Leuze Electronic kooperiert mit Microsoft
Leuze electronic und Microsoft entwickeln gemeinsam eine I4.0-fähige Sensorlösung, die Daten direkt an die Azure Cloud und wieder zurück in den Sensor überträgt. Sie basiert auf de...
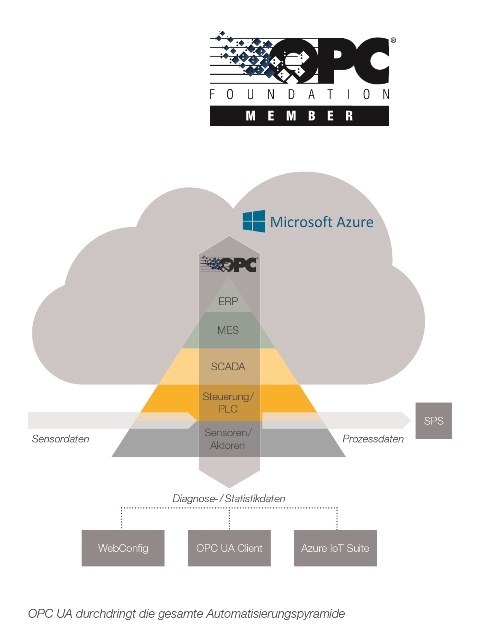
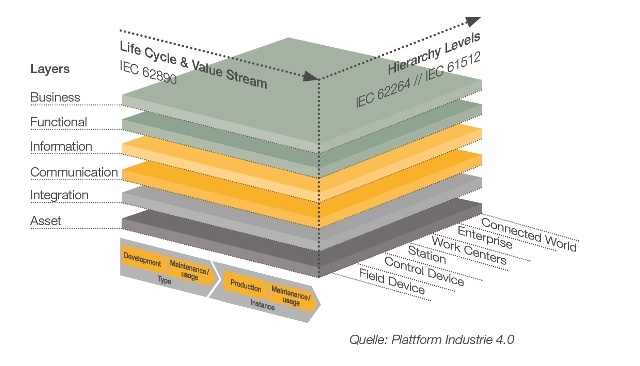
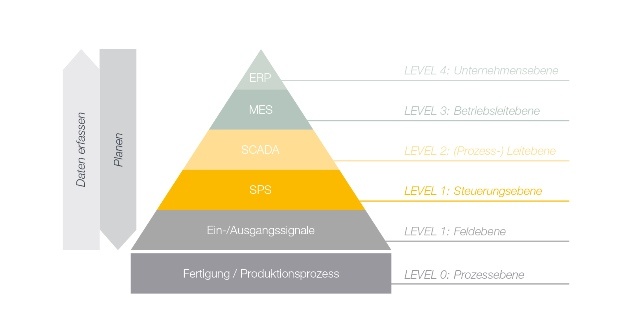
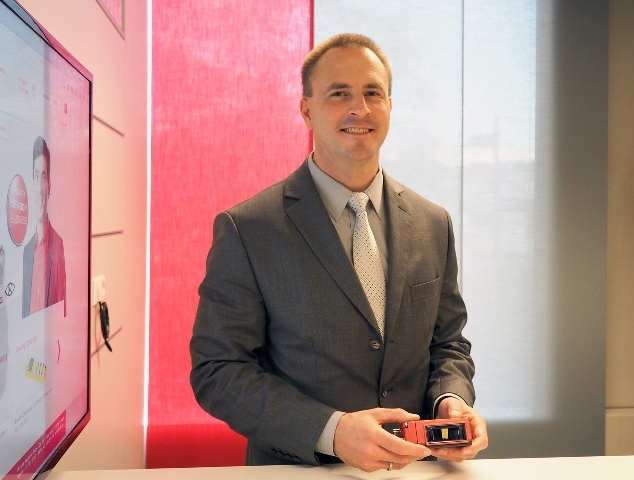
Leuze electronic und Microsoft entwickeln gemeinsam eine I4.0-fähige Sensorlösung, die Daten direkt an die Azure Cloud und wieder zurück in den Sensor überträgt. Sie basiert auf dem Barcodeleser BCL 300i von Leuze. Ein von den Kooperationspartnern vorgelegtes White Paper erläutert die Hintergründe.
