Safety Services in der Praxis
Maschinenbetreiber müssen die Sicherheit der von ihnen eingesetzten Maschinen und Anlagen gewährleisten. Hilfreich kann dabei eine „Standortbestimmung" im Sinne einer einheitlich...
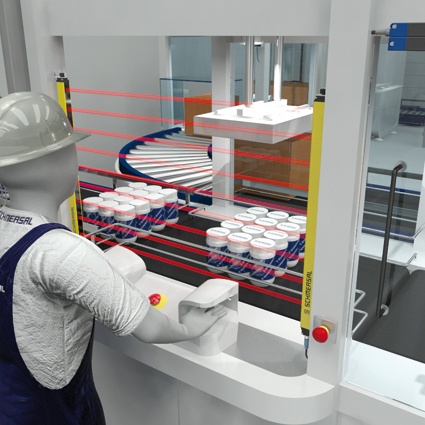
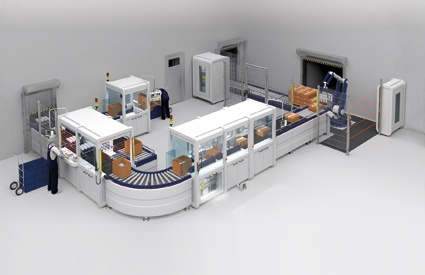
Maschinenbetreiber müssen die Sicherheit der von ihnen eingesetzten Maschinen und Anlagen gewährleisten. Hilfreich kann dabei eine „Standortbestimmung" im Sinne einer einheitlichen sicherheitstechnischen Bewertung sein - mit dem Ziel, Schwachstellen zu erkennen. Das gibt dem Betreiber die Gewissheit, dass die Maschinen den aktuellen Normen und Richtlinien entsprechen und die Mitarbeiter somit an sicheren Maschinen arbeiten.
Typischerweise ist der Maschinenpark eines produzierenden Unternehmens sehr heterogen strukturiert. Er besteht aus alten und neuen Anlagen, die zum Teil umgebaut, erweitert, modernisiert oder verkettet wurden - mit eigenen Mitteln oder durch externe Unternehmen.
Sind die Maschinen sicher?
Die Frage, ob alle Maschinen sicher arbeiten, ist deshalb berechtigt. Entsprechen sie den geltenden Standards der Maschinensicherheit, die in der Maschinenrichtlinie und der ihr nachgeordneten Normen festgelegt sind? Stellt der Anwender vielleicht eigene Anforderungen oder hat er Standards definiert, deren Einhaltung zu überprüfen ist?
Diese Fragen treten entweder dann auf, wenn ein Sicherheitsmangel entdeckt wurde oder wenn Maschinen oder komplette Produktionslinien von einem Standort zu einem anderen verlagert wurden. Auch bei der Übernahme von Unternehmen mit Fertigungsbetrieben stellt sich beim Käufer oft die Frage, ob die Produktionseinrichtungen den eigenen Sicherheitsstandards entsprechen. In diesen Fällen bietet sich ebenfalls eine sicherheitstechnische Analyse des Maschinenparks an.
Bewertung an vierzehn Standorten und über 2000 Maschinen
Der Geschäftsbereich „Safety Services" von Schmersal hat Erfahrungen darin, diese Fragen zu beantworten und entsprechende Aufgabenstellungen systematisch abzuarbeiten. Kürzlich haben die Mitarbeiter dieses Geschäftsfeldes ein Projekt abgeschlossen, das wegen seiner schieren Dimension außergewöhnlich war.
Ein weltweit aktives Unternehmen der Medizintechnik hat sich mit einem anderen Konzern derselben Branche zusammengeschlossen und sah sich nun vor die Herausforderung gestellt, die Produktionsstätten und -prozesse zu bewerten und möglichst zu vereinheitlichen. Auch die Maschinensicherheit sollte untersucht und an allen Standorten auf ein gleichmäßig hohes Niveau gebracht werden. Insgesamt handelte es sich um über 2000 Maschinen an vierzehn Standorten allein in Deutschland, Österreich und der Schweiz, die zu bewerten waren. Mit diesem Projekt wurde der Geschäftsbereich „Safety Services" der Schmersal Gruppe beauftragt.
