Schlanke MRK-Lösung bei Continental
Continental gehört zu den weltweit führenden Automobilzulieferern. Die zunehmende Modell- und Variantenvielfalt an Fahrzeugmodellen und Derivaten bei kürzeren Produktlebenszyklen i...
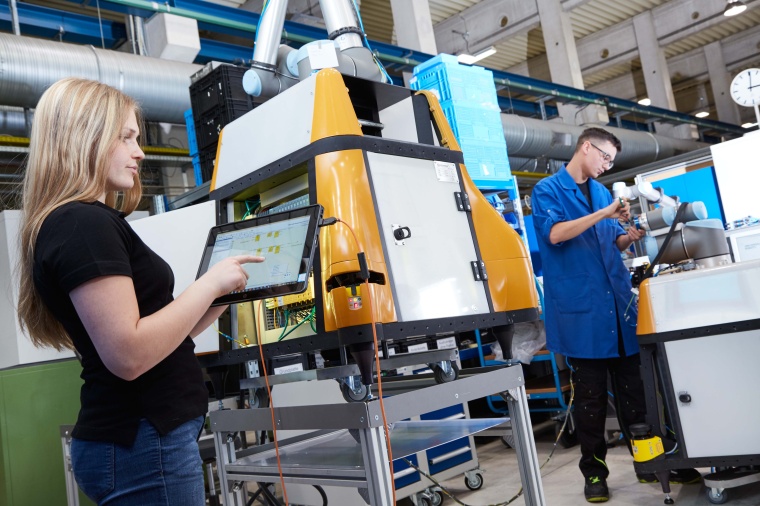
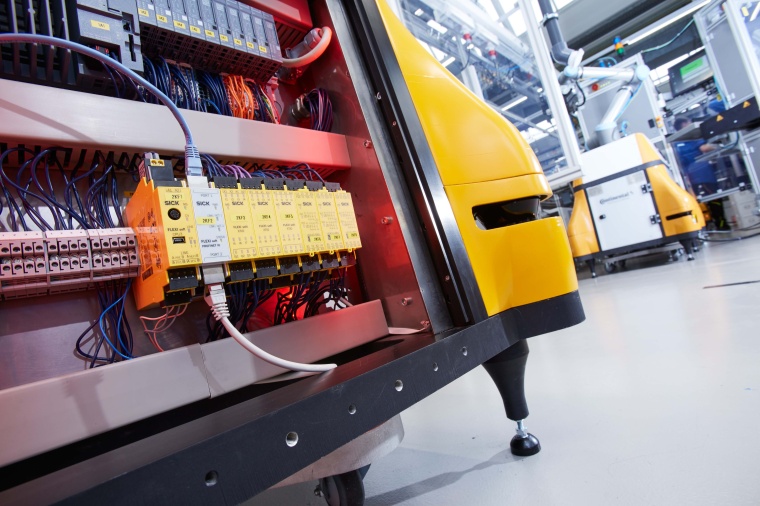
Continental gehört zu den weltweit führenden Automobilzulieferern. Die zunehmende Modell- und Variantenvielfalt an Fahrzeugmodellen und Derivaten bei kürzeren Produktlebenszyklen in der Automobilindustrie erhöht auch die Dynamik bei den Zulieferern. In starr verkettete Fertigungslinien wirken sich Veränderungen und Störungen an einzelnen Stationen auf die Ausbringung der gesamten Linie gravierend aus. Je größer die Störungen ausfallen, desto schwieriger wird eine Kompensation.
Im Werk Babenhausen gehen rund um die Uhr alle 15 Sekunden High-Tech-Komponenten für Auto-Cockpits vom Band. Da ist wenig Luft nach oben, um Stillstandszeiten aufzuholen. Deshalb ersetzt Continental derzeit starre Prüf- und Bestückungslinien durch flexible redundante kollaborative Prüflinien: Die Cobots Claus und Clara bestücken die Prüfautomaten, und zwar dort, wo sie benötigt werden. Beschäftigte gehen ihnen, wenn nötig, sozusagen zur Hand. Für die Sicherheit im kollaborativen Miteinander sorgt eine Safety-Lösung von Sick bestehend aus Sicherheits-Laserscannern S300, Sicherheitsschaltern TR4 und Software-programmierbaren Sicherheitssteuerungen Flexi Soft.
In der komplett neu aufgebauten Prüflinie gibt es drei Prüfstände, die mit Robotern (Cobots) bestückt werden. Der Cobot nimmt sich ein Teil von einem Band, legt das in den Prüfautomaten ein, nimmt sich das geprüfte Gerät wieder mit und legt das auf ein nächstes Band auf.
