Worauf es beim sicheren Zugang zu Maschinen und Anlagen ankommt - Interview mit Marcel Wöhner
Die Artikel-Serie in Kooperation von VDMA Elektrische Automation und GIT SICHERHEIT beleuchtet verschiedene Arten von Schutzeinrichtungen und geht der Frage nach, wann welche Schutzmaßnahme/n sinnvoll bzw. erforderlich sind und worauf es bei Auswahl und Einsatz zu achten gilt.
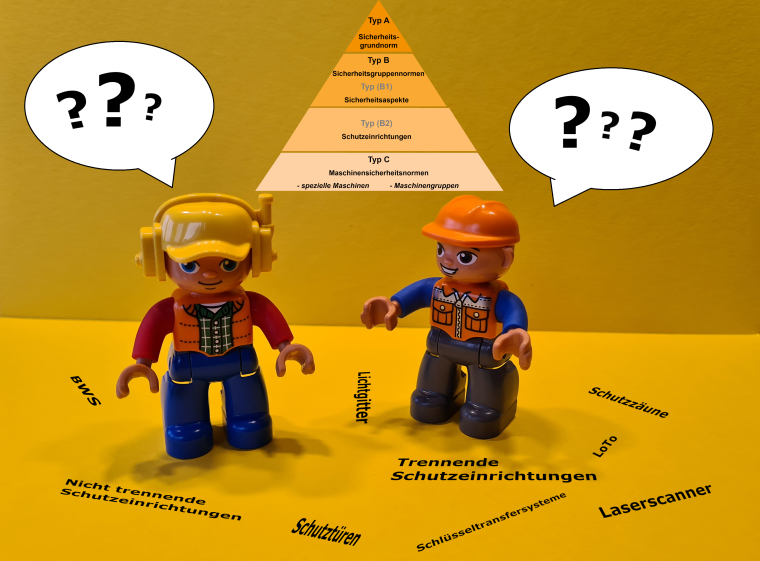
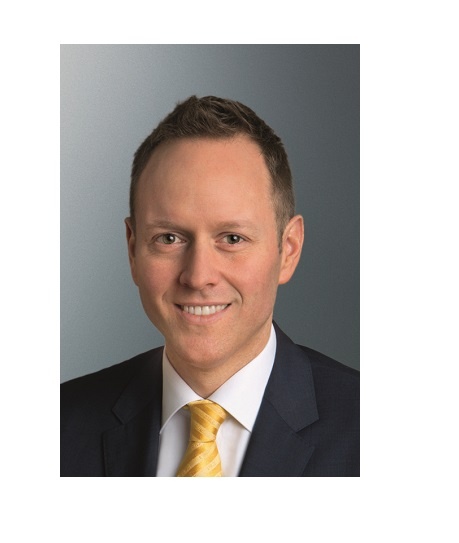

Werden Schutzeinrichtungen an Maschinen außer Kraft gesetzt, steigt die Gefahr für Arbeitsunfälle. Insbesondere während der Instandhaltung beim Betreiber werden Schutzeinrichtungen an Maschinen häufig manipuliert, zum Beispiel wenn der bereitgestellte Funktionsumfang für bestimmte Tätigkeiten nicht ausreicht oder Schutzeinrichtungen als störend empfunden werden.
Die Artikel-Serie in Kooperation von VDMA Elektrische Automation und GIT SICHERHEIT beleuchtet verschiedene Arten von Schutzeinrichtungen und geht der Frage nach, wann welche Schutzmaßnahme/n sinnvoll bzw. erforderlich sind und worauf es bei Auswahl und Einsatz zu achten gilt.
Maschine ist nicht gleich Maschine, Anlage nicht gleich Anlage. Entsprechend unterschiedlich sind die Herausforderungen, mit denen sich Maschinenhersteller konfrontiert sehen, wenn es um deren sicheren Zugang geht. Doch wo liegen die Knackpunkte? Wie definiert man den Bedarf? Welche technischen und organisatorischen Maßnahmen sind notwendig bzw. sinnvoll? Einen einführenden Überblick in unserem ersten Beitrag zur Gemeinschaftsreihe „Sicherer Zugang zu Maschinen und Anlagen“ von VDMA und GIT SICHERHEIT gibt uns Marcel Wöhner, Chief Technical Officer beim Safety-Experten Pilz.
