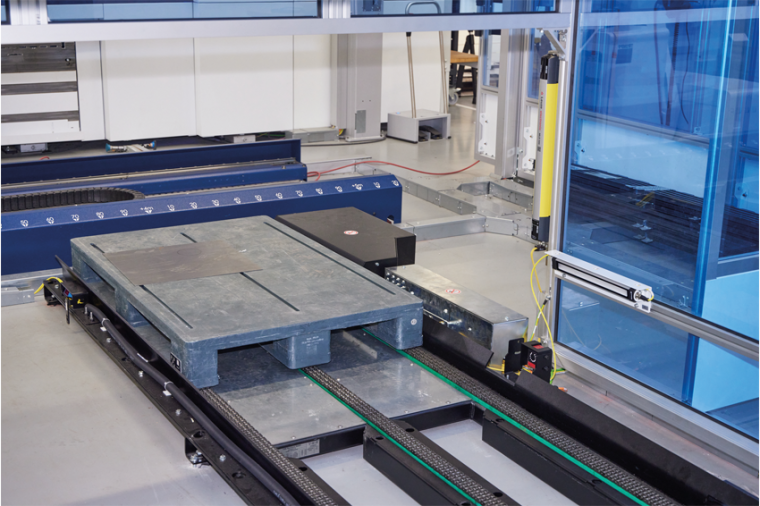
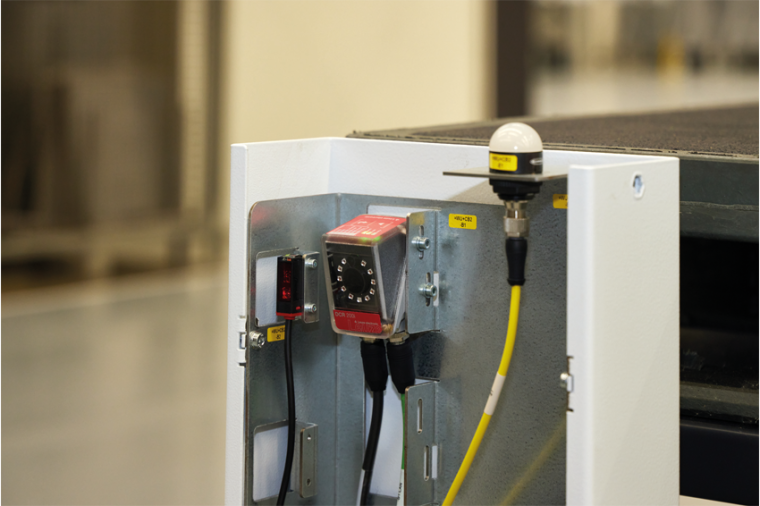
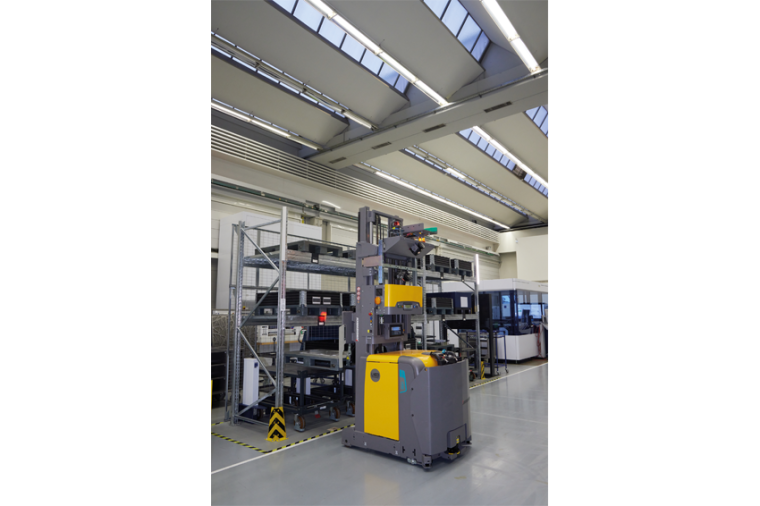
Mit einem Umsatz von rund 5,4 Milliarden Euro im Geschäftsjahr 2022/23 bietet Trumpf seinen Kunden Fertigungslösungen in den Bereichen Werkzeugmaschinen und Lasertechnik. Rund 17.900 Mitarbeitende sind an mehr als 70 Standorten für das Unternehmen mit Sitz in Ditzingen weltweit tätig.