Sicherheit macht Mensch-Roboter-Kollaboration effizient
„Claus (Clever automatisiertes universelles Roboter-System) und Clara (Clever automatisierte Roboter Applikation) sind halbmobile Leichtbauroboter, die stationär arbeiten, aber mobil einsetzbar sind“, beschreibt Heiko Liebisch, Industrial Engineering, Robotics, Continental Automotive GmbH, die Cobots und ihre Vorteile. „Mit diesem Konzept ist es möglich, den Roboter auszuheben und für eine andere Schicht an einen anderen Platz zu fahren. Somit hat man die Möglichkeit, an zwei Anlagen mit denselben Robotern zu arbeiten. In der Frühschicht an der einen und in der Spät- oder Nachtschicht an der anderen Anlage.“
Mittels mechanischer Indexierung kann der Cobot jederzeit wieder optimal zum Prüfplatz positioniert werden, hier verifiziert ein Transponder-Sicherheitsschalter TR4 Direct Unique-Code Sensor, den TR4 Direct Unique-Code-Betätiger an Claus oder Clara.
„Alles, was zum Thema Sicherheit in dem ganzen System steckt, wird über die Software-programmierbare Sicherheitssteuerung Flexi Soft gesteuert. D.h., die Flexi Soft schaut nach, ob der codierte Sicherheitsschalter da ist. Wenn nicht, dann passiert gar nichts. Dann löst sie eine Fehlermeldung aus. Wenn der Schalter verifiziert wird, laden die Sicherheits-Laserscanner (S300 Advanced) die Feldsätze, die passend zu dem Arbeitsplatz hinterlegt sind und geben dem Cobot überhaupt erstmal die Freigabe, sein Programm zu laden und starten zu können“, beschreibt Heiko Liebisch die Initialisierung. „Wir haben die Möglichkeit mehrere codierte Schalter vorne dran zu schrauben. So können wir den Cobot für mehrere Arbeitsplätze einrichten.“
Die neue Linie bietet die Möglichkeit, ausgeschleuste Prüfteile wieder als Rückläufer in die laufende Anlage zu bringen. Hierfür geht ein Bediener im laufenden Betrieb zur Prüfanlage bzw. zum Cobot, legt das Prüfteil irgendwohin, wo gerade Platz ist, läuft wieder raus und der Cobot weiß selbstständig, da liegt was, das muss ich noch prüfen und macht ganz normal weiter.
Die Sicherheits-Laserscanner, die diagonal angebracht für die Rundum-Überwachung sorgen, zeigen frontseitig per Leuchtmelder in Ampelfarben die Schutzfeldzonen bzw. deren Verletzung an. Damit Bediener dies quasi bereits im Augenwinkel wahrnehmen können, leuchtet der ganze Korpus unter dem Cobotarm entsprechend der Signalampel-Automatik. Im kollaborativen Modus läuft Claus gelb an und reduziert die Geschwindigkeit. Im roten Modus bleibt er komplett stehen. Verlässt der Bediener das rote Schutzfeld, läuft das System und somit Claus automatisch wieder an. Der Bediener muss nicht quittieren.
Am Anfang steht immer die Risikobeurteilung – auch bei Cobots
Auch wenn Claus und Clara sich relativ langsam bewegen, generell kann ein Roboterarm einem Bediener lebensbedrohlich nah kommen. „Man muss immer das Gesamtkonzept beurteilen; deswegen haben wir die Greifer, die wir vorne einsetzen, lasergesintert – ohne spitze Kanten, alles verrundet.“
Keine Mensch-Roboter-Kollaboration gleicht der anderen – daher ist eine individuelle Risikobeurteilung der MRK-Applikation selbst dann erforderlich, wenn der eingesetzte Roboter speziell für die Interaktion mit dem Menschen entwickelt wurde – ein solcher Cobot also schon von der grundsätzlichen Auslegung her eine Vielzahl von Merkmalen einer inhärent sicheren Konstruktion aufweist. Gleichzeitig muss auch der Kollaborationsraum grundlegende Anforderungen erfüllen, z. B. hinsichtlich von Mindestabständen zu angrenzenden begehbaren Bereichen mit Quetsch- oder Einklemmgefahren. Normative Grundlage für die funktionale Sicherheit von MRK-Anwendungen sind zum einen generelle Normen wie die IEC 61508, die IEC 62061 und die ISO 13849-1/-2. Darüber hinaus sind die ISO 10218-1/-2 zur Sicherheit von Industrierobotern und speziell die ISO TS 15066 über Roboter für den Kollaborationsbetrieb zu berücksichtigen.