GIT SICHERHEIT: Herr Wöhner, wenn wir über den sicheren Zugang zu Maschinen und Anlagen sprechen, gibt es ja eine ganze Reihe rechtlicher Bestimmungen sowie Normen, die es je nach Fall und Situation einzuhalten gilt. Was sind die wesentlichen rechtlichen Vorgaben und wie gestaltet sich der Umgang bzw. die Anwendung der Normen?
Marcel Wöhner: Wenn wir Maschinen und Anlagen hören, dann denken wir sicherlich gleich an die Maschinenrichtlinie 2006/42/EG (MRL). Bei der Gestaltung sicherer Zugänge zu Maschinen und Anlagen ist es selbstverständlich wichtig die Vorgaben einzuhalten. Dabei richtet sich die MRL, genauer das Produktsicherheitsgesetz (ProdSV), an den Hersteller oder Inverkehrbringer einer Maschine. Der Konstrukteur wird also überlegen, welche Risiken von der Maschine bzw. Anlage ausgehen werden und sichert diese ab. In diesem Zusammenhang spielt aber auch die Betriebssicherheitsverordnung (BetrSichV) als Umsetzung der europäischen Arbeitsmittelbenutzungsrichtlinie (AMBR 2009/104/EG) eine wesentliche Rolle. Dieses Gesetz richtet sich an die Betreiber von Maschinen und Anlagen. Hier wird die Verwendungsphase angeschaut, wobei der Mensch im Fokus steht. Man betrachtet nicht mehr nur, welche Risiken von einer Maschine selbst ausgehen, sondern bewertet alle Gefährdungen, die auf den Menschen, also den Bediener, einwirken. Z. B. könnten sich neue Sicherheitsaspekte durch den Aufstellort oder das Zusammenwirken unterschiedlicher Maschinen ergeben. Zudem muss auch die Rolle bzw. der Aufgabenbereich des einzelnen Bedieners betrachtet werden. Ein Maschinenbediener hat andere Aufgaben und somit auch andere Zugänge zu den Maschinenteilen als beispielsweise ein Instandhalter. So ist also nicht immer ‚nur‘ die Zuhaltung einer Schutztür die Antwort auf die richtige Maßnahme gegen eine Gefährdung.
In der Auslegung der Maschinensicherheit werden generell harmonisierte Normen herangezogen. Dabei unterscheiden wir in Typ A-, B- und C-Normen, also unterschiedliche Level. Die Typ A-Norm EN ISO 12100 ist eine Sicherheitsgrundnorm, die Begriffe, Gestaltungsleitsätze bzw. allgemeine Aspekte behandelt. Darunter finden sich die Typ B1-Normen, die bestimmte Sicherheitsaspekte maschinentypübergreifend beschreiben. Die Typ B2-Normen gehen etwas konkreter auf unterschiedliche Schutzeinrichtungen ein. Auch sie finden wiederum übergreifend Anwendung. Erwähnen möchte ich hier insbesondere die EN ISO 14120 für trennende Schutzeinrichtungen oder die EN ISO 14119 für Verriegelungseinrichtungen. Erst auf dem Level der Typ C-Normen sind detaillierte Sicherheitsanforderungen an eine bestimmte Maschine oder Gruppe von Maschinen beschrieben. In den Maschinensicherheitsnormen lassen sich Gestaltungsvorgaben für konkrete Maschinentypen finden wie beispielsweise in der EN ISO 10218-1/2 für Industrieroboter oder EN ISO 16092-1 für Pressen.
Rechtliche Bestimmungen und Normen sind das eine, konkrete und reale Situationen das andere: Wie genau sehen denn erste Schritte im konkreten Fall tatsächlich aus?