Das Unternehmen unterstützt seine Kunden nicht nur mit einzelnen Maschinen, sondern hebt auf Wunsch die komplette Intralogistik von produzierenden Betrieben auf eine neue Stufe. Und das macht sich für die Kunden von Trumpf bezahlt: Bis zu 40 Prozent der Ressourcen entfallen in einer herkömmlichen Fertigung auf nicht wertschöpfende Tätigkeiten – etwa Materialsuche, Transport von Blechteilen oder administrative Buchungstätigkeiten.
Besser geht’s per Smart Material Flow, weiß Manuel Schwestka. Der Produktmanager Software & Automation bei Trumpf ist Experte für intelligente Automatisierungslösungen: „Bei unserem Ansatz spielen sämtliche Maschinen, Abläufe, Schnittstellen und vor allem der Mensch eine Rolle. Wir bringen alles miteinander in Einklang.“ Grundlage ist ein digitales Abbild der Produktion inklusive aller Komponenten und Lagerorte. Darauf basierend lässt sich der gesamte Fertigungsprozess systematisch planen und steuern.
Wer sich einen Eindruck von dieser Art des smarten Materialflusses verschaffen will, besucht eines der weltweit 16 Trumpf Customer Center – wie am Stammsitz in Ditzingen. Seit 1987 bildet das Unternehmen dort anhand seines aktuellen Produktportfolios die gesamte Prozesskette Blech ab – von der einzelnen Werkzeugmaschine bis hin zur vollautomatischen Fertigungslösung. Kunden können sich Maschinen unterschiedlicher Technologien vorführen lassen. Auch Zeit- und Machbarkeitsstudien sowie die Musterteileproduktion gehören dort zu den Kernaufgaben des Teams.
Zielsicher in den „Bahnhof“
Die Prozesskette Blech besteht im Wesentlichen aus den Schritten Schneiden bzw. Stanzen, Biegen und Schweißen. Für jeden Schritt bietet Trumpf die passenden Geräte an. Als verbindendes Element aller Arbeitsplätze dienen wiederum Docking-Stationen: „Eine Docking-Station lässt sich am besten als ‚Materialbahnhof‘ für Arbeitsplätze und Werkzeugmaschinen beschreiben“, sagt Manuel Schwestka. „Sie ist damit der Ort, an dem sich im Zusammenspiel mit der Trumpf Software Oseon alle Materialbewegungen zwischen den Arbeitsplätzen automatisch erfassen und verbuchen lassen. Außerdem dient die Docking-Station auch als sicherer und definierter Übergabeort für fahrerlose Transportsysteme (FTS).“ Diese liefern Paletten mit oder ohne Material an die ihnen zugewiesenen Docking-Stationen.
Damit die Übergaben automatisiert und effizient ablaufen, braucht es geeignete Sensorlösungen. Bei der Konzeption stand daher Leuze als Sensorspezialist mit tiefgreifendes Applikations-Know-how der Intralogistik beratend zur Seite. Auf Basis der Kundenanforderungen wurden alle Docking-Stationen im Customer Center in Ditzingen entlang der Prozesskette Blech mit Sensoren ausgestattet.
Automatischer Nachschub
Die Abläufe an einer Docking-Station gestalten sich wie folgt: Ein FTS oder manuell bedienter Stapler bestückt eine Station mit einer leeren oder beladenen Palette. Die Palette befindet sich wiederum auf einem Rollwagen, den die Beschäftigten aus der Docking-Station beispielsweise an ihren Arbeitsplatz oder zur Werkzeugmaschine in der Nähe ziehen können. Auf diese Weise lassen sich Arbeitsplätze komfortabel mit erforderlichen Teilen beliefern. Die Mitarbeitenden müssen für Nachschub keine weiten Wege auf sich nehmen.
Ein großer Vorteil ist das digitale Abbild der Vorgänge: Jede Docking-Station registriert Materialbewegungen beim Ablegen oder Entnehmen einer Palette automatisch. Diese werden per OPC UA ins Transportleitsystem von Oseon eingespeist. Die Docking-Station ist damit sowohl Informationsquelle für ein- und ausgehende Materialbewegungen als auch kurzfristiger Lagerort in unmittelbarer Nähe verschiedener Arbeitsplätze.
Per Sensor alles erfasst
Für den sicheren Betrieb der Docking-Station sowie zur Übertragung von Daten ins System kommen Leuze Sensoren zum Einsatz. An einer Docking-Station sind dies in der Regel drei Stück: Ein Sensor HT5.1/4X ist unten an der Station installiert. Er erfasst die Anwesenheit eines Wagens. Ein weiterer Sensor dieses Typs befindet sich oben an der Docking-Station. Dessen Aufgabe ist es, die Anwesenheit von Paletten zu registrieren.
