Sauber und sicher - M12-Verkabelung für die Lebensmittel-Industrie
Steckverbinder sind in der Lebensmittel-Industrie nicht neu - allerdings werden sie nicht in allen Teilen der Anlage eingesetzt. Anhaftungen am Steckverbinder gilt es zu vermeiden...
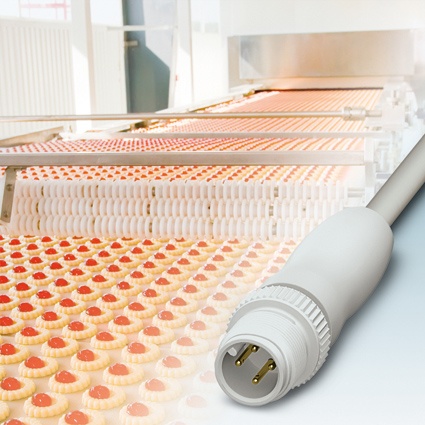
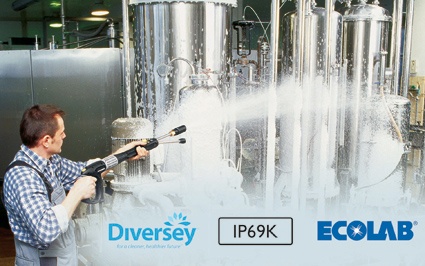
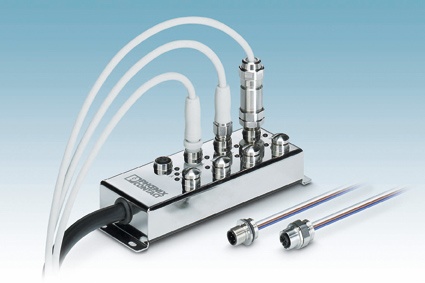
Steckverbinder sind in der Lebensmittel-Industrie nicht neu - allerdings werden sie nicht in allen Teilen der Anlage eingesetzt. Anhaftungen am Steckverbinder gilt es zu vermeiden, damit Lebensmittel nicht bakteriell verunreinigt werden.
Ein neues Design-Konzept und die technische Weiterentwicklung der M12-Steckverbinder von Phoenix Contact ermöglichen nun erstmals den Einsatz in Bereichen, in denen die Komponenten mit Lebensmitteln in Kontakt kommen können.
Die Anforderungen an Maschinen und Anlagen in der Lebensmittel-Industrie gehen weit über den Standard des klassischen Maschinenbaus hinaus. Alle Oberflächen müssen eben sowie ohne Spalten oder Zwischenräume gestaltet sein. Sogenannte Schmutznester sind zu vermeiden, um ein Anhaften von Lebensmitteln zu verhindern. Gesäubert werden die Anlagen oft mit Hochdruck- und Dampfreinigern, die mit aggressiven Reinigungsmitteln auf saurer oder alkalischer Basis arbeiten.
Lebensmittel und deren Verpackungen dürfen generell nicht durch den Kontakt mit Anlagen- und Maschinenteilen verunreinigt werden. Unterschieden werden bei der Produktion drei Zonen: Produktkontaktzone, Spritzzone und produktfreie Zone. Jede Zone stellt spezifische Anforderungen an die Sensorik und Aktorik - und an die jeweiligen Kabel und Steckverbinder.
Die Produktkontaktzone
Jedes Bauteil einer Anlage kann hier mit dem zu verarbeitenden Lebensmittel in Berührung kommen, und das Lebensmittel selbst kann danach zurück in den Verarbeitungsprozess gelangen. In dieser Zone sind die Hygiene-Anforderungen besonders hoch. Steckverbinder und andere Bauteile dürfen hier keine Schmutznester aufweisen.
Eine Lösung bieten die M12-Steckverbinder von Phoenix Contact im Hygienic Design (HD). Die Entwicklung des Designs erfolgte in Anlehnung an die Design-Vorgaben der European Hygienic Engineering & Design Group (EHEDG).
Diese speziell für den Einsatz in der Lebensmittel-Industrie konzipierten Varianten des M12-Steckverbinders haben besonders glatte Oberflächen und bestehen aus FDA-konformen Materialien: V4A-Edelstahl (1.4404) für die Metallteile (Schraube, Mutter und Schirmhülse) sowie PP(Polypropylen)-basierte Umspritz-Kunststoffe und Leitungsmaterialien.
