Automatisierung: Industrie 4.0 verändert alle Branchen
Ob nun Revolution oder Evolution - wir befinden uns auf dem Weg in die Welt der „Industrie 4.0". Vorreiter ist unter anderem die Automobilindustrie, aber auch alle anderen Branche...
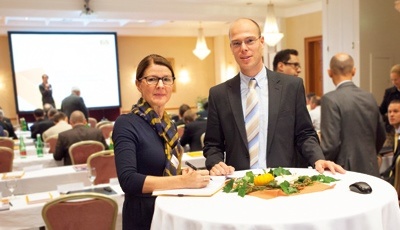
Ob nun Revolution oder Evolution - wir befinden uns auf dem Weg in die Welt der „Industrie 4.0". Vorreiter ist unter anderem die Automobilindustrie, aber auch alle anderen Branchen nehmen immer stärkeren Anteil an dieser Entwicklung - sagt Stefan Schönegger, Marketing Manager bei B&R im Gespräch mit GIT-SICHERHEIT.de.
GIT-SICHERHEIT.de: Herr Schönegger, der Begriff „Industrie 4.0" hängt unter anderem mit einer Entwicklung zusammen, die mit den Kunden und ihren individuellen Wünschen zu tun hat: Der Kunde gewinnt stärkeren Einfluss auf den Produktionsprozess. Wie kann man sich das genau vorstellen?
Stefan Schönegger: Am besten werfen wir einen Blick auf die Entwicklung in der Automobilindustrie. Die Massenfertigung hat mit Fords T-Modell Einzug gefunden. Maßgeblich war die Reduktion auf ein einziges Modell. Selbst die Farbe wurde auf Schwarz beschränkt. Aus dieser Zeit stammt der berühmte Ausspruch von Henry Ford: ‚ You can have any color as long as it‘s black.' Heute ist die Welt bunter. Es genügt ein Blick auf die Internetseiten der Automobilhersteller, um einen Einblick auf die Vielfalt zu erhalten. Komplexe Konfiguratoren mit zig Varianten und Optionen ermöglichen beinahe die Definition von Unikaten. Der Anwender kann sich sein Auto selbst definieren und der Produktionsprozess wird genau anhand seiner Wünsche abgearbeitet. Der Kunde greift somit direkt in das ERP-System und darauf folgend in den Produktionsbetrieb ein. Natürlich sind diesem Prozess heute noch Grenzen gesetzt, zum Beispiel muss sich der Kunde bei der Wahl der Karosserie zu meist mit einer Auswahl aus vier oder fünf Optionen begnügen. Auch die Möglichkeiten an Varianz in den Lackieranlagen sind begrenzt. Aber der Weg geht ganz klar hin zu Losgröße 1. Darauf müssen sich Maschinenlieferanten sowie Automatisierer ausrichten.
Abgesehen von der von Ihnen gerade angesprochenen Automobilindustrie - von welchen Branchen oder Produkttypen sprechen wir dabei noch? Ist das weitere Vorantreiben der Customization in diesem Sinne nicht nur in bestimmten Branchen ein Thema?
Stefan Schönegger: Alle Industrien sind betroffen. Denken Sie an Handys mit beliebigen Covers, Fotobücher vom eigenen Urlaub bis hin zu Lebensmitteln mit individualisierten Verpackungen. Selbst im Bereich der Pharmaindustrie gibt es Blisterverpackungen mit bereits individuell zusammengestellten Medikamenten. Im Krankenhaus erhält so jeder Patient vollautomatisiert exakt die für ihn verschriebene Medikation. Menschliche Fehler bei der Zusammenstellung werden dadurch gänzlich eliminiert. Beispiele von Kunden, mit denen wir diese Wege bereits beschreiten, sind Krones und Dividella. In unserem eigenen Werk verfolgen wir konsequent diesen Weg. Wir bieten unseren Kunden zum Beispiel die Möglichkeit, unser modulares I/O-System vorzukonfektionieren und als Out-of-the-Box-System inklusive der gewünschten Kanalbeschriftung auszuliefern.
Was ist dazu erforderlich?