Eine intelligente und standardisierte Datenschnittstelle ist die Voraussetzung für eine hohe Datentransparenz und damit Basis für Industrie 4.0. Die Schnittstelle alleine reicht aber nicht aus, um Industrie 4.0-Systeme realisieren zu können. Das Referenzarchitekturmodell RAMI 4.0 der Plattform Industrie 4.0 liefert eine Darstellung für die Industrie.
Im RAMI-Modell werden die Eigenschaften von Industrie 4.0-Komponenten in drei verschiedenen Dimensionen dargestellt: In einer Richtung wird der Produktlebenszyklus beschrieben – hierbei werden Produktdaten wie beispielsweise Produktionsdaten, Datenblätter, Parametrierdaten usw. gesammelt. In der nächsten Dimension wird eine Hierarchie aufgezeichnet. Dabei handelt es sich im Prinzip um die bekannte Automatisierungspyramide, erweitert um die Punkte „Product“ unterhalb der Feldebene und „Connected World“ oberhalb der Unternehmensebene. In der dritten Dimension wird die IT-Repräsentanz beschrieben.
Industrie 4.0-Komponenten müssen sich durch das RAMI-Modell 4.0 beschreiben lassen. Das bedeutet, dass ein Sensor (Field Device) über alle IT-Ebenen kommunizieren können muss, wenn er als Industrie 4.0-Komponente eingesetzt werden soll. Dies kann ein Sensor mit einer klassischen Feldbus-Schnittstelle nicht leisten, da diese Schnittstellen ausschließlich mit der Steuerung kommunizieren, aber keine Daten in die oberen IT-Ebenen abgeben.
OPC UA als Standard
Im Gegensatz zu den klassischen Feldbus-Schnittstellen kann eine Schnittstelle, die um das OPC UA-Kommunikationsmodell erweitert ist, Daten in höhere IT-Ebenen des RAMI-Modells transportieren. OPC steht für „Open Platform Communications“ und ist ein Satz von Standards für die industrielle Kommunikation. Dieser Standard wurde zwischen 1994 und 1996 unter dem Namen „OLE for Process Control“ entwickelt, mit dem Ziel, Prozessdaten von Aktoren und Sensoren unterschiedlicher Hersteller mit SCADA- und HMI-Systemen auszutauschen.
OPC basiert dabei auf den Microsoft-Technologien OLE, COM und DCOM. Das UA in OPC UA steht für „Unified Architecture“ und stellt eine signifikante Weiterentwicklung von OPC dar. Im Gegensatz zu der ursprünglichen OPC-Technologie handelt es sich bei OPC UA um eine plattformübergreifende Implementierung, die damit nicht mehr an Windows-Plattformen gebunden ist. Sie kann unter anderem auch auf Embedded Systemen und damit in Sensoren implementiert werden. Darüber hinaus lässt sich das OPC UA-Kommunikationsmodell neben den klassischen Protokollen wie zum Beispiel Profinet oder Ethercat über alle ethernetbasierenden Feldbus- Schnittstellen betreiben.
OPC UA beinhaltet eine Security-Implementierung, die aus Authentifizierung, Autorisierung, Verschlüsselung und Datenintegrität mit Signaturen besteht. Damit erlaubt OPC UA im Gegensatz zu den üblicherweise im industriellen Umfeld eingesetzten Kommunikationsmethoden eine sichere Kommunikation. Von der Feldebene der Automatisierungspyramide kann OPC UA über zwei unterschiedliche Mechanismen kommunizieren, entweder über eine Client/Server- Kommunikation oder über ein Publisher-Verfahren.
