David Korte über das Thema Losgröße 1 und die Sensorik der Zukunft
Bereits im Oktober 2018 hörten Besucher des Fachforums Sicherheit + Automation auf der Motek einiges über die Trends der Automatisierungsbranche. Einer der Referenten war David Kor...

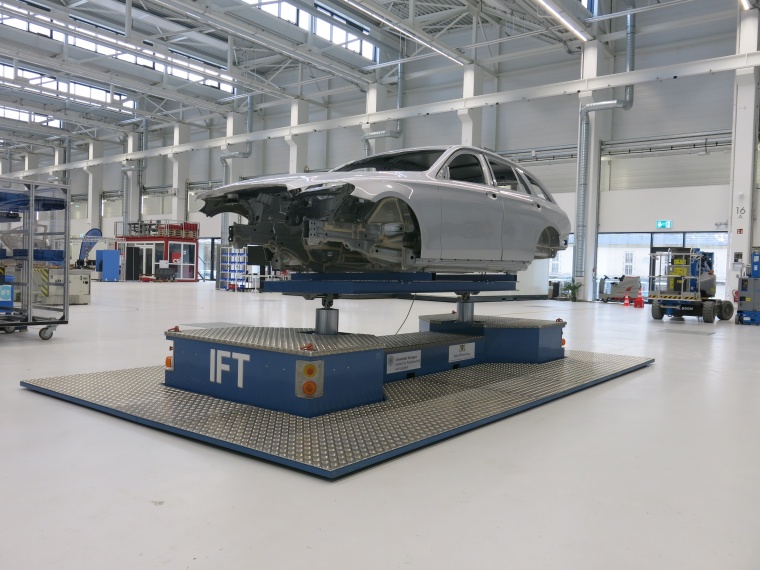
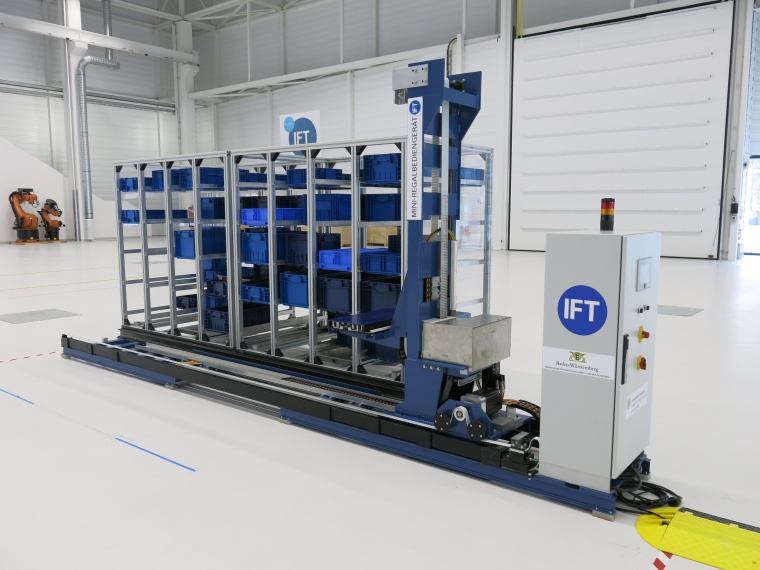
Bereits im Oktober 2018 hörten Besucher des Fachforums Sicherheit + Automation auf der Motek einiges über die Trends der Automatisierungsbranche. Einer der Referenten war David Korte, Dipl.-Ing., Akademischer Mitarbeiter an der Universität Stuttgart am Institut für Fördertechnik und Logistik, der mit seinem Vortrag „Die sichere Kollaboration in der Automobilproduktion der Zukunft“ GIT SICHERHEIT besonders auffiel. Jetzt hat Lisa Schneiderheinze, Redakteurin bei GIT SICHERHEIT, ihn zum Interview gebeten, um ihn zu seinen Forschungsprojekten, den aktuellen Herausforderungen in der Automobilproduktion und seiner Vision 2036 zu befragen.
