Sicherheit in der Mensch-Roboter-Kooperation
Rückt der Roboter dem Menschen in der Produktion in dem Sinne näher, dass keine klassische Schutzeinrichtung die beiden trennt, spricht man von kollaborativen Robotern. Mit dieser ...
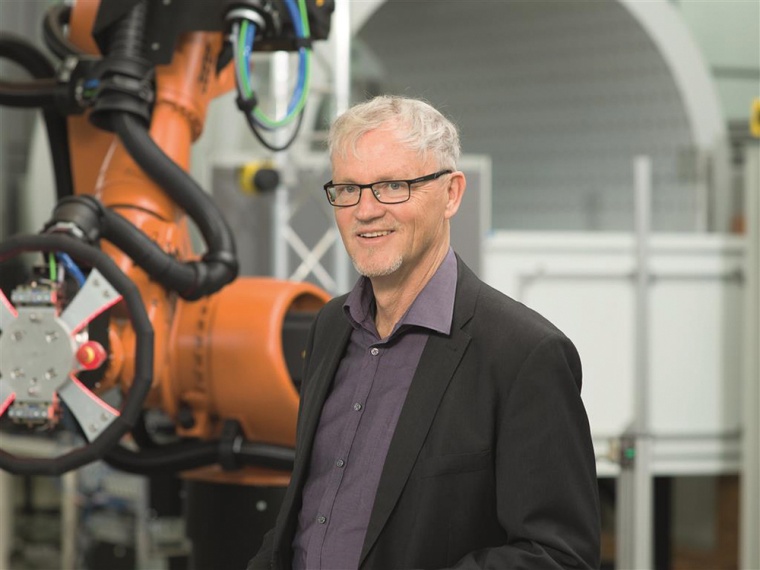
Rückt der Roboter dem Menschen in der Produktion in dem Sinne näher, dass keine klassische Schutzeinrichtung die beiden trennt, spricht man von kollaborativen Robotern. Mit dieser Art der Zusammenarbeit lassen sich Arbeitsplätze automatisieren, die häufig wiederkehrende monotone Tätigkeiten beinhalten, gleichzeitig aber menschliches Eingreifen erfordern. Über die Sicherheit solcher Systeme im Vergleich zur klassischen Robotik befragte Matthias Erler von GIT SICHERHEIT Dr. Matthias Umbreit, Robotik-Experte bei der Berufsgenossenschaft Holz und Metall.
GIT SICHERHEIT: Herr Dr. Umbreit, als Berufsgenossenschaft Holz und Metall geht es Ihnen um die Gesundheit der Mitarbeiter in den Betrieben – deshalb steht bei der Mensch-Roboter-Kooperation für Sie im Vordergrund, dass sie Tätigkeiten übernehmen können, die für den Menschen nicht ergonomisch wären. Glauben Sie, dass wir wegen dieser Entlastung eher noch mehr Robotik brauchen? Viele Roboter werden ja aus anderen Gründen eingesetzt?
Matthias Umbreit: Natürlich steht beim Einsatz von Automation in den meisten Fällen die Kostenfrage im Vordergrund. Es ist auch nachvollziehbar, dass in Europa in der Regel durch mehr Automation die Industrieproduktion dauerhaft gehalten werden kann. Die Vermeidung von Arbeitsunfällen, Berufskrankheiten und arbeitsbedingten Gesundheitsgefahren sollte dabei ebenfalls ein Ziel sein. Das gilt zum Beispiel für die Überkopfarbeit, das Arbeiten in gebückter Haltung oder das Heben von Teilen in rückenergonomisch ungünstiger Position. Daraus resultierende Erkrankungen gilt es für die betroffenen Personen zu vermeiden. Gleichzeitig verursachen Unfälle oder Erkrankungen vermeidbare Kosten. Wenn es gelingt, diese Erkrankungen zu vermeiden, können Roboter Teil einer Lösung sein.
Roboter sind ja ein bisschen wie Indianer – sie kennen keinen Schmerz. Allerdings können sie Menschen ganz schön wehtun und merken es dabei noch nicht mal.
Matthias Umbreit: Da muss ich ein klein wenig korrigieren: Die neue Robotergeneration, sogenannte Leichtbauroboter, kennen auch eine Art Schmerz. Beim Kontakt eines solchen Roboters oder des Roboterwerkzeugs mit einem Hindernis kann z. B. durch in den Robotergelenken eingebaute Drehmomentsensoren die einwirkende Kraft erkannt werden. Ab einer bestimmten Kraftschwelle schaltet sich der Roboter ab. Sollte es sich bei dem besagten Hindernis um einen Menschen handeln, können so Verletzungen verhindert werden. Die Grundlagen dazu – die sogenannten biomechanischen Grenzwerte – wurden in von der Berufsgenossenschaft Holz und Metall und der Deutschen Gesetzlichen Unfallversicherung beauftragten Forschungsarbeiten entwickelt. Die internationale Normenorganisation ISO hat die Grenzwerte in ihr Normenwerk übernommen.