Stefan Schönegger: Um diese Möglichkeiten vollautomatisiert realisieren zu können, ist es notwendig, vom ERP-System direkt auf den einzelnen Sensor zugreifen zu können. Die herkömmliche Automatisierungspyramide mit ihren strikt getrennten Schichten wird sich auflösen und zu einer Einheit verschmelzen. Ein modernes Steuerungssystem kann dabei zum Beispiel auch Aufgaben eines Scada- oder sogar MES-Systems übernehmen und gleichzeitig den aktuellen Zustand eines Sensorsignals überwachen. Für die Variantenvielfalt ist ein entsprechend modularer Aufbau zwingend erforderlich. Komponenten werden je nach Bedarf angeschlossen bzw. in Form von mechatronischen Einheiten beliebig gekoppelt - während des vollen Produktivbetriebs. Eine entsprechende automatische Änderung der Konfiguration aller involvierten Komponenten ist natürlich Voraussetzung.
Neben der vertikalen Integration im Sinne von Durchgängigkeit und Transparenz, wie Sie sie gerade erläutert haben, sprechen Sie auch von der horizontalen Integration der Disziplinen. Was verstehen Sie darunter?
Stefan Schönegger: Unter der horizontalen Integration verstehen wir die Verschmelzung aller Disziplinen, die für die Entwicklung und Produktion der Produkte notwendig ist. Simulation, Elektrokonstruktion, Mechanikkonstruktion, Automatisierung sowie Qualitätssicherung (Inspektion) müssen nahtlos zusammenspielen. Zum Beispiel müssen Änderungen von der Elektroverkabelung (ECAD) direkt im Automatisierungssystem übernommen werden können. Dies gilt natürlich auch in die andere Richtung bei Änderungen in der Automatisierung.
Könnten Sie konkrete Beispiele anführen?
Stefan Schönegger: B&R und Eplan haben eine perfekte Schnittstelle geschaffen, um die beiden Welten ECAD und Automatisierung ideal zu verbinden. Dafür hat sich der Begriff Round-Trip-Engineering etabliert. Ähnliches gilt für die Kopplung von Vision-Systemen mit dem Steuerungssystem. Vision-Systeme werden häufig zur Produktendkontrolle für die Qualitätssicherung eingesetzt. Der Hersteller möchte nachvollziehen können, welche Produkte mit welcher Seriennummer aus welcher Charge an welchen Kunden geliefert wurden. Dies ist bekannt unter dem Begriff Track-and-Trace. Hierfür ist eine enge Verbindung mit dem Steuerungssystem und dem übergeordneten Produktionsleitsystem Voraussetzung. Mit dem Hersteller von Vision-Komponenten Cognex haben wir auch die Echtzeitsynchronisierung mit Powerlink in das Kamerasystem integriert. Damit können wir auch zeitkritische Vorgänge, zum Beispiel das Aussortieren von mangelhaften Produkten, direkt über die Kamera steuern.
Sie nennen weiter die Stichworte Differenzierung und Effizienz?
Stefan Schönegger: Alle diese Anforderungen dienen einem einzigen Ziel: der Wirtschaftlichkeit bzw. der Profitabilität des Produktionsunternehmens. Eine große Herausforderung ist, sich am Weltmarkt differenzieren zu können. Dies gilt auch für Maschinenbauunternehmen. Bei allem Fokus auf Losgröße 1 und noch individuelleren Lösungen muss es möglich sein, die Produkte effizient zu fertigen. Umrüstzeiten müssen radikal reduziert werden, Stillstandszeiten von Anlagen sind nicht akzeptabel. Wir haben dafür mit unserem Solution-Programm Scalability+ die Basis geschaffen, um diesem Anspruch gerecht zu werden.
Was genau versteckt sich hinter dem Begriff Scalability+?
Stefan Schönegger: Scalability+ ermöglicht neuartige Maschinenkonzepte. Die Basis dafür bildet eine beliebige Kombinierbarkeit des gesamten Hardware-Portfolios mit allen Technologiefunktionen. Zum Beispiel kann eine anspruchsvolle Robotiksteuerung auf einer kosteneffizienten Standardsteuerung realisiert werden, anstatt wie in der Industrie üblich auf spezielle Controller angewiesen und dadurch eingeschränkt zu sein. Zusätzlich hat der Kunde die Möglichkeit, mit eigenen modularen Applikationsbausteinen seine Differenzierung sicherzustellen. Durch die Wiederverwendbarkeit dieser Softwarepakete kann er auch seine Entwicklungsaufwände deutlich reduzieren. Durch die beliebige Auswahl und Skalierbarkeit der Hardware hat der Kunde zudem die Möglichkeit, erst zu einem sehr späten Zeitpunkt in der Entwicklung die finale und ideale Hardware festzulegen.
Bei Industrie 4.0 geht es nicht zuletzt auch um Standardisierung - hier kommt Powerlink zum Tragen?