GIT SICHERHEIT: Herr Korte, Sie haben in Ihrem Vortrag den Forschungscampus „Arena 2036“ erwähnt. Können Sie unseren Lesern kurz schildern, worum es sich dabei handelt und welche Themen dort erforscht werden?
David Korte: Die Arena 2036 ist ein Forschungscampus, der an der Universität Stuttgart beheimatet ist. Der Name steht für Active Research Environment for the Next Generation of Automobiles, also grob übersetzt für eine aktive Forschungsumgebung für das Automobil der Zukunft. Die Zahl 2036 steht dabei für das 150-jährige Jubiläum des Automobils im Jahr 2036. Doch die Arena 2036 ist noch mehr: Neben der Mobilität der Zukunft wird dort auch an der Arbeit und der Produktion der Zukunft geforscht. Außer verschiedenen Instituten der Universität Stuttgart beteiligen sich an der Forschung unter anderem Institute der Fraunhofer-Gesellschaft oder des Deutschen Zentrums für Luft- und Raumfahrt sowie zahlreiche Industriepartner wie Daimler, Bosch, Kuka, Trumpf oder auch Pilz. Seit der Gründung hat sich die Anzahl der Mitglieder in der Arena 2036 mehr als vervierfacht. Um auch den notwendigen Platz für die verschiedenen Forschungsaktivitäten zu haben, wurde eigens dafür für rund 30 Millionen Euro eine Forschungsfabrik mit 10.000 m² Bruttogeschossfläche errichtet. Mit meinen Kollegen vom Institut für Fördertechnik und Logistik der Universität Stuttgart arbeiten wir vor allem an der passenden Logistik für die Produktion der Zukunft. Dies beinhaltet neben völlig neuen Konzepten des Materialflusses auch die dafür erforderlichen Komponenten.
Wie kommt es, dass der Trend vom Massenprodukt hin zum Einzelstück geht und ist Losgröße 1 schon bei uns in Deutschland angekommen?
David Korte: Angefangen hat es auf dem Fließband mit dem Modell T vor über 100 Jahren. Damals waren die Fahrzeuge weitestgehend identisch. Heutzutage haben der gesellschaftliche Stellenwert, die spezifischen Einsatzzwecke und die individuellen Ansprüche zu einem breit gefächerten Produktportfolio im Automobilbereich geführt. Die Kunden können neben unterschiedlichen Kombinationsmöglichkeiten bei den klassischen Verbrennungsmotoren und den jeweiligen Getrieben sowie weiteren Antriebsvarianten, wie Gas, Elektro, Wasserstoff oder Hybrid auch die Ausstattung der Fahrzeuge völlig individuell wählen. So ist vor allem im Bereich der Oberklasse-Fahrzeuge die Losgröße 1 bereits erreicht.
Vor welchen Herausforderungen stehen Montage und Logistik in Bezug auf variantenreichere Produkte?
David Korte: Die variantenreiche Serienfertigung stellt die Automobilindustrie vor zahlreiche Herausforderungen, da das Fließbandprinzip und die einschlägigen Logistikprozesse trotz Automatisierung im Kontext von Losgröße 1 nicht mehr effizient genug sind. Früher wurden häufig Großladungsträger und Gitterboxen für die Materialbereitstellung verwendet. Grund dafür waren die vielen Gleichteile. Heute hingegen werden Durchlaufregale oder vorkommissionierte Warenkörbe verwendet. Bereitgestellt werden die für die Produktion benötigten Materialien in der Regel Just-In-Sequence. Dies führt allerdings auch dazu, dass die Produktionsreihenfolge sehr stark vorgegeben ist. Auf kurzfristige Änderungen oder bei fehlerhaften Produkten kann dann nicht mehr reagiert werden.
An welchen Konzepten arbeiten Sie gerade in Bezug auf sichere Mensch-Roboter-Kollaboration?