Marcel Wöhner: Nehmen wir ein allgemein bekanntes Beispiel: die Schutztür eines Bearbeitungszentrums, z. B. einer Dreh- oder Fräsmaschine. Im normalen Bearbeitungsprozess haben wir schnelle Bewegungen, angetriebene Werkzeuge sowie herumfliegende Späne. Türen, Hauben und Klappen sind beweglich trennende Schutzeinrichtungen und können mit einer Verriegelungseinrichtung verbunden sein. Diese sorgen dafür, dass bei geöffneter Schutztür gefährliche Maschinenfunktionen gestoppt werden und ein unerwarteter Wiederanlauf zuverlässig verhindert wird. D. h. also, bei richtiger Auslegung sind die EN ISO 14120 für trennende Schutzeinrichtungen, die EN ISO 14119 für Verriegelungseinrichtungen sowie die EN ISO 14118 für den Schutz vor unerwarteten Anlauf berücksichtigt. Wäre diese Maschine etwas größer dimensioniert, ließe sich die Zugangstür schließen und der Bearbeitungsprozess starten, obwohl sich ggf. Wartungspersonal im Arbeitsraum befindet. Spätestens der Betreiber muss in seiner Gefährdungsbeurteilung solche Möglichkeiten identifizieren und entsprechende Maßnahmen dagegen ergreifen.
Wie grenzt sich dieser Themenkomplex von anderen Themen der „Funktionalen Sicherheit“ ab?
Marcel Wöhner: In der Zugangsgestaltung ist der Fokus auf der Interaktion des Menschen mit der Maschine. Es ist nicht das Bedien-Interface der Anlage, aber doch die Fragestellung, wie die Aufgaben ausgeführt werden sollen, in welche Bereiche man gelangen muss und wie dafür der Zugang gestaltet werden kann. Natürlich kommen noch Systembeschaffenheit, Kategorien, Fehlererkennung, Performance Level und alle anderen Aspekte mit dazu, die uns sonst aus der Funktionalen Sicherheit geläufig sind. Aber trotz normkonformer Konstruktion oder Auslegung können in der Praxis gefährliche Situationen entstehen. Die Frage, ob ein Mensch mit den notwendigen Barrieren arbeiten kann, muss geklärt sein. Sonst schafft man unweigerlich Anreize zur Manipulation – also dem Ausbauen oder Überbrücken notwendiger Schutzmaßnahmen.
Die unterschiedlichen Produktarten mit ihren jeweiligen Vorzügen oder Eignungen für die Absicherung von Zugängen müssen im Blick sein: Speziell an Be- und Entnahmestellen z. B. mit sehr häufigem Eingreifen in den Prozess eignen sich aufgrund der automatischen Abschaltung berührungsloswirkende Schutzeinrichtungen (BWS) wie Lichtgitter. BWS wird auch als willensunabhängiges Schutzsystem bezeichnet, das den Zugang erkennt, aber nicht verhindert. Durch die Barrierefreiheit löst der Bediener die Abschaltung unabsichtlich aus, gibt sie aber auch beim Verlassen des Schutzfeldes wieder automatisch frei. Dem Bediener ist nicht bewusst, dass er Maschinenfunktionen oder den Zugang in einen Gefahrenbereich abschaltet. Wenn Zugänge aber nur selten genutzt werden, eignen sich trennende Schutzeinrichtungen in Verbindung mit elektromechanischen Verriegelungsgeräten mit Zuhaltung oder sogar ein rein mechanisches Schlüsseltransfersystem. Der Mensch nimmt dann eine Tür bewusst wahr und entscheidet willentlich, ob diese geöffnet wird.
Um eine optimale Auswahl bei der Gestaltung sicherer Zugänge zu Maschinen treffen zu können, ist es immens wichtig, ein grundlegendes Verständnis der unterschiedlichen Produktarten sowie eine Übersicht zu Vorteilen und Eigenheiten hinsichtlich des Einsatzgebietes zu haben.
Wenn wir von Sicherheitsmaßnahmen sprechen, unterscheidet man in der Regel zunächst zwischen technischen und organisatorischen Maßnahmen. Welche technischen Maßnahmen gibt es und wann kommen diese zur Anwendung?
Marcel Wöhner: Ganz grundsätzlich sind technische Maßnahmen zu bevorzugen, um Menschen gegen Gefährdungen, sprich Verletzung, zu schützen. Wichtig ist aber, dass neben dem eigentlichen Bearbeitungsprozess auch andere Maschinen-Lebensphasen betrachtet werden und zusätzlich weitere Rollen bzw. Aufgaben berücksichtigt sind. So machen Einstellarbeiten, Wartung oder auch Materialzuführung und Entnahme einen Zugang in den Gefahrenbereich zwingend erforderlich. Es ist nicht nur unwirtschaftlich, die Maschine jedes Mal komplett energiefrei zu schalten. In manchen Situationen sind Prozessbeobachtung oder weitere Maschinenfunktionen zwingend notwendig.