Und wie sieht es mit den Unfallzahlen aus?
Matthias Umbreit: Nach den Erhebungen der Deutschen Gesetzlichen Unfallversicherung ereigneten sich im Jahr 2015 bundesweit 183 meldepflichtige Arbeitsunfälle an Robotern. Rechnet man noch roboterähnliche Anlagen, wie z. B. sog. Transferanlagen und automatische Montagesysteme hinzu, ergibt das für 2015 eine Gesamtzahl von 304 meldepflichtigen Arbeitsunfällen. Im Vergleich zu den Unfallzahlen an anderen Maschinen handelt es sich um sehr geringe Werte. Beispielsweise ereigneten sich im Bereich der gewerblichen Wirtschaft und der öffentlichen Hand 1.045.237 meldepflichtige Arbeitsunfälle, davon 43.074 an Maschinen.
Wie viele Unfälle fallen dabei im engeren Sinne auf kollaborierende Roboter?
Matthias Umbreit: Die genannten Daten liefern derzeit keine Anhaltspunkte zu möglichen Unfällen mit kollaborierenden Robotern. Dies liegt aber auch sicher an der derzeit noch geringen Zahl dieser Anlagen im tatsächlichen Industrieeinsatz. Genaue Zahlen gibt es hierzu nicht. Von den knapp 200.000 klassischen Industrierobotern in Deutschland (nach Angaben des Statistik-Jahrbuchs „World Robotics“ der International Federation of Robotics c/o VDMA) dürften nach meiner persönlichen Schätzung einige Hundert kollaborierende Roboter sein.
Kann man ungefähr einschätzen, wie viele dieser Vorfälle durch bessere Sicherheitsmaßnahmen im Zusammenhang mit der Mensch-Roboter-Kooperation vermeidbar gewesen wären?
Matthias Umbreit: Hierbei kommt dem Anlass zur Manipulation von Schutzeinrichtungen (z. B. Schutzzäune, Schutztüren, Lichtschranken) besondere Bedeutung zu. Eine im Jahr 2009 von der Deutschen Gesetzlichen Unfallversicherung durchgeführte Untersuchung ergab, dass bis zu 30 % der Schutzeinrichtungen an Maschinen in Deutschland zweitweise oder dauerhaft außer Kraft gesetzt werden. Auch Roboteranlagen sind davon betroffen. Einer der Hauptründe zur Manipulation ist ein notwendiger Eingriff des Maschinenbedieners bei Störungen. Hier bietet die Mensch-Roboter-Kollaboration (MRK) einen entscheidenden Vorteil: Wo kein Schutzzaun vorhanden ist, kann auch keiner manipuliert werden. Allerdings kann die MRK aufgrund der Randbedingungen nicht überall eingesetzt werden. Dennoch: Bei einer fachgerechten Anwendung kann die MRK dabei helfen, Manipulationen zu vermeiden.
Die Wirtschaftlichkeit von Maßnahmen kann auch hier nicht außer Acht gelassen werden. Wie sehen Sie hier die Praxis?
Matthias Umbreit: Die Sicherheitsanforderungen für MRK-Anlagen sind z. B. bei der steuerungstechnischen Sicherheit ebenso hoch, wie für andere Roboteranlagen. Ein pauschales „Kostenproblem“ aufgrund technischer Anforderungen dürfte es daher nicht geben. Natürlich gibt es bei MRK-Anlagen z. B. speziell entwickelte, neuartige Schutzsysteme. Die Kosten für diese Systeme stellen jedoch nach meiner Erfahrung kein Problem dar, wenn die Hersteller die Sicherheitsanforderungen von Anfang an berücksichtigen. Werden die Anforderungen nicht oder nur unzureichend bei der Produktentwicklung berücksichtigt, kann es durchaus zu Problemen kommen. Dann müssen z. B. Hardware- und Software im Nachhinein mit meist sehr hohem Aufwand geändert oder gar neu entwickelt werden. Dies führt in der Regel zu hohen Kosten.
Können die konsequente Beachtung und die Verstärkung von Sicherheitsmaßnahmen die Robotik so verteuern, dass die Ausbreitung der Mensch-Roboter-Kooperation gehemmt wird?