David Korte: In Bezug auf die Mensch-Roboter-Kollaboration arbeiten wir momentan in zwei Bereichen. Zum einen möchten wir neue Bedienkonzepte für die Kollaboration zwischen dem Menschen und beispielsweise fahrerlosen Transportfahrzeugen entwickeln. Die bald erscheinende neue FTS-Norm wird zukünftig auch das Mitfahren von Personen auf fahrerlosen Transportfahrzeugen ermöglichen. Dazu muss aber sicher erkannt werden, ob und wo sich Personen auf dem Fahrzeug befinden. Wir wollen aber nicht nur sicher erkennen, ob sich Personen auf dem Fahrzeug befinden, sondern sie auch in der Umgebung der Fahrzeuge erkennen. Dazu haben wir im Dezember vergangenen Jahres ein vom Bundesministerium für Bildung und Forschung finanziertes Forschungsprojekt gestartet, in dem wir mit unseren Partnern eine 3D-Umgebungssensorik entwickeln möchten, die eine sichere Unterscheidung von Personen und Objekten ermöglichen soll. Dadurch wären wir in der Lage, das Verhalten von fahrerlosen Transportfahrzeugen oder auch Robotern an die Anwesenheit von Personen anzupassen. Am Projekt S³, was für Sicherheitssensorik für Serviceroboter und weitere Anwendungen steht, beteiligen sich unter anderem das Fraunhofer-Institut für Produktionstechnik und Automatisierung sowie die Firma Pilz.
Welche Herausforderungen ergeben sich bei diesen Konzepten in der sicheren Kollaboration?
David Korte: Dadurch, dass wir beispielsweise zukünftig die Möglichkeit haben, Personen direkt in die Montageprozesse auf einem FTF einzubeziehen, ergeben sich völlig neue Herausforderungen. So muss das gefahrlose Aufsteigen auf das FTF ermöglicht werden, das Verhalten des Fahrzeuges muss sich dann an die Personen hinsichtlich Beschleunigung und Verzögerung anpassen und es bedarf neuer Bedienkonzepte, die eine Steuerung des FTF durch den Werker ermöglichen, auch wenn dieser beispielsweise gerade Werkzeuge oder Bauteile in den Händen hat.
Was wird sich in der Sensorik ändern? Sind aktuelle Sensoren für dieses Konzept ausreichend?
David Korte: Gerade bei fahrerlosen Transportfahrzeugen wird sich die Sensorik, die den sicheren Betrieb gewährleisten soll, ändern müssen. Bisher werden bei diesen Fahrzeugen überwiegend Laserscanner oder berührungsempfindliche Sensoren, manchmal auch Ultraschallsensoren, eingesetzt. Die Fähigkeiten dieser Sensoren sind jedoch beschränkt. So ermöglicht der klassische Laserscanner die Überwachung lediglich einer Ebene. In einem dynamischen Umfeld wird es zunehmend wichtiger, mehr als nur diese eine Ebene zu überwachen. Häufig wird dabei auf Sensoren aus dem Automobilbereich verwiesen. Dort werden verschiedene Kamerasysteme, Radarsensoren, Lidar-Sensoren alleine oder in Kombination miteinander eingesetzt und sollen so langfristig das Autonome Fahren ermöglichen. Warum also nicht einfach diese Sensoren industriell in fahrerlosen Transportfahrzeugen einsetzen? In unserem Forschungsprojekt S³ wollen wir auch dieser Frage nachgehen.
Wo stehen wir 2036 mit der Automobilproduktion bzw. was ist Ihre Vision 2036?