Bei der Client/Server-Kommunikation wird in der Datenquelle, zum Beispiel einem Sensor, ein OPC UA-Server integriert, der Daten an einen Datenabnehmer liefern kann. Beim Publisher-Verfahren wird ein UPC UA Publisher in der Daten-Quelle integriert, welcher dann verschiedenen Datenabnehmern seine Daten zur Verfügung stellen kann. Gibt es im System mehr als eine Datenquelle (Sensor), kann der Datenabnehmer entscheiden, welche Daten er von welchem Publisher beziehen möchte. Somit muss der Abnehmer nicht immer die Daten aller Publisher empfangen. Über dieses Verfahren ist so eine Kommunikation von m-Datenquellen zu n-Daten-Abnehmern möglich. Zum anderen kann sich eine Daten-Cloud interessante Daten direkt von der Datenquelle holen. Auch in der gegengesetzten Richtung – von der Cloud in den Sensor – wird in der Zukunft eine Kommunikation möglich sein. OPC UA kann somit – entsprechend der Forderung an eine Industrie 4.0-kompatible Kommunikation – die Schichten der Automatisierungspyramide quasi „durchtunneln“ und Daten in die höheren Schichten des RAMI-Modells transportieren. Somit wird eine standardisierte Kommunikation von Sensoren und Aktoren unterschiedlicher Hersteller direkt mit einem Cloud-basierten ERP-System möglich. Dank der sicheren Kommunikation ist sogar ein Austausch von Daten zwischen unterschiedlichen Systemen über öffentliche Kanäle denkbar. Da Industrie 4.0 und IIoT für den Austausch von Daten zwischen erfassenden und agierenden Einheiten über alle Systemgrenzen hinweg steht, ist OPC UA ein wichtiger Bestandteil von Industrie 4.0 und mit den oben genannten Eigenschaften aus unserer Sicht einer der wichtigsten Kandidaten für einen zukünftigen Standard in der Machine-to-Machine-Kommunikation (M2M).
Die Microsoft Azure Cloud
Die Datenbereitstellung von Komponenten über die OPC UA-Kommunikation alleine ist aber nicht ausreichend für eine Industrie 4.0-Anwendung. Es werden zusätzliche Mechanismen zur Datenabnahme von der Cloud benötigt. Der Datentransfer vom Sensor in die Cloud wird als Telemetrie bezeichnet. Um die Telemetriedaten ohne zusätzliche Komponenten, wie beispielsweise ein Industrie 4.0-Gateway, zu realisieren, starten Leuze electronic und Microsoft eine Zusammenarbeit, deren erste Ergebnisse beide Unternehmen gemeinsam auf der SPS/IPC/Drives 2016 in Nürnberg präsentiert haben: Sensordaten des Barcodelesers BCL 348i von Leuze electronic werden über das OPC UA-Publish/Subscriber Communication Modell (PSCM) in den Azure IoT Hub der Firma Microsoft übertragen. Vom Barcodeleser werden sowohl Prozess- als auch Metadaten wie Codeart oder die Anzahl Lesungen über das Advanced Message Queuing Protokoll (AMQP) der OPCUA-Schnittstelle an die Microsoft Azure Cloud übertragen. Diese Daten werden dort vom IOT-Hub erfasst, den Azure Cloud Services zur Analyse und Visualisierung bereitgestellt.
Kooperation zwischen Leuze Electronic und Microsoft
Microsoft ist mit der Azure Cloud einer der führenden Cloud-Anbieter. Die Azure Cloud stellt dem Nutzer eine Vielzahl von Cloud-Anwendungen zur Verfügung. Diese Dienste sind hyperscalingfähig und können vom Anwender global abgerufen werden. Aktuell bietet Microsoft für Embedded-Geräte erstmals die Möglichkeit einer Relay/Broker-Kommunikation an, die jetzt im Barcodeleser BCL 348i von Leuze electronic integriert wurde. Mit dieser Kommunikation kann ein Embedded Device aus der Azure Cloud gesteuert werden und wird als Command/ Controll-Funktion bezeichnet.