Der Betreiber einer Anlage trägt die Verantwortung für die Mitarbeiter, die teilweise an den Gefahrenstellen arbeiten müssen. Dabei werden bestehende technische Absicherungen häufig um organisatorische Maßnahmen ergänzt. Meist ist es sinnvoll, eine bestimmte Reihenfolge beim Stillsetzen eines Anlagenteils einzuhalten oder auch beim Eintreten in einen Gefahrenbereich eine Wartungssicherung zum Selbstschutz anzubringen. Solche Abfolgen ordnen wir schnell unter Lockout-Tagout (LOTO) Mechanismen ein. Eine Abschaltprozedur muss aber nicht nur beschrieben sein, sie kann beispielsweise mittels Schlüsseltransfersystem auch technisch erzwungen werden.
Zum Schluss wollen wir noch einmal kurz auf die organisatorischen Maßnahmen eingehen: Warum sind diese im europäischen Raum kein adäquater Ersatz für technische Sicherheitsmaßnahmen?
Marcel Wöhner: Sicher sind Gefahrenstellen denkbar, für die bislang keine geeigneten technischen Sicherheitslösungen existieren. Hier sind dann organisatorische Maßnahmen unabdingbar. Um Manipulationsanreize zu bekämpfen, müssen bei technischen Absicherungsmaßnahmen an