Gasmesstechnik: Detektion brennbarer Gase mit Wärmetönungssensoren von Compur
Gasmesstechnik: Detektion brennbarer Gase mit Wärmetönungssensoren von Compur. Der Betreiber einer Produktionsanlage ist dafür verantwortlich, Mensch und Umwelt vor Gefahren zu sch...
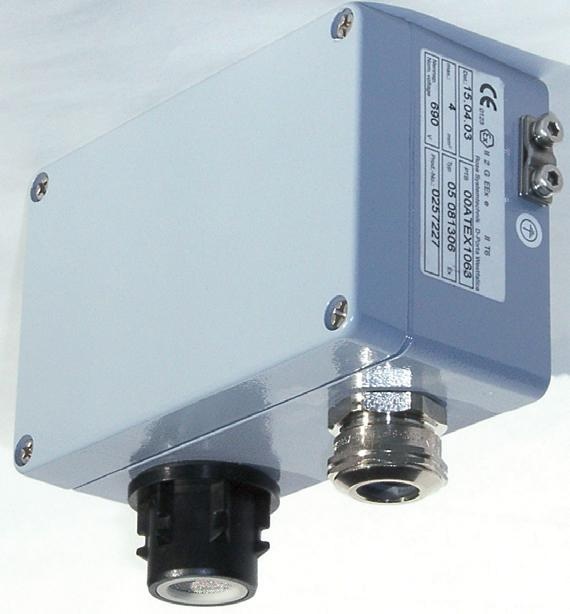
Gasmesstechnik: Detektion brennbarer Gase mit Wärmetönungssensoren von Compur. Der Betreiber einer Produktionsanlage ist dafür verantwortlich, Mensch und Umwelt vor Gefahren zu schützen. Er wird also stets bemüht sein, Gase dort zu halten wo sie hingehören: Im Prozess. Die Welt ist nicht perfekt, deshalb besteht immer die Gefahr, dass geringe Substanzmengen in die Atmosphäre gelangen. Um sicher zu gehen, dass dies nicht unbemerkt geschieht, werden Anlagen in denen Gefahrstoffe gelagert und verarbeitet werden messtechnisch auf gefährliche Gase überwacht. Prinzipiell bieten sich zwei Messmethoden an: Wärmetönungssensoren oder Infrarotabsorption. Jede Methode hat ihre Vor- und Nachteile. In manchen Anlagen empfiehlt es sich sogar beide zu kombinieren.
Der Wärmetönungssensor als Standardanwendung
Ein Standardbeispiel für den sicheren und kostengünstigen Einsatz von Wärmetönungssensoren wäre z.B. ein Einzelbetrieb mit gleich bleibenden Einsatzstoffen, End- und Nebenprodukten. Die Sensoren verbrennen katalytisch die zu messende Substanz und erhöhen dadurch ihre Temperatur. Die Temperaturerhöhung führt zu einer Erhöhung des inneren elektrischen Widerstands des Sensors. Der Widerstand ist eine einfach zu messende elektrische Größe. Die Sensoren sind dementsprechend einfach aufgebaut und daher preisgünstig.
Allerdings benötigt ein einfacher Wärmetöner eine Elektronik, die ihm die erforderliche Heizspannung für die Messbrücke zur Verfügung stellt und das Signal auswertet. In der Regel ist diese in 19" Racks in der Messwarte untergebracht. Modernere Systeme verwenden auch Kontrollmodule zur DIN-Schienen-Montage.
Auf Grund ihres Designs detektieren Wärmetönungssensoren alle brennbaren Substanzen - wenn auch nicht mit gleicher Empfindlichkeit: Eine Gaswarnanlage muss also auf die zu messende Substanz justiert werden. Sinnvollerweise stellt man den Messbereich auf 0-100 % UEG (Untere Explosionsgrenze - eine stoffspezifische Größe, die sich im Konzentrationsbereich von 1,5-15,5 Volumen-% bewegt) ein.
Beim sog. "primären Explosionsschutz" muss man die tatsächliche Konzentration einer Substanz gar nicht unbedingt wissen, man muss aber wissen ob die Atmosphäre sich in ein zündfähiges Gemisch verwandeln wird. Deshalb stellt man die Alarme typischerweise auf 20 und 50 % UEG ein, um im Alarmfall noch genügend Zeit zum Handeln zu haben.
In einem Einzelbetrieb ist die Justage einfach, da die zu messende Substanz bekannt und immer dieselbe ist. Ist diese Substanz gasförmig, genügt es den Sensor mit einem Gas-Luft-Gemisch bekannter Konzentration zu beaufschlagen. Hierbei ist zu beachten, dass Gas-Stickstoff-Gemische ungeeignet sind, da Sauerstoff zur Oxidation des Messgases auf der Sensoroberfläche benötigt wird.
Schwierigkeiten kann die Justage auf flüssige Stoffe machen. Es ist ziemlich aufwändig Dampf-Luft-Gemische mit Genauigkeit vor Ort herzustellen. In diesem Fall ist der Anwender gut beraten, bereits vom Hersteller den Referenzfaktor der Flüssigkeit zu einem Referenzgas ermitteln zu lassen. Dann kann bei der Kalibrierung oder Justierung im Feld, dass wesentlich einfacher zu handhabende Gas verwendet werden. Wertvolle Hinweise zum Betrieb von Gaswarneinrichtungen gibt das Merkblatt BGI 518 der BG Chemie.