Matthias Umbreit: Ich betone nochmals, dass die Sicherheitsmaßnahmen in den technischen Standards nicht erhöht wurden. Es sind jedoch neue Funktionen hinzugekommen, z. B. die Kraftüberwachung. Es dürfte aber nachvollziehbar sein, dass solche Sicherheitsfunktionen mindestens den gleichen Schutzlevel haben, wie beispielsweise ein Not-Halt-Taster oder ein Lichtvorhang. Ein konsequentes Beachten der Sicherheitsmaßnahmen ist folglich kein großes Hemmnis für die Ausbreitung von MRK-Anlagen. Hierbei spielen andere Faktoren, wie z. B. Anschaffungskosten vs. Einsatzmöglichkeiten, eine Rolle. In vielen Fällen sind MRK-Anlagen teurer als eine klassisch abgesicherte Roboterzelle. Zusätzlich können MRK nicht überall eingesetzt werden. Sie sind bei Geschwindigkeit, Traglast, Teilegeometrie etc. eingeschränkt. Klassische Anlagen bieten hier in der Regel höhere Prozesssicherheit und arbeiten schneller. Die MRK sollte also nur dort eingesetzt werden, wo es dem Anwender tatsächlich nützt. Grundlegend hinkt der direkte Vergleich von MRK-Anlagen mit klassischer Robotik. Es ist eben nicht, wie – im übertragenen Sinne - ein Vergleich von zwei Obstsorten, wie z. B. Äpfel und Birnen. Es ähnelt eher einem Obst-Gemüse-Vergleich bzw. dem Versuch, Äpfel durch Kartoffeln ersetzen zu wollen.
Sind die unter Industrie 4.0 verschlagworteten Entwicklungen von Einfluss in diesem Zusammenhang?
Matthias Umbreit: Die von der Bundesregierung koordinierte „Plattform Industrie 4.0“ treibt ohne Zweifel auch die kollaborative Robotik an. Bei der Industrie 4.0 geht es streng genommen um die Verzahnung der industriellen Produktion mit modernster Informations- und Kommunikationstechnik. Das betrifft primär die gesamte Automation und eben nicht „nur“ die kollaborative Robotik. Das belegt auch der internationale Vergleich. In Japan wird z. B. eine ähnliche Initiative als „Robotic Revolution“ bezeichnet. Die Technologien der klassischen und kollaborativen Robotik werden sich weiterentwickeln. Dabei stehen insbesondere einfache Programmierstrategien im Fokus, die intuitiv ohne das Erlernen einer Programmiersprache angewendet werden können. Gleiches gilt für Programmiergeräte, die ähnlich wie Smartphones oder Tablets gestaltet sind und klassische Programmierhandgeräte ersetzen. Auch hier gilt aber: Sicherheitsfunktionen wie z. B. ein Zustimmungsschalter oder Not-Halt-Taster müssen den Anforderungen entsprechen.
Nun gibt es ja verschiedene Ansätze zur Gewährleistung dieser Sicherheit – worin bestehen diese genau?
Matthias Umbreit: Die kollaborative Robotik wird derzeit nach der internationalen Technischen Spezifikation ISO TS 15066 in vier unterschiedliche Kollaborationsarten unterteilt: Die Handführung, den sicherheitsgerichteten Stopp, die Geschwindigkeits- und Abstandsüberwachung sowie die sogenannte Leistungs- und Kraftbegrenzung. Wobei die ersten drei Arten überwiegend mittels klassischer Industrieroboter realisiert werden, unter Zuhilfenahme zusätzlicher spezieller Schutzeinrichtungen kommt die letztere sogenannte Leistungs- und Kraftbegrenzung ohne Lichtschranken, Schutzzäune, Trittmatten und dergleichen aus. Diese derzeit vielbeachtete Technologie beruht in der Regel auf speziell für diesen Zweck konstruierte Roboter. Diese Roboter, meistens auch als Leichtbauroboter bezeichnet, haben die Eigenschaft, einen Kontakt mit einem Hindernis, z. B. einer Person durch zusätzliche Sensoren zu erkennen und noch vor Eintreten einer Verletzung die Roboterbewegung zu stoppen.
Eine wichtige Größe ist hier z. B. der sogenannte biomechanische Grenzwert.... Könnten Sie das etwas näher erläutern?