Maschinenzugängen die jeweiligen Produkte optimal nach den applikativen Anforderungen ausgesucht werden. Schlussendlich und ganz klar zu unterstreichen: Die MRL formuliert deutlich, dass technische Maßnahmen zur Risikominderung den organisatorischen Maßnahmen vorzuziehen sind.
Die Maschinenrichtlinie 2006/42/EG ist als europäische Richtlinie eine Vorlage für die nationale Gesetzgebung, in Deutschland für das Produktsicherheitsgesetzt (ProdSV). Die Neufassung der Maschinenrichtlinie wird als Maschinenverordnung 2023/1230/EU zum Stichtag 20. Januar 2027 in Kraft treten. Im Unterschied zur Richtlinie entfaltet eine Verordnung direkte Gesetzwirkung in allen Mitgliedsstaaten der EU.
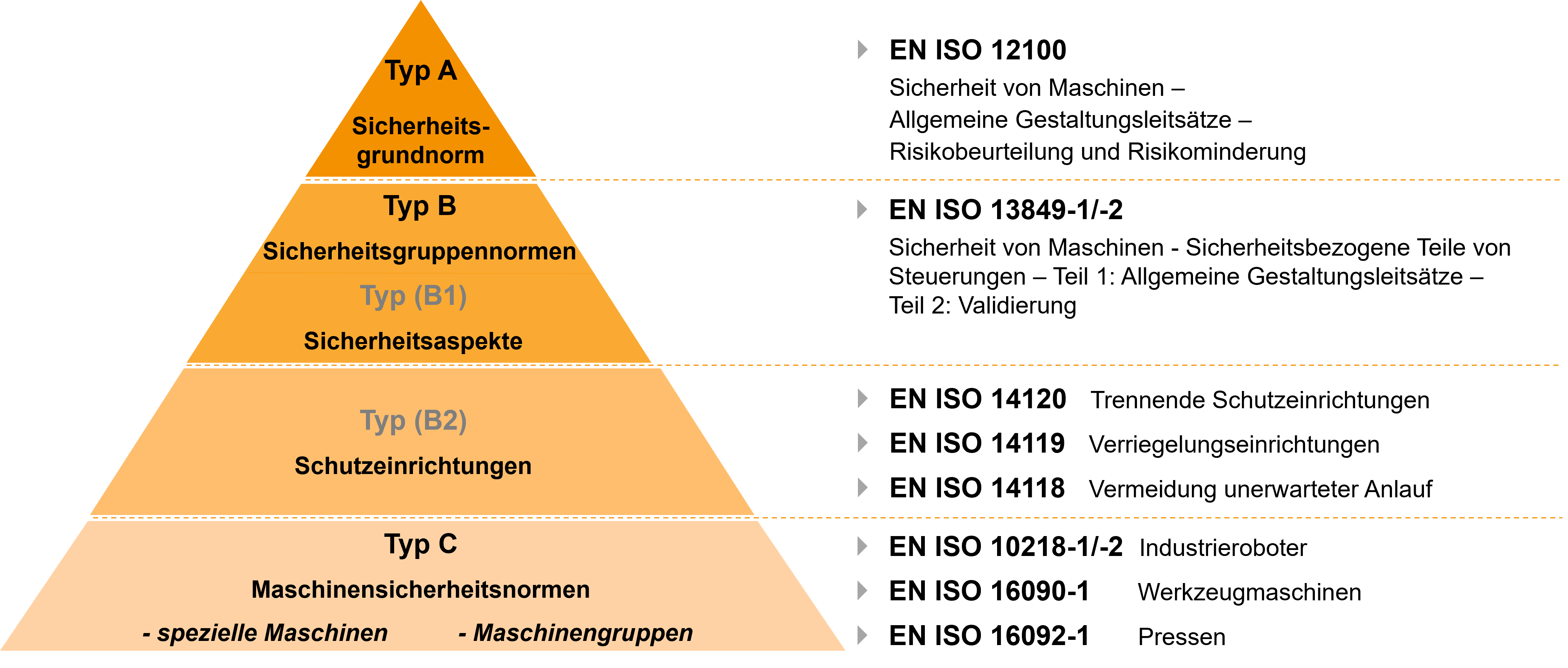
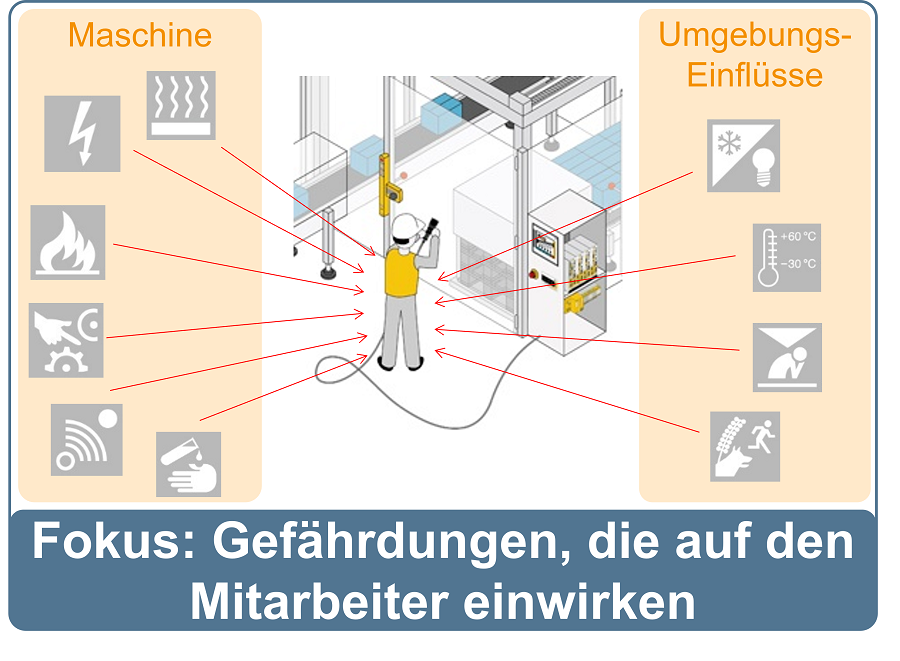
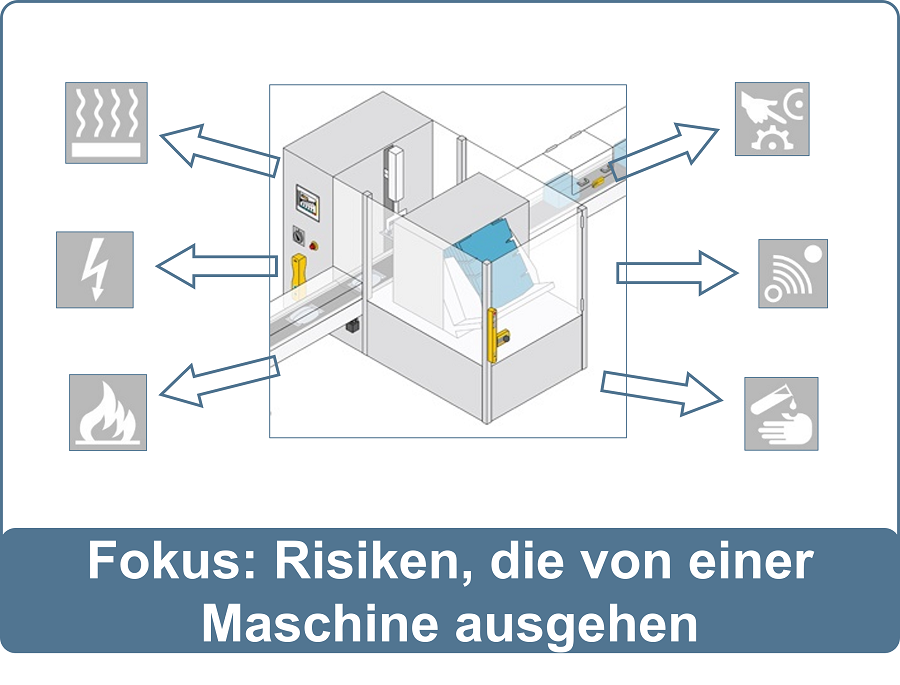
Business Partner
VDMA Verband Deutscher Maschinen- und Anlagenbau e.V.Lyoner Str. 18
60528 Frankfurt
Deutschland
Meist gelesen
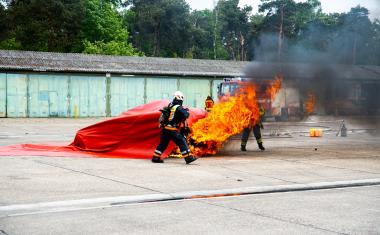
Lithium-Ionen Energiespeicher: Abwehrender und vorbeugender Brandschutz
Lithium-Ionen-Technologie: Hohe Energiedichte, vielseitig einsetzbar, aber auch Risiken im Brandschutz beachten