Einheitliche Standards erarbeitet
Im ersten Schritt erarbeiteten die beteiligten Schmersal-Mitarbeiter gemeinsam mit dem Kunden eine Matrix, nach der jede einzelne Maschine bewertet werden sollte. Dabei konnten sie auf einer Software aufsetzen, die bereits im Unternehmen angewendet wurde.
Das Ergebnis dieser Arbeit waren 90 zu bewertende Eigenschaften, die es an jeder Maschine zu untersuchen galt. Berücksichtigt wurden neben den einschlägigen Normen und Richtlinien auch Aspekte des Manipulationsschutzes sowie der Ergonomie - und das bei sehr heterogenen Maschinenparks, weil die einzelnen Standorte ganz unterschiedliche Produkte herstellen. Die Resultate der Maschinenbewertung wurden vor Ort direkt in die vorhandene Software eingegeben, so dass sie nicht mehr separat dokumentiert werden mussten.
Einheitliche Vorgehensweise an den Produktionsstandorten
Die Vorgehensweise der Sicherheits-Experten an den einzelnen Standorten war stets identisch und ebenfalls im Vorfeld festgelegt worden. Die Schmersal-Mitarbeiter erläuterten den Verantwortlichen im jeweiligen Betrieb zunächst ihre Aufgabe. Dann folgten eine gemeinsame Begehung und die standardisierte Bewertung jeder einzelnen Maschine. Als Abschluss wurden die Ergebnisse und die gewonnenen Erkenntnisse im Unternehmen präsentiert.
Kernaufgabe in drei Monaten erledigt
Die Schmersal Gruppe konnte bei dieser Aufgabe auf Functional Safety Engineers aus drei Landesgesellschaften zurückgreifen. Darüber hinaus wurde die Ressourcen des CE-Netzwerkes genutzt. Dieses von Schmersal initiierte Netzwerk besteht aus zwölf unabhängigen Ingenieurbüros, die sich jeweils auf Einzelaspekte und definierte Arbeitsbereiche der Maschinensicherheit spezialisiert haben.
Mit dieser qualifizierten „Manpower" konnten alle Standorte und über 2.000 Maschinen innerhalb von drei Monaten bewertet und die Ergebnisse dokumentiert werden. Das Projekt ist somit abgeschlossen. Aber es stehen Folgeprojekte an, z. B. eine Bewertung der Standorte auf anderen Kontinenten.
Die Schmersal Gruppe sieht sich auch für solche Aufgaben bestens vorbereitet. Zum Beispiel haben die Kollegen der amerikanischen Schmersal-Landesgesellschaft schon umfangreiche Erfahrungen mit derartigen Maschinenbewertungen sammeln können.
Verlagerung einer Produktionslinie
In einem anderen Projekt verlagerte ein internationaler Automobilkonzern eine Produktionslinie für Kfz-Getriebe von einer europäischen Fertigungsstätte und auch von einer Konzernmarke zu einer anderen. Dabei stellte sich die Frage, ob die Sicherheitsanforderungen entsprechend der Werksnormen erfüllt werden. Auf der Basis der EN-Normen und eben dieser Werksnormen haben Functional Safety Engineers von Schmersal alle Einzelstationen der verketteten Anlage untersucht.
Nachlaufzeitmessung an rund 450 Gefahrstellen
Die „Safety Services", die Schmersal anbietet, sind nicht immer so umfangreich wie die beiden dargestellten Beispiele. Oft handelt es sich „nur" um einzelne Maschinen oder auch Maschinenfunktionen, die im Hinblick auf die Sicherheit zu bewerten sind. Und manchmal sind es nicht Einzelprojekte, sondern kontinuierliche Dienstleistungen. Auch hier ein Beispiel: Im Werk eines namhaften europäischen Automobilzulieferers sind die Ingenieure von Schmersal verantwortlich für die regelmäßige Prüfung von 450 Sicherheits-Lichtvorhängen und -Lichtgittern.