Matthias Umbreit: Ein Maß, welches den zulässigen Kontakt zwischen Mensch und Roboter genauer beschreibt, ist in der Tat der biomechanische Grenzwert. Dabei geht es um die unter Sicherheits- und Gesundheitsaspekten zulässige mechanische Einwirkung von Teilen des Roboters, des Roboterwerkzeugs oder des Bauteils bei einem Kontakt mit dem Menschen. Denn auch wenn der Roboter bei einem Kontakt sofort stoppt, muss geklärt sein, wie „heftig“ dieser Kontakt sein darf, ohne die Gesundheit eines Beschäftigten zu beeinträchtigen. In den von der Berufsgenossenschaft Holz und Metall in Kooperation mit Forschungspartnern durchgeführten Untersuchungen zeigte sich, dass dabei grundsätzlich zwei Größen zu berücksichtigen sind: Die einwirkende Kraft für großflächige Kontaktierungen z. B. an den Roboterarmen, und der Druck für kantige Kontaktierungen z. B. am Roboterwerkzeug oder am Bauteil. Letztere ist in der Praxis meist die ausschlaggebende Größe, weil sich kantige Oberflächen nicht komplett vermeiden lassen. Im Auftrag der Berufsgenossenschaft Holz und Metall wurden Untersuchungen mit über 100 Probanden in mehr als 10.000 Einzelmessungen an unterschiedlichen Körperregionen durchgeführt. Apparative Ausrüstungen wurden vom Institut für Arbeitsschutz der DGUV (IFA) bereitgestellt. Die Untersuchungsergebnisse wurden in das Schriftenwerk der DGUV aufgenommen und in die technische Spezifikation ISO TS 15066 aufgenommen.
Sicherheit ist andererseits keine abstrakte Größe, sondern stellt sich in jedem Betrieb anders dar. Wie verteilt sich denn die Verantwortung für die Sicherheit im Dreieck Hersteller, Unternehmer und Mitarbeiter?
Matthias Umbreit: In diesem Zusammenhang werden in der Praxis oft Sonderlösungen erwartet. Hier muss ich Sie aber leider enttäuschen. Auch eine MRK-Anlage ist nach der EG-Maschinenrichtlinie zunächst eine Maschine wie jede andere. Das heißt, von der Risikobeurteilung des Herstellers über die technische Dokumentation bis hin zum CE-Zeichen obliegen dem Anlagenhersteller die in der EU und Deutschland üblichen Verpflichtungen. Das gleiche gilt für die Anlagenbetreiber. Für Arbeitgeber in Deutschland gilt das Arbeitsschutzgesetz und speziell u.a. die Betriebssicherheitsverordnung. Im Detail ergeben sich bei MRK-Anlagen jedoch schon ein paar Besonderheiten. So muss z. B. der Hersteller einer solchen Anlage auch an Gefahren denken, die bei klassischen Anlagen unbekannt waren. Also, dass beispielsweise ein Arbeiter in einer misslichen Lage zwar nicht verletzt, aber durch die plötzliche Sicherheitsabschaltung in der Bewegung eingeschränkt sein kann. Dafür müssen technische Maßnahmen zum „Befreien“ bereitgestellt werden – etwa ein immer erreichbarer Bedienknopf zum Lösen der mechanischen Bremsen. Ebenso kommen auch auf den MRK-Anlagenbetreiber neue Aufgaben beim Benutzen zu. Bei einer Neuprogrammierung aufgrund eines neuen Teileprogramms ändern sich auch die biomechanischen Grenzwerte. Dann ist in der Regel eine Neumessung erforderlich. Gleiches gilt für entsprechende, gem. Arbeitsschutzgesetz vom Arbeitgeber sicherzustellende Unterweisungen der Beschäftigten, wie auch für Schulungen.
Wo sehen Sie jeweils noch den größten Handlungs- oder Veränderungsbedarf?
Matthias Umbreit: Die letzte Messe Automatica in München hat schon eindrucksvoll gezeigt, dass das Thema MRK nun auch bei den Komponentenherstellern angekommen ist. In den Messehallen waren ansehnliche Funktionsmuster von Greifersystemen für die kollaborative Robotik zu sehen. Hierin sehe ich eine der wichtigsten Voraussetzungen, damit kollaborative Robotersysteme verstärkt Einzug in den praktischen Alltag halten können. Die Technologie der Greifersysteme muss bis hin zu zertifizierten Systemen weiterentwickelt werden, die von den Anwendern baukastenartig eingesetzt werden können. Ein weiterer, noch zu entwickelnder Baustein ist die Verifikation von sicheren Anlagen. Die Berufsgenossenschaft Holz und Metall hat mit der Deutschen Gesetzlichen Unfallversicherung und dem Institut für Arbeitsschutz der DGUV (IFA) durch Forschung und maßgebliche Beteiligung an der Normung wichtige Grundlagen hierfür geschaffen. Außerdem wurden durch die Berufsgenossenschaft Holz und Metall ersten Anlagen zertifiziert. Nun, da die Zahl der Anlagen zunimmt, reicht die Kapazität der Berufsgenossenschaft für die Zertifizierung jeder einzelnen Anlage nicht mehr aus. Eine Zertifizierung ist auch keine gesetzliche Pflicht. Hier sind nun qualifizierte Dienstleister gefragt zur Beratung und insbesondere zur Messung der biomechanischen Grenzwerte bis hin zur Dokumentation und Unterstützung bei der EG-Konformitätsbewertung.