Auch die Dichtungsmaterialien der O-Ringe sind FDA-konform. Weil PP als Grundmaterial für die Umspritzung und für den Leitungsmantel verwendet wird, ist die Medienbeständigkeit extrem hoch. Die Nachteile PVC-basierter Lösungen spielen keine Rolle mehr. Mit PP gibt es kein Verhärten und Verfärben des Materials, alle dichtenden und optischen Eigenschaften bleiben langfristig erhalten. Mit den Schutzklassen IP65, IP68 (2m/24h) und IP69K erfüllen die M12-HD-Steckverbinder auch die hohen Reinigungsanforderungen.
Um die Anforderungen der EHEDG und gleichzeitig die Dichtigkeitsanforderungen zu erfüllen, wurde für das Hygienic Design ein neuartiges Dichtkonzept umgesetzt. Die Steckverbinder bilden mit ihrem Gegenstück eine geschlossene und glatte Oberfläche, die leicht zu reinigen ist. Für eine fliegende Kupplung im Feld wurde eine Profildichtung geschaffen, die Stecker und Buchse ebenfalls bündig abdichtet. Schmutznester gehören somit der Vergangenheit an. Die Beschriftung der Leitungen per Laser ermöglicht eine dauerhaft beständige Nachverfolgung.
Die Spritzzone
Auch in der Spritzzone können Bauteile mit dem Lebensmittel in Kontakt kommen. Anders als in der Produktkontaktzone gelangt das Lebensmittel nach dem Kontakt mit den Bauteilen jedoch nicht mehr zurück in den Prozess. Daher müssen auch die Steckverbindungen nicht den Richtlinien des Hygienic Design genügen. Die Steckverbinder, die Phoenix Contact im sogenannten Wash-Down-Design anbietet, wurden speziell für die Applikation Spritzzone konzipiert: ebenfalls glatte Konturen am Griffkörper minimieren Lebensmittelanhaftungen am Steckverbinder. Bei der Auswahl der Materialien wurde wiederum auf PP-basierte Kunststoffe zurückgegriffen, die sowohl für die Umspritzung als auch für die Verschraubung des Steckverbinders eingesetzt werden. Andere marktübliche Wash-Down-Steckverbinder setzen größtenteils auf Edelstahl - V2A oder V4A - als Verschraubungsmaterial. Durch den Verzicht auf Edelstahl im Wash-Down-Design von Phoenix Contact bekommt der Anlagenbauer erstmals einen Steckverbinder, der die Anforderungen der Lebensmittel- und Getränke-Industrie für die Spritzzone erfüllt.
Die produktfreie Zone
Die Bezeichnung „produktfreie Zone" ruft häufig Irritationen hervor. In dieser Zone sind die Produkte nicht verschwunden, sondern meist schon verpackt und nicht mehr direkten Berührungen durch Anlagenteile ausgesetzt. In dieser Zone sind die Anforderungen mit denen im klassischen Industrieumfeld vergleichbar. Die Reinigung der Verpackungsanlagen erfordert keine aggressiven Reiniger und erfolgt meist nicht mit Hochdruckgeräten. Jedoch können Kartonagen und Umverpackungen sowie eventuell austretende trockene Lebensmittel die Umgebungsluft mit Staub belasten. Damit die Steckverbinder staubdicht sind, ist hier ebenfalls eine hohe IP-Schutzart erforderlich.
In dieser Umgebung sind Standard-M12-Steckverbinder sinnvoll - Phoenix Contact bietet hier geeignete Steckverbinder und Leitungen. So kann der Anlagenbauer je nach Anwendungsfall etwa zwischen Robotor- oder Schleppketten-tauglichen Leitungen wählen und bewegliche Anlagenteile, wie Robotergreifarme oder Förderstrecken, anwendungsgerecht verkabeln. Das Produktprogramm umfasst geschirmte wie ungeschirmte Leitungen und Steckverbinder. Als Standardleitung setzt der Hersteller im Bereich der Sensor-/Aktor-Verkabelung auf halogenfreie Leitungen aus Polyurethan (PUR). Diese Leitung eignet sich für zahlreiche Einsatzbereiche in Verpackungsanlagen der produktfreien Zone - bedingt durch gute Schleppkettenwerte, gute Öl- und Hydrolyse-Beständigkeit, Halogenfreiheit sowie eine Flammwidrigkeit nach UL FT2.