Die hier beschriebene Gaswarneinrichtung stellt eine messtechnisch saubere Problemlösung dar, die bei regelmäßiger Wartung zuverlässige und genaue Messergebnisse liefert. Es ist allerdings darauf zu achten, dass die Betriebsbedingungen gleich bleiben. Wechseln z.B. die Einsatzstoffe, ist zu prüfen ob diese ebenfalls ausreichend genau angezeigt werden. Im Zweifelsfall muss die Gaswarnanlage auf den neuen Stoff justiert werden.
Darüber hinaus ist zu prüfen, ob nicht etwa Substanzen vorkommen, die den Katalysator vergiften können, ob über einen längeren Zeitraum hohe Konzentrationen anstehen können oder ob Sauerstoffmangel auftreten kann. Ist dies der Fall, muss in kürzeren Intervallen kalibriert oder sogar auf alternative Messtechnik umgerüstet werden. Sensoren, die vergiftet wurden, können nämlich nach wie vor eine saubere Null anzeigen, d. h. der Zustand einer unerkannten Unverfügbarkeit ist bei Wärmetönungssensoren durchaus denkbar. Dies muss bereits bei der Planung der Anlage und bei der Festlegung der Kalibrierintervalle berücksichtigt werden.
Ein typisches Beispiel für ein Gaswarnsystem mit Wärmetönungssensoren ist der Compur Statox 501 HRC. Der Controller des Statox 501 kann per Tastendruck auf verschiedene Brückenspannungen programmiert werden, so dass für jede Applikation der optimale Sensor ausgewählt werden kann. Wenn Flüssigkeiten detektiert werden sollen, bietet der Hersteller eine Bestimmung des Referenzfaktors Flüssigkeit/Standard Kalibriergas an. Der Betreiber kann dann bequem mit Prüfgas arbeiten, indem er die Anzeige bei der Beaufschlagung mit Gas mit diesem Faktor multipliziert.
Der Wärmetönungssensor. Einer für fast alle Fälle
An einem Standort mit vielen unterschiedlichen Betrieben sieht sich der Instrumentierer und Betreuer mit zahlreichen verschiedenen Anwendungsfällen und noch viel mehr unterschiedlichen Messgasen konfrontiert. Da liegt es nahe, sich ein Messsystem zu suchen, das möglichst alle Problemstellungen bewältigen kann. Wenn auch mit einigen Einschränkungen kann durchaus der Wärmetöner die geeignete Problemlösung sein.
Er zeigt zwar alles an was explodieren könnte aber eben leider mit unterschiedlicher Empfindlichkeit. Wenn man aber mit folgenden Prämissen leben kann: Der Normalzustand in allen zu überwachenden Betrieben ist, dass die Konzentration brennbarer Substanzen gleich "null" ist, d. h. die Sensoren sind nicht permanent Gas ausgesetzt.
Der Alarm wird ausgelöst, wenn eine Abweichung vom Normalzustand eintritt. Der Alarm wird bereits weit unterhalb der UEG ausgelöst, d. h. in manchen Fällen wird viel zu früh Alarm auslöst, niemals aber zu spät. Dann kann man nahezu alle Messköpfe am Standort auf eine Referenzsubstanz justieren. Gebräuchlich ist hier Nonan. Nonan hat als Einsatzstoff bei der Produktion keine Bedeutung, wird aber gerne als Referenz herangezogen da Wärmetöner wegen seiner sehr niedrigen UEG vergleichsweise unempfindlich darauf reagieren. Eine Nonanjustierung nennt man daher häufig auch "Sicherheitskalibrierung". Allerdings ist Nonan eine Flüssigkeit. Um eine Feldkalibrierung mit vertretbarem Aufwand zu gewährleisten, sollte man für jeden Sensor den Referenzfaktor zu einem Gas ermitteln oder vom Hersteller ermitteln lassen.
Gebräuchlich an einigen Chemiestandorten ist auch die Einstellung auf 0-10 % UEG Ethylen. Ethylen ist ein Gas und daher einfach zu handhaben. Es ist nicht toxisch, preisgünstig zu beschaffen und bleibt in Gasflaschen über lange Zeit stabil.
Zwar macht man bei der generellen Kalibrierung auf eine Referenzsubstanz erhebliche Kompromisse bei der Messgenauigkeit, kann aber die Kosten für Wartung, Ersatzteilhaltung und die Bereitstellung von Kalibriergas erheblich reduzieren.
Eine solche generelle Problemlösung ist aber nur dann empfehlenswert wenn die Betriebsbedingungen sehr genau analysiert wurden. Vor allem muss sichergestellt sein, dass keine Katalysatorgifte auftreten können. Außerdem muss sichergestellt sein, dass das einsetzte Gaswarnsystem bei der oben beschriebenen Justierung alle potentiell vorhandenen Gase empfindlich genug anzeigt. Dies ist im Zweifelsfall durch Versuche zu ermitteln.
Ein typischer Vertreter dieser Kategorie ist der Compur Statox 501 ARE. Er ist auf die möglichst empfindliche Anzeige aller Arten von Treibstoffen und Lösemittel optimiert. Er eignet sich für eine Referenzkalibrierung mit 10 % UEG Ethylen.
KONTAKT
Bernd Rist
Compur Monitors GmbH & Co. KG, München
Tel.: 089/62038-0
Fax: 089/62038-184
compurmonitors@t-online.de
www.compur.de