David Korte: Unsere Vision ist die sogenannte Production2Go. Dieses Konzept sieht vor, dass man in einer leeren Halle, dabei kann es sich auch um eine mobile Halle wie beispielsweise ein Festzelt handeln, mit mobilen Komponenten innerhalb kürzester Zeit eine Produktionsanlage ohne feste Infrastruktur aufbauen und betreiben kann. Erste Prototypen dieser mobilen und hochflexiblen Komponenten für den Materialfluss und die Montage wurden in der Arena 2036 bereits aufgebaut und werden dort weiterentwickelt. Zentrales Element ist dabei die sogenannte „Mobile Montageinsel“ die den Transport von zu montierenden Fahrzeugen und die gleichzeitige Montage daran ermöglicht. Die Materialbereitstellung kann mit Hilfe des „Mobilen Supermarktes“ erfolgen, bei dem mittels Mini-Regalbediengerät den Werkern genau das Material angereicht wird, das sie für die jeweiligen Montageschritte benötigen. Um ein effizientes Zusammenspiel dieser Komponenten zu ermöglichen, bedarf es unserer Ansicht nach auch neuer Steuerungsansätze, an denen unsere Kollegen derzeit forschen.
Business Partner
Institut für Fördertechnik und LogistikHolzgartenstrasse 15b
70174 Stuttgart
Deutschland
Meist gelesen
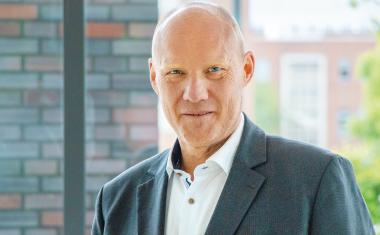
VIP-Interview: Andreas Maack, Chief Security Officer bei Volkswagen
GIT SICHERHEIT im Interview mit Andreas Maack, Leiter Konzern Sicherheit & Resilienz und Chief Security Officer der Volkswagen AG.
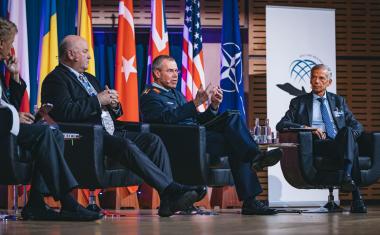
Euro Defence Expo und NATO JAPCC parallel zur Security Essen 2026
Vom 22. bis 25. September 2026 wird die Euro Defence Expo (Eudex) ihre Premiere in der Messe Essen begehen – gleichzeitig mit der jährlichen Konferenz des NATO Joint Air Power Competence Centre sowie der Security Essen.
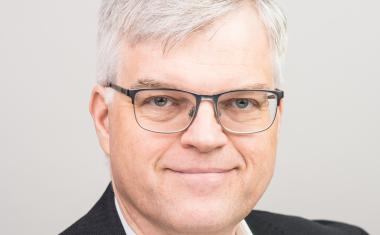
Maschinensicherheit im Kontext von KI und Security – Cyber Resilience Act: Neue Anforderungen für Maschinenbauer
Cyber Resilience Act & Maschinenverordnung: Neue Sicherheitsanforderungen für Maschinenbauer in vernetzten Industrieanlagen
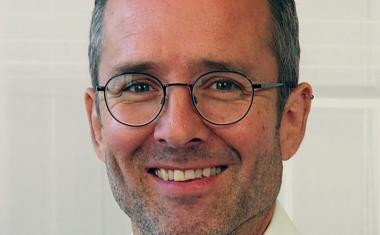
Zur aktualisierten Version der ISO 13855 zur Anordnung von Schutzeinrichtungen an Maschinen
ISO 13855 neu gedacht: Sicherheitsabstände für Maschinen präzise und zukunftssicher berechnen – jetzt informieren!
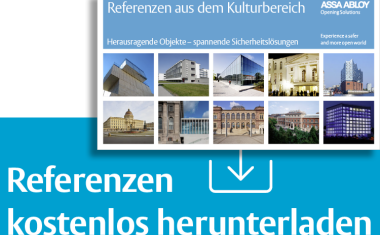
Zutritt steuern, Werte schützen – Schließtechnik für Kulturstätten
Öffentlich zugängliche Kulturinstitutionen sind mit unschätzbaren materiellen und immateriellen Werten ausgestattet.