Stefan Schönegger: Powerlink und openSafety sind die ideale Basis und bieten alle technischen Voraussetzungen, um auch langfristig alle Anforderungen von Industrie 4.0 unterstützen zu können. Beide Kommunikationsstandards sind als Open Source verfügbar, denn tatsächliche Offenheit ist die Basis für die echte Revolution von Industrie 4.0. Eine gute Ergänzung zu diesen beiden Systemen bildet die Kommunikation mittels OPC UA und IO-Link. Diese vier Technologien lassen sich ideal kombinieren und ihre jeweiligen Vorteile ergänzen sich perfekt zu einem harmonischen System.
Stichwort Offenheit - Industrielle Kommunikationsnetzwerke müssen verstärkt mit Fremdsystemen interoperieren. Warum wird das wichtiger?
Stefan Schönegger: Industrielle Kommunikationsnetzwerke müssen eine Interoperabilität mit Fremdsystemen bieten. Nahezu jede Produktion umfasst Maschinen oder Fertigungseinheiten unterschiedlicher Anbieter. Eine effiziente und wirtschaftliche Fertigung bis hinunter zu Losgröße 1 erfordert jedoch zwangsläufig eine Kommunikation über alle Produktionseinheiten hinweg. Alle am Prozess beteiligten Komponenten müssen in der Lage sein, zueinander Daten auszutauschen. Dies darf nicht nur auf einen Hersteller limitiert sein. Eine gut ausgeprägte Kompatibilität mit existierenden Systemen und eine vollständige Offenheit der Technologie sind da von entscheidender Wichtigkeit. Die Offenheit des Standards bedeutet Investitionssicherheit und Freiheit für Anwender und Betreiber.
Schließlich verlangt die Entwicklung von Industrie 4.0 und die Welt des Internets der Dinge, Cloud Computing, etc. eine Dezentralisierung von Automatisierungsprozessen. Was bedeutet das genau?
Stefan Schönegger: Es wird immer mehr Intelligenz in die Komponenten wandern. Dadurch erhöht sich insgesamt das Datenaufkommen. Eine direkte Kommunikation zwischen den Komponenten wird zwangsläufig für bestimmte Prozesse die entscheidende Anforderung sein. Ein zentrales technisches Merkmal von Powerlink ist, dass seine Netzwerk-Teilnehmer via Querverkehr kommunizieren können. Powerlink organisiert die Kommunikation unter den Teilnehmern und erlaubt andererseits den völlig freien Systemausbau ohne Beeinträchtigung der Echtzeit. Starre Topologien würden Probleme bereiten, wenn der Betreiber sein System erweitern möchte.
Ein weiterer Aspekt von Industrie 4.0 in diesem Zusammenhang ist der Arbeitsschutz im Spannungsfeld mit der erforderlichen Flexibilität und Ungehindertheit der Produktionsabläufe, die sich aus den eben besprochenen Entwicklungen ergeben. Eingehauste Maschinen in Sicherheitskäfigen, trennende Schutzgitter, etc. soll es möglichst nicht mehr geben. Was bedeutet das für die Sicherheit in der Produktion?
Stefan Schönegger: Einzelmaschinen in Sicherheitskäfigen einzuhausen, ist nicht zielführend. Die Maschinen und Fertigungszellen sollen in Abhängigkeit des Werkstückes, das gerade gefertigt wird, ihre Konfiguration anpassen können. Dazu werden Maschinenmodule hinzugenommen oder ihre Reihenfolge wird geändert. Feldbusintegrierte Sicherheits-Steuerungssysteme sind eine Voraussetzung für den modularen Maschinenbau. Das vom Feldbustyp unabhängige Sicherheitsprotokoll Opensafety ermöglicht darüber hinaus die sicherheitstechnische Ausstattung von Maschinen oder Modulen, die mitunter über unterschiedliche Protokolle kommunizieren. So ist es mit Opensafety möglich, ganze Produktionslinien inklusive aller dynamisch konfigurierbarer Elemente in einer gemeinsamen sicheren Einheit zusammenzufassen. Darüber hinaus bietet das System Möglichkeiten, auf trennende Schutzgitter zu verzichten - etwa mit der sicher begrenzten Geschwindigkeit am Werkzeugmittelpunkt bei Robotern oder überhaupt von durchgängig sicheren komplexen Kinematiken. Damit kann auf kostenintensive Einhausungen bereits heute komplett verzichtet werden.