Am Beispiel des Barcodelesers BCL 348i präsentiert Leuze electronic, wie ein Device von der Cloud, ohne dass ein weiteres Gateway benötigt wird, auf der untersten RAMI- Ebene angesprochen werden kann. Konkret wird gezeigt, wie überall auf der Welt von einem beliebigen Mobil-Device, über die Azure Cloud, das Lesetor eines Barcodelesers von Leuze electronic gesteuert werden kann.
Im Sinne von Big Data ist jedoch ein weiterer Anwendungsfall von weitaus größerer Bedeutung. Die vom IoT-Hub erfassten Sensordaten können von den mächtigen Analysewerkzeugen der Cloud nach vorbestimmten Kriterien analysiert werden und Ereignisse im Industrie 4.0-Gesamtsystem auslösen. Mit dem Eingehen von Kooperationen, anwendungsorientierten Use Cases und Entwicklern von innovativen Industrie 4.0-fähigen Lösungen und Produkten versteht sich Leuze electronic als ein Treiber für Industrie 4.0 und sieht diese als Chance für neue Geschäftsmodelle.
Kommunizieren mit der Cloud
Leuze electronic kooperiert in Sachen Industrie 4.0 mit Microsoft und präsentiert eine erste gemeinsam entwickelte I4.0-fähige Sensorlösung auf Basis des Barcodelesers „BCL 348i“. Dr. Henning Grönzin, Director Research & Development bei Leuze, erläutert die Details.
GIT SICHERHEIT: Herr Dr. Grönzin, Leuze Electronic betrachtet OPC UA als wichtigen Bestandteil von Industrie 4.0, um die Daten von Komponenten bereitzustellen. An welchem Punkt kommt da Microsoft ins Spiel?
Dr. Henning Grönzin: Bei Industrie 4.0 geht es grundsätzlich um Daten und deren Austausch in verschiedene Ebenen und Richtungen. Als Hersteller im Bereich Optosensorik ist Leuze Electronic ein Datenlieferant. Im Kontext von Industrie 4.0 werden Plattformen benötigt, in denen diese Daten aggregiert und analysiert werden. Mit der Azure Cloud stellt Microsoft eine sehr mächtige solche Plattform zur Verfügung. Um die Daten aus den Leuze-Sensoren in die Azure Cloud zu übertragen, wird ein standardisiertes Kommunikationsmodell benötigt. Hier bietet sich OPC UA derzeit als der, aus unserer Sicht, vielversprechendste Kandidat an.
Was bringt die „Azure Cloud“ von Microsoft?
Dr. Henning Grönzin: Microsoft ist mit der Azure Cloud einer der führenden Cloud-Anbieter. Die Azure Cloud stellt dem Nutzer eine Vielzahl von Cloud-Anwendungen und Diensten zur Datenbearbeitung und -analyse zur Verfügung. Sie ist Datenempfänger für nicht- steuerungsbezogene Daten und ermöglicht eine globale Verfügbarkeit derselben.
Wie ist die Anbindung des Barcodelesers realisiert?
Dr. Henning Grönzin: Prozess- und Metadaten unseres Barcodelesers BCL 348i werden über das OPC UA-Publish/Subscriber Communication Modell (PSCM) in den Azure IoT Hub der Firma Microsoft übertragen. Die Übertragung an die Azure Cloud erfolgt über das Advanced Message Queuing Protokoll (AMQP) der OPC UA-Schnittstelle. Die Daten werden dort vom IOT-Hub erfasst und den Azure Cloud Services zur Analyse und Visualisierung bereitgestellt. Für erweiterte Steuerungsaufgaben mit intensivem bidirektionalen Datenaustausch steht mit der Reverse IoT Proxy Lösung ein weiterer Mechanismus zur Verfügung.
Und wie sieht die Kommunikation zwischen Barcodeleser und Cloud aus?