Ist eine Palette erkannt, startet der HT5.1/4X deren Identifikation über einen weiteren Sensor. Hierfür ist ein DCR202iC installiert: Der Scanner erfasst über den auf der Palette abgebildeten 2D-Code Auftrags- und Materialdaten und übergibt sie ans Transportleitsystem.
Auf Basis der Informationen aus den Docking-Stationen informiert die Software Oseon die Shopfloor-Mitarbeitenden, wann genau welcher Auftrag wo abgeholt, zwischengelagert oder zu einem bestimmten Arbeitsplatz gebracht werden soll. Das System orientiert sich dabei an vorhandenen Auftragsdaten aus dem Produktionsplan. Automatisiert erzeugt die Oseon daraus Transportvorgänge von A nach B und leitet diese an Beschäftigte oder FTS weiter.
Automatisiert und doch flexibel
Für die Intralogistik hat dieses Zusammenwirken zwischen Sensortechnik und Software große Vorteile, erklärt Mario Mörk, Gruppenleiter Software und Prozesslösungen bei Trumpf: „Durch die Sensorik der Docking-Stationen weiß man immer, ob am Materialbahnhof der nächsten Arbeitsstation noch Platz ist. Falls ja, wird über die Oseon Produktionsplanung das nächste sinnvolle Material an diesen Platz gebracht oder ein Transportauftrag erzeugt. Der Auftrag wird dann entweder an eine Person mit Tablet oder an ein FTS übergeben und nach einer dynamischen Reihenfolge abgearbeitet.“ Was zuerst erledigt wird und was danach, hängt beispielsweise von der Priorität der Kundenaufträge ab. Dank der Leuze Sensoren werden Paletten am Arbeitsplatz automatisch gebucht oder angemeldet – das spart Zeit.
Zugleich bleibt eine gewisse Flexibilität gewahrt, weil sich über das System bei Bedarf auch Mitarbeitende zwischenschalten lassen. Das kann beispielsweise erforderlich sein, wenn ein Unternehmen in mehreren, voneinander getrennten Hallen fertigt. Dann liefert das FTS etwa bis zur Hallengrenze und eine Person übernimmt den Weitertransport über die Außenfläche zwischen den Gebäuden.
Sensoren als Schlüssel zur Automation
„Die installierten Leuze Sensoren sind sozusagen das Rückgrat dieser intelligenten Intralogistiklösung“, sagt Jörg Beintner, Key Account Manager für Werkzeugmaschinen bei Leuze. Dabei spielt jeder Sensor seine Stärken aus. Der HT5.1/4X zur Anwesenheitserkennung von Wagen und Palette ist ein LED-Lichttaster mit Hintergrundausblendung. Die Tastweite lässt sich per Spindel intuitiv einstellen.
Leuze bietet darüber hinaus weitere Varianten des Sensors an, maßgeschneidert auf die Anforderung und Applikation des Kunden. So ist der Lichttaster mit Hintergrundausblendung beispielsweise auch mit Laser erhältlich oder als Sensorversion, um besonders kleine Objekte zu erkennen. Taster mit extra großen oder kleinen Lichtflecken oder optimiert für hochglänzende und polierte Oberflächen stehen ebenfalls zur Wahl.
„Als zweite wichtige Komponente für die Intralogistiklösung von Trumpf haben wir auf unseren stationären 2D-Codeleser DCR 202iC gesetzt“, erläutert Beintner. Der Sensor erfasst 1D- und 2D-Codes äußerst zuverlässig. Im Customer Center hat Trumpf die 2D-Codes auf zwei Seiten jeder Palette abgebildet – diagonal gegenübergesetzt. Dadurch spielt es keine Rolle, mit welcher Seite voran die Palette in die Docking-Station geschoben wird. Der Code lässt sich so stets über nur einen Sensor erfassen. Der DCR 202iC liest Codes je nach Typ gedruckt oder direkt markiert, auch omnidirektional. Die Sensor People von Leuze bieten verschiedene Ausführungen hinsichtlich Größe, Schutzklassen IP 67 oder 69K, Schnelligkeit und Schnittstellen an. Übrigens ist es bei Trumpf in Ditzingen mit Leuze Sensoren zur Detektion nicht getan: Des Weiteren sind an den Materialschleusen zu Blechbearbeitungsmaschinen noch Sicherheits-Lichtvorhänge im Einsatz. Sie verhindern zuverlässig den Zutritt von Personen. Leuze hat hier ebenfalls bei Konzeption und Umsetzung umfassend unterstützt. Und weitere gemeinsame Projekte sind bereits in Planung.