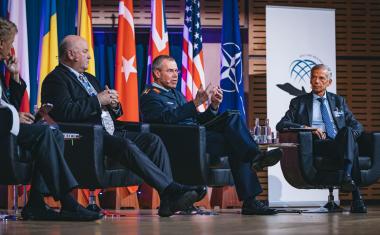
Euro Defence Expo und NATO JAPCC parallel zur Security Essen 2026
Vom 22. bis 25. September 2026 wird die Euro Defence Expo (Eudex) ihre Premiere in der Messe Essen begehen – gleichzeitig mit der jährlichen Konferenz des NATO Joint Air Power Competence Centre sowie der Security Essen.
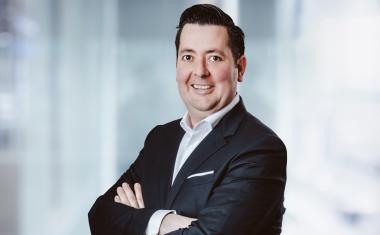
Disruptiv aus Überzeugung - Interview mit Carsten Simons über technologische Unabhängigkeit, mutige Weiterentwicklung und die Zukunft der mobilen Videoüberwachung
LivEye-Chef Carsten Simons über Disruption, technologische Unabhängigkeit und das neue Überwachungssystem NSTR
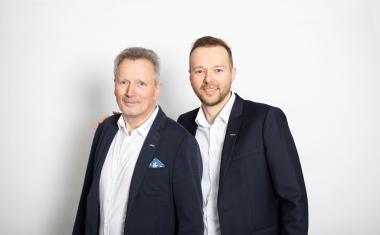
Partner des Fachhandels – Ein Gespräch mit Jürgen Hövelmann von EPS-Vertrieb
Sicherheitslösungen mit Tradition & Innovation: EPS-Vertrieb stellt das Ajax Fire-System vor
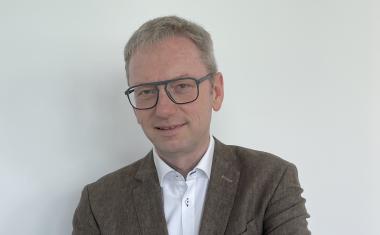
VDMA-Einheitsblatt 24994: Lithium-Ionen-Batterien im Fokus
VDMA 24994 Anforderungen und Prüfverfahren für Lithium-Ionen-Schränke im Interview mit Priorit erläutert