Dr. Henning Grönzin: Der Fokus liegt auf dem Monitoring von Sensordaten. Vom Barcodeleser werden Daten in die Cloud übergeben. Hierbei handelt es sich in erste Linie um Gerätedaten, wie beispielsweise Geräteidentifikation und -status, Statistikdaten sowie Daten, die nicht steuerungsrelevant sind. Zusätzlich spielt die die Kommunikation von Ereignissen und steuernde Funktionen von der Cloud in den Barcodeleser eine Rolle, die via Command/Control-Erweiterungen erfolgt.
Was konnten Besucher auf dem Messestand der SPS konkret sehen?
Dr. Henning Grönzin: Konkret sichtbar für den Messebesucher waren Geräteinformationen, Statusdaten vom Gerät sowie Lesestatistiken und -ergebnisse. Darüber hinaus wurde gezeigt, wie ein Sensor über ein global verfügbares User Interface gesteuert werden kann, indem der Benutzer das Lesetor eines Barcodelesers öffnen und schließen kann – ebenso ein Anwendungsfall, der die Analysefähigkeit der Cloud nutzt, abgegebene Sensordaten bewertet und die Ergebnisse global verfügbar macht.
Meist gelesen
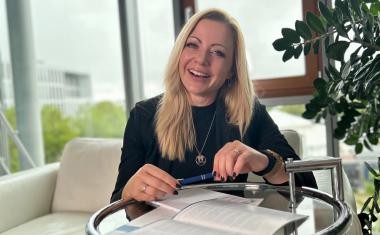
Schutz für exponierte Personen und wohlhabende Familien
Personenschutz für Vermögende: Christina Schwung über Risiken, Schutzkonzepte und digitale Bedrohungen
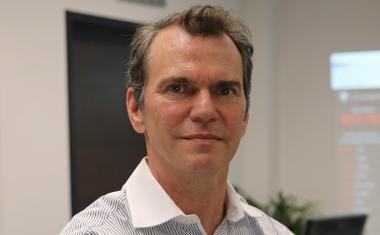
Globale Sicherheitsstrategien der DHL Group
Frank Ewald von der DHL Group über globale Sicherheitsstrategien und die Herausforderungen der Logistikbranche im Interview
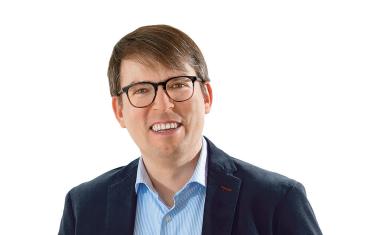
VDMA-Einheitsblatt 24994: Erster einheitlicher Prüfstandard für die Zertifizierung von Lager-/Ladeschränken für Lithium-Ionen-Akkus
Mit dem VDMA-Einheitsblatt 24994 gibt es seit August vergangenen Jahres erstmals eine Grundlage für einen einheitlichen Prüfstandard im Bereich von Lager- bzw. Ladeschränken und -einrichtungen für Lithium-Ionen-Akkus.
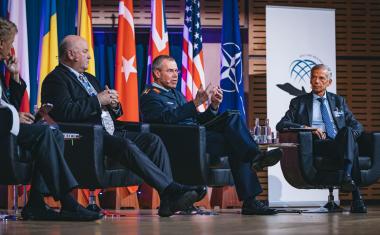
Euro Defence Expo und NATO JAPCC parallel zur Security Essen 2026
Vom 22. bis 25. September 2026 wird die Euro Defence Expo (Eudex) ihre Premiere in der Messe Essen begehen – gleichzeitig mit der jährlichen Konferenz des NATO Joint Air Power Competence Centre sowie der Security Essen.
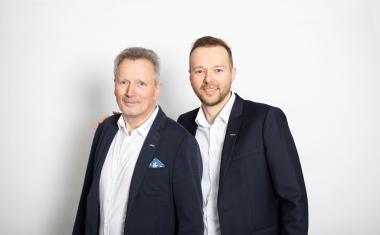
Partner des Fachhandels – Ein Gespräch mit Jürgen Hövelmann von EPS-Vertrieb
Sicherheitslösungen mit Tradition & Innovation: EPS-Vertrieb stellt das Ajax Fire-System vor