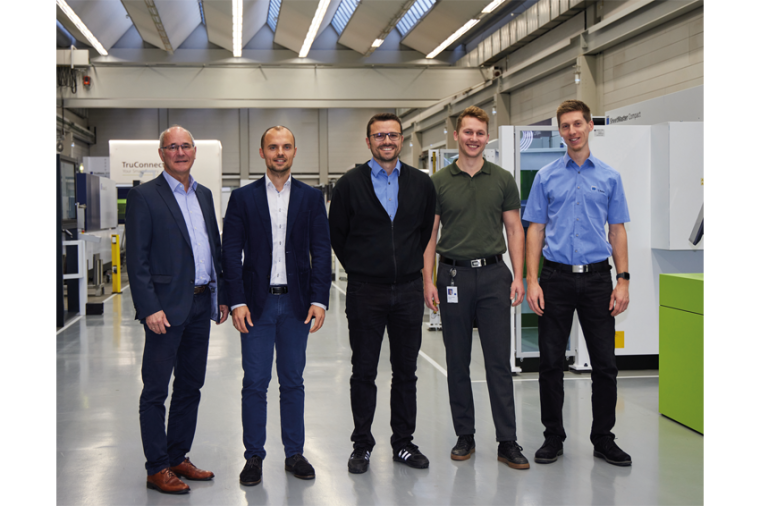
Meist gelesen
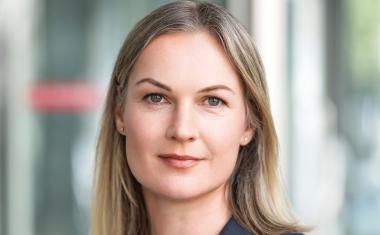
VIP-Interview: Dr. Alexandra Forster, Konzernsicherheit Bayer
GIT SICHERHEIT im Interview mit Dr. Alexandra Forster, Leiterin Konzernsicherheit bei der Bayer AG.
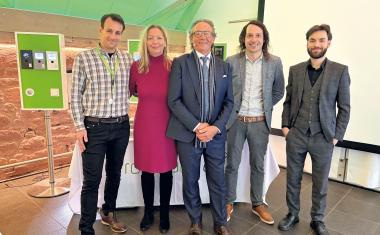
Frogblue International Partner Conference 2025: Innovationen und Zukunftsvisionen
Die Veranstaltung bot eine Plattform für den Austausch von Innovationen, Strategien und Zukunftsvisionen im Bereich der Gebäudeautomation und Zutrittskontrolle bis hin zu Einblicken in Kameratechnik.
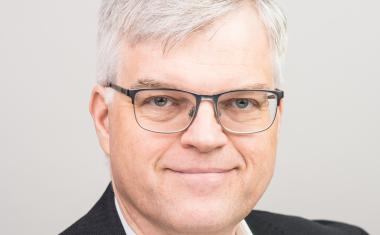
Maschinensicherheit im Kontext von KI und Security – Cyber Resilience Act: Neue Anforderungen für Maschinenbauer
Cyber Resilience Act & Maschinenverordnung: Neue Sicherheitsanforderungen für Maschinenbauer in vernetzten Industrieanlagen
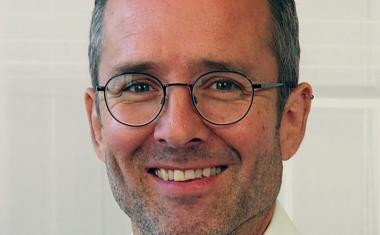
Zur aktualisierten Version der ISO 13855 zur Anordnung von Schutzeinrichtungen an Maschinen
ISO 13855 neu gedacht: Sicherheitsabstände für Maschinen präzise und zukunftssicher berechnen – jetzt informieren!
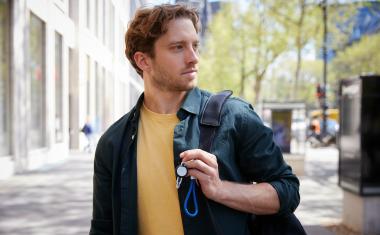
eCLIQ: Die elektronische Schließlösung für alle Fälle
Das eCLIQ-System vereint mechanische Sicherheit mit digitaler Flexibilität. Mit über 60 Zylindertypen und verschiedenen Schlüsseln, bietet es vielseitige Einsatzmöglichkeiten.