Das Team um Heiko Liebisch hat sich bzgl. der Auslegung, Richtlinien, gesetzlichen Vorgaben und Normen für Kollaborative Robotik von Sick beraten und schulen lassen. „Wir sind ganz glücklich mit dem System, wie es draußen läuft“, kommentiert Heiko Liebisch das Ergebnis. „In der Praxis zeigen sich hier und da noch Optimierungsmöglichkeiten, die wir mit Sick als Partner für die Gesamtlösung weiter entwickeln werden.“
Funktionale Sicherheit bei der Mensch-Roboter-Kollaboration (MRK)
Hoher Automatisierungsgrad versus flexible Fertigungsabläufe: Wenn Mensch und Maschine jetzt noch enger und dennoch sicher zusammenarbeiten, ist die funktionale Sicherheit in modernen Fertigungssystemen ein Schritt auf dem Weg zu mehr Flexibilität. Hierzu sind nicht nur ein umfassendes Verständnis der Roboteranwendungen, sondern auch Fachwissen bei der Risikobewertung und das entsprechende Portfolio an Sicherheitslösungen notwendig.
Bei bestimmten Anwendungen müssen der Mensch und der bewegte Roboter eng miteinander interagieren. In diesen sogenannten kollaborativen Szenarien stellen Kraft, Geschwindigkeit, Bewegungsbahnen des Roboters und das Werkstück inklusive Werkstückträger Gefahren für den Werker dar. Diese Gefahren müssen entweder durch die Nutzung inhärenter Schutzmaßnahmen oder/und durch die Anwendung zusätzlicher Maßnahmen zur Risikominderung beschränkt werden. Die Auswahl und die Auslegung der technischen Schutzeinrichtungen können sich sehr komplex gestalten.
Ein Beispiel für eine Anwendung, wie die Vernetzbarkeit mehrerer Sicherheits-Laserscanner die Lösung der Applikation erleichtert, ist die lückenlose 360°-Rundum-Absicherung von Robotern oder AGVs und AGCs mit S300 Mini, S300, S3000 oder dem neuen microScan3 Core im Verbund mit der Sicherheitssteuerung Flexi Soft von Sick. Durch diese Lösung ist die Sicherheit in alle Bewegungsrichtungen gewährleistet. Es handelt sich hierbei um eine integrationsfreundliche, hoch verfügbare und wirtschaftliche Komplettlösung aus einer Hand, d. h. ohne applikationstechnische Schnittstellenrisiken. Die Sick-spezifische EFI-Schnittstelle (Enhanced Function Interface) erlaubt eine direkte sicherheitsgerichtete Kommunikation der Geräte untereinander. Die Nutzung dieser Schnittstelle minimiert den sonst erforderlichen, hohen Verkabelungsaufwand für den Anwender – und damit gleichzeitig auch das Risiko von Verdrahtungsfehlern insbesondere in der Inbetriebnahmephase. Durch die zentrale Integration der Flexi Soft im Fahrzeug oder Roboterkorpus ist neben der einfachen Konfiguration auch eine verbesserte Diagnose des Laserscanner-Gesamtsystems von einer Stelle aus möglich. Dies spart nicht nur Zeit während der Inbetriebnahme, sondern optimiert die Wartung und Instandhaltung.
Erfolgreiche Pilotlinie seit Anfang 2017
Heiko Liebisch und sein Kollege Dejan Pfaff haben die neue 4.0-Prüflinie der Continental Automotive GmbH in Babenhausen geplant und die Cobots konstruiert. Sie sind sozusagen die Väter von Claus und Clara, die bald Geschwister in Gestalt von Cora und Kurt bekommen werden. Die erfolgreiche Umstellung macht nämlich Schule bei Continental. Der Einsatz weiterer Cobots ist geplant. Apropos „Schule“, gebaut werden die Cläuse und Claras von Auszubildenden der Continental Automotive GmbH. Mechaniker bauen das Grundgestell, Mechatroniker den Rest. Eine tolle Sache für die Auszubildenden. Wenn sie später mal in einer solchen Linie arbeiten, können sie mit Stolz sagen, das habe ich gebaut.
Business Partner
Sick AGErwin-Sick-Str. 1
79183 Waldkirch
Deutschland