Produktprogramm für F&B-Applikationen
Zum Anschluss von Sensoren und Aktoren in der Lebensmittel- und Getränke-Industrie (F&B, Food & Beverage) bietet Phoenix Contact ein durchgängiges und vollständiges System, auf das der Anlagenplaner nun zurückgreifen kann. Neben den erwähnten konfektionierten Leitungen im Hygienic- und Wash-Down-Design enthält es auch konfektionierbare Steckverbinder, Wanddurchführungen und passive Verteiler-Boxen im Wash-Down-Design.
Die gesamte Steckverbinder-Familie wurde für die Reinigungsabläufe in diesen Applikationen konzipiert und ist gegen alle handelsüblichen Reinigungsmittel beständig. Das bestätigen Zertifikate unabhängiger Prüfeinrichtungen - wie Ecolab und Diversey. Die gute Beständigkeit über alle Komponenten des Systems wird durch eine abgestimmte Werkstoffauswahl erreicht. V4A-Edelstahl sowie optimierte Dichtmaterialien und Kunststoffe ermöglichen einen problemlosen Einsatz aller Komponenten in der Lebensmittel-Industrie. Ein weiterer Vorteil des Gesamtsystems ist die gute Abstimmung der Einzelkomponenten aufeinander. Beim Design-In der Komponenten wird der Anlagenplaner durch die Engineering-Software Eplan unterstützt.
Business Partner
Phoenix Contact Deutschland GmbHFlachsmarktstr. 8
32825 Blomberg
Deutschland
Meist gelesen
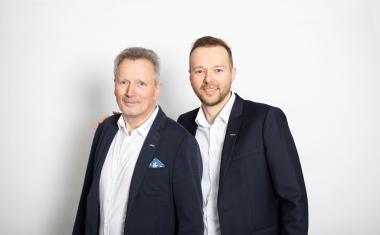
Partner des Fachhandels – Ein Gespräch mit Jürgen Hövelmann von EPS-Vertrieb
Sicherheitslösungen mit Tradition & Innovation: EPS-Vertrieb stellt das Ajax Fire-System vor
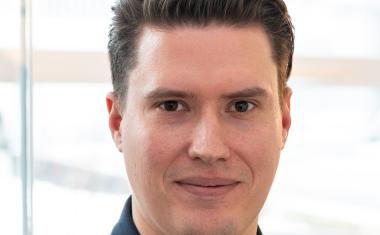
VDMA-Einheitsblatt 24994: Einheitliches Prüfverfahren für die Zertifizierung von Lager-/Ladeschränken für Lithium-Ionen-Akkus
In einer Zeit, in der die sichere Lagerung und das Laden von Lithium-Ionen-Batterien immer wichtiger werden, setzt das VDMA-Einheitsblatt 24994 neue Maßstäbe und definiert klare Anforderungen an Sicherheitsschränke.
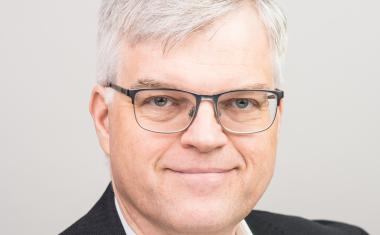
Maschinensicherheit im Kontext von KI und Security – Cyber Resilience Act: Neue Anforderungen für Maschinenbauer
Cyber Resilience Act & Maschinenverordnung: Neue Sicherheitsanforderungen für Maschinenbauer in vernetzten Industrieanlagen
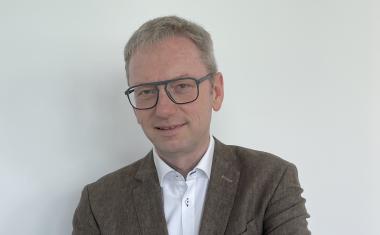
VDMA-Einheitsblatt 24994: Lithium-Ionen-Batterien im Fokus
VDMA 24994 Anforderungen und Prüfverfahren für Lithium-Ionen-Schränke im Interview mit Priorit erläutert
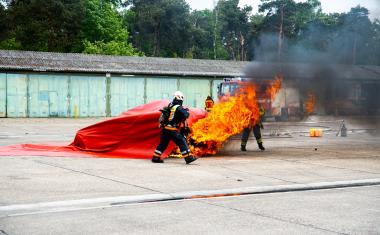
Lithium-Ionen Energiespeicher: Abwehrender und vorbeugender Brandschutz
Lithium-Ionen-Technologie: Hohe Energiedichte, vielseitig einsetzbar, aber auch Risiken im Brandschutz beachten