Maschinen- und Anlagensicherheit: Gefahrendokumetation durch externe Dienstleister
Maschinen- und Anlagensicherheit: Gefahrendokumetation durch externe Dienstleister. Technik einzusetzen bedeutet immer auch ein Sicherheitsrisiko. Ausfälle und Fehlfunktionen von M...
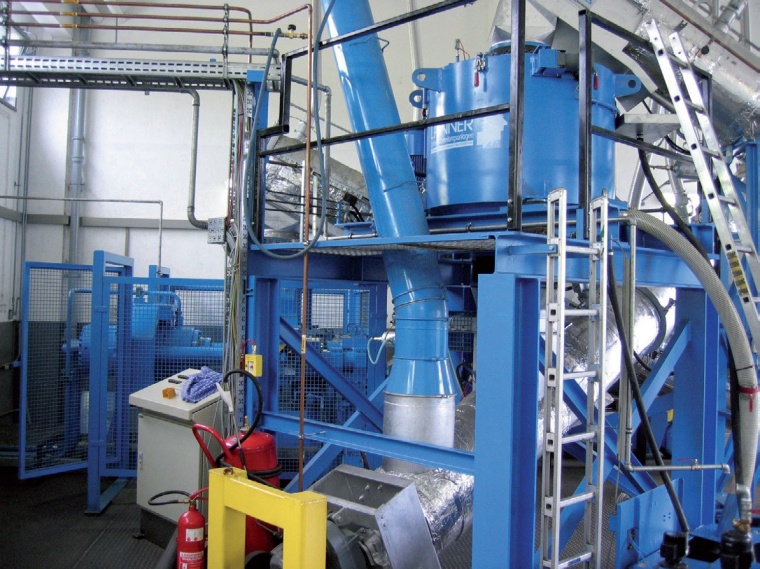
Maschinen- und Anlagensicherheit: Gefahrendokumetation durch externe Dienstleister. Technik einzusetzen bedeutet immer auch ein Sicherheitsrisiko. Ausfälle und Fehlfunktionen von Maschinen und Anlagen können zu Risiken für Personen, Umwelt oder Sachwerten führen. Maschinensicherheit ist deshalb ein zentrales Thema im betrieblichen Arbeitsschutz und wird durch die zunehmende Automatisierung der Produktionsprozesse immer wichtiger. Wie die Erfahrung zeigt, sind jedoch die heute geltenden, rechtlich verbindlichen Forderungen, Normen und Richtlinien in der Praxis leider oft schwer umzusetzen.
Bereits Ende des 19. Jahrhunderts wurden in verschiedenen Industriebereichen Verfahren entwickelt, um die von Maschinen und Anlagen ausgehenden Gefahren und Risiken zu analysieren und dadurch bereits im Vorfeld weitestgehend zu vermeiden.
In der Folgezeit wurden die rechtlichen Forderungen im Zusammenhang mit Vorsorge- und Vorbeugemaßnahmen ständig weiter verschärft und heute muss jeder Hersteller einer Maschine oder Produktionsanlage eine Gefahrenanalyse gemäß der EG-Maschinenrichtlinie durchführen und dokumentieren. Die Gefahrenanalyse ist damit Voraussetzung für die CE-Kennzeichnung und das Inverkehrbringen einer Maschine oder Anlage.
Man muss sich folglich frühzeitig in der Entwicklung oder Konzeption darum kümmern und dabei natürlich auch die geforderte Dokumentation berücksichtigen. Genau hier fangen aber für viele die praktischen Probleme an.
Unzureichende Dokumentation – fatale Folgen
Maschinen- oder Anlagenkonstrukteure haben selten Zeit, eine gründliche und praxisgerechte Gefahrenanalyse einschließlich der notwendigen technischen Dokumentation zusätzlich zu ihren Aufgaben zu erstellen. Doch welche Abteilung im Betrieb sollte sonst dafür zuständig und in der Lage sein, die entsprechenden Arbeiten zu übernehmen, zumal standardisierte, einfach einführ- und anwendbare Vorgehensweisen nicht definiert sind?
Die Folgen dieser Situation können fatal sein; denn gegen solche "Verfehlungen" gibt es keinen Versicherungsschutz. Mancher Anlagenbetreiber kam schon nach einem kleineren Unfall ins Schwitzen, wenn sich zeigt, dass die vorhandenen Dokumentationen zur Gefahrenanalyse nicht komplett und richtlinienkonform sind.