Diese optoelektronischen Schutzeinrichtungen müssen laut BetrSichV (TRBS 1203) regelmäßig daraufhin überprüft werden, ob beim Auslösen der Stopp-Funktion ein rechtzeitiges Anhalten der gefahrbringenden Bewegung gewährleistet ist. In der Praxis kann sich durchaus die Nachlaufzeit der Schutzeinrichtung verlängern - etwa wenn schwerere Werkzeuge eingesetzt werden oder durch Verschleiß an beweglichen mechanischen Komponenten. Mit der Methodik der Nachlaufzeitmessung lässt sich dokumentieren, dass der Anwender und der Bediener der Maschine im wahrsten Sinne des Wortes auf der sicheren Seite sind.
Meist gelesen
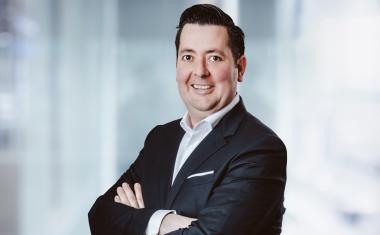
Disruptiv aus Überzeugung - Interview mit Carsten Simons über technologische Unabhängigkeit, mutige Weiterentwicklung und die Zukunft der mobilen Videoüberwachung
LivEye-Chef Carsten Simons über Disruption, technologische Unabhängigkeit und das neue Überwachungssystem NSTR
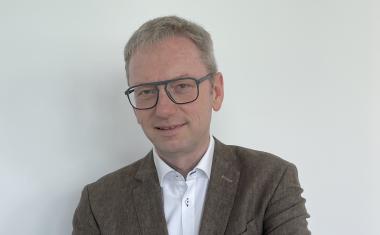
VDMA-Einheitsblatt 24994: Lithium-Ionen-Batterien im Fokus
VDMA 24994 Anforderungen und Prüfverfahren für Lithium-Ionen-Schränke im Interview mit Priorit erläutert
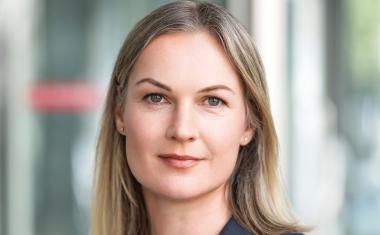
VIP-Interview: Dr. Alexandra Forster, Konzernsicherheit Bayer
GIT SICHERHEIT im Interview mit Dr. Alexandra Forster, Leiterin Konzernsicherheit bei der Bayer AG.
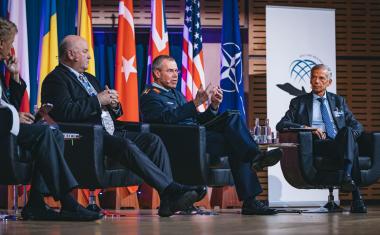
Euro Defence Expo und NATO JAPCC parallel zur Security Essen 2026
Vom 22. bis 25. September 2026 wird die Euro Defence Expo (Eudex) ihre Premiere in der Messe Essen begehen – gleichzeitig mit der jährlichen Konferenz des NATO Joint Air Power Competence Centre sowie der Security Essen.
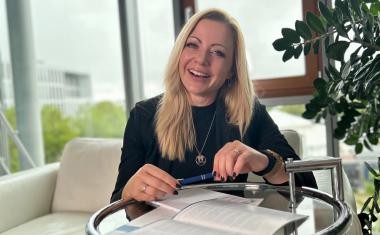
Schutz für exponierte Personen und wohlhabende Familien
Personenschutz für Vermögende: Christina Schwung über Risiken, Schutzkonzepte und digitale Bedrohungen