Immerhin gibt es Normen, wie die EN ISO 10218-1 und -2?
Matthias Umbreit: Die Normen EN ISO 10218-1 und EN ISO 10218-2 sind europäisch harmonisiert und im Amtsblatt der EU gelistet. Das heißt, sie besitzen in der Praxis einen hohen Stellenwert. Werden diese Normen angewendet, wird automatisch von der Erfüllung der EG-Maschinenrichtlinie ausgegangen. Diese Normen enthalten hinsichtlich kollaborativer Robotik jedoch nur grundlegenden Anforderungen wie z. B. die Steuerungssicherheit nach Kategorie 3, PLd. Darüber hinaus gehende Anforderungen z. B. nach biomechanischen Grenzwerten sind in der sogenannten Technischen Spezifikation ISO TS 15066 enthalten. Dieses Dokument hat nicht den Status einer harmonisierten Norm. Es ist dafür bestimmt für einen Übergangszeitraum von ca. 3-4 Jahren die Anforderungen, die dem durch die Forschung gewonnenen wissenschaftlichen Kenntnisstand als Stand der Technik entsprechen, im Normungsumfeld darzustellen und anschließend bei Überarbeitung von EN ISO 10218-1 und EN ISO 10218-2 in diese zu übernehmen. Nichts desto trotz gilt ISO TS 15066 als Regel der Technik und kann in der Praxis angewendet werden, zumal vergleichbare Normen nicht oder nur unzureichend vorhanden sind.
Sie sind ja an der Entwicklung von Normen selbst beteiligt als Berufsgenossenschaft bzw. DGUV – wie sieht das genau aus?
Matthias Umbreit: Innerhalb der DGUV wurde schon vor vielen Jahren eine Arbeitsteilung vereinbart. Sie erlaubt es, dass übergreifende Fachaufgaben nicht durch jede Berufsgenossenschaft separat gelöst werden. Nach dem Prinzip „Einer für alle“ wurden jenen Berufsgenossenschaften mit den am stärksten vorhanden Aufkommen die entsprechenden Aufgaben im Rahmen von sogenannten Fachbereichen der DGUV übertragen. So sind z. B. bei der Berufsgenossenschaft Holz und Metall die Themenfelder Robotik und Werkzeugmaschinen angesiedelt, während es bei anderen Berufsgenossenschaften z. B. die Verpackungstechnologien oder der Brandschutz sind. Ein Vertreter der gesetzlichen Unfallversicherung für ein entsprechendes Normungsgremium wird nach der gleichen Systematik bestimmt. Diese Person vertritt dann die DGUV bzw. die gesetzlichen Unfallversicherungsträger im jeweiligen Normungsausschuss. Themen sind dann die Arbeitssicherheit und der Gesundheitsschutz z. B. bei im jeweiligen Normungsgremium behandelten Maschinen von der Herstellung bis zum Betrieb.
Sie sehen sogar in der demografischen Entwicklung einen Anlass, sich stärker mit der Mensch-Roboter-Kollaboration zu beschäftigen?
Matthias Umbreit: Die demographische Entwicklung ist in Deutschland wie in anderen Industrienationen ein Thema von hoher Relevanz. Die Technik wird dabei immer wieder als mögliches Mittel zur Kompensation ins Spiel gebracht. Aus meiner Sicht ist generell die Automation ein Mittel, um den drohenden Fachkräfterückgang teilweise aufzufangen. Klassische Roboteranlagen stehen dabei mehr im Fokus als kollaborative. Geht es aber darum, z. B. ältere Arbeitnehmer länger im Betrieb zu halten, könnte die MRK sicherlich eine erwägenswerte Maßnahme sein. So werden bereits heute Anlagen realisiert, die beispielsweise den Anteil der Überkopfarbeit an einem Montagearbeitsplatz übernehmen. Auch häufiges Bücken, um eine Verschraubung zu setzen oder ein Teil aus einem Behälter aufzunehmen, kann an einem weiterhin manuellen Arbeitsplatz anteilig durch einen kollaborativen Roboter übernommen werden. So können ältere Arbeitnehmer oder Arbeitnehmer mit Einschränkungen an diesen Arbeitsplätzen eingesetzt werden.