Um solche Fehler zu vermeiden und die eigenen Abteilungen von den aufwändigen und gerade in der Anfangsphase oft kompliziert erscheinenden Verfahren zu entlasten, bietet sich deshalb "Outsourcing" an, d.h. die Beauftragung eines externen Dienstleisters. Wie das in der Praxis aussehen kann, zeigt die Gefahrenanalyse für die Magnesiumrecycling-Anlage der Firma Magrec in Sonneberg (Abb. 1). Es geht um das Handling explosiver Materialien.
Praxisbeispiel: Gefahrenanalyse für eine Magnesiumrecycling-Anlage
Späne aus Magnesium oder Magnesiumlegierungen fallen in der metallverarbeitenden Industrie als Abfälle an. In der Magnesiumrecycling-Anlage in Sonneberg wird zunächst das an ihnen haftende Öl oder die ölhaltige Emulsion abgeschleudert. Anschließend werden die Späne bei bestimmten Temperaturen und unter hohem Druck so aufbereitet, dass die entstandenen Briketts wieder zur Herstellung von Magnesiumlegierungen eingeschmolzen werden können.
Das klingt einfach, ist in der Praxis jedoch recht kompliziert und vor allem nicht ungefährlich. Bei falschem Handling bzw. Fehlern im Produktionsablauf wird Magnesium zur Brandbombe. Magnesiumspäne sind leicht entzündlich; Magnesiumstäube im Gemisch mit Luft sind explosionsfähig.
Einen wesentlichen Teil der Gefahrenanalyse machte bei dieser Produktionsanlage daher die Beurteilung der Brand- und Explosionsgefahr aus. Wichtige Grundlagen liefert BGR 104 "Regeln für das Vermeiden der Gefahren durch explosionsfähige Atmosphäre" und BGR 204 "Umgang mit Magnesium" sowie der "Leitfaden für einen sicheren Umgang mit Aluminium und Magnesium".
Ausgehend von den gefährlichen Stoffen Magnesium, öligem Kühlschmiermittel und Wasserstoff, der durch die Reaktion der Späne mit eventuell anhaftendem Wasser entsteht, war zudem eine Gefährdungsbeurteilung der Lagerhalle und der Maschinen in der Produktionsanlage notwendig.
Explosionsschutzbericht im Rahmen der Gefahrenanalyse
Die Palette reicht von einer detaillierten Beschreibung der Anlage und die Identifizierung möglicher Gefährdungen und die anzuwendenden Normen und Richtlinien, über die Risikoeinstufung und die Maßnahmenplanung bis hin zu der Rahmen- und Detailgefahrenanalyse mit Checkliste sowie einer umfangreichen Prüfliste für die Maschinen und die elektrische Ausrüstung.
Mit der daraus resultierenden übersichtlich gegliederten Nachweisdokumentation einschließlich des für diese Anlagen notwendigen Explosionsschutzdokuments mit der detaillierten Beschreibung des Gefahrenpotentials und dem Maßnahmenkatalog zu dessen Vermeidung ist der Anlagenbetreiber heute auf der sicheren Seite. Alle rechtlich verbindlichen Forderungen wurden nicht nur vorbildlich in der Praxis umgesetzt, sondern sind auch jederzeit nachvollziehbar dokumentiert.
Outsourcing – Entlastung für den Hersteller
Dabei wird deutlich, wie komplex die Thematik "Gefahrenanalyse" bereits bei einer einzigen Maschine sein kann. Wer die entsprechenden Arbeiten nicht komplett auslagern will, sollte deshalb zumindest fachlichen Rat einholen oder entsprechende Schulungsangebote nutzen.
Denn auch auf dem Gebiet der Gefahrenanalyse gilt der Grundsatz: „Unkenntnis schützt vor Strafe nicht“. Die Sicherheitsingenieure der Firma beta Sensorik verfügen über langjährige Praxiserfahrung auf diesem Gebiet. Sie bieten neben der sicherheitstechnischen Beratung auch die Durchführung und lückenlose Dokumentation von CE-konformen Gefahrenanalysen bis hin zur unterschriftsfertigen Konformitätserklärung an.
KONTAKT
Dipl.-Ing. Marco Neidert
beta Sensorik GmbH, Küps
Tel.: 09264/1004
Fax: 09264/8393
briefkasten@betasensorik.de
www.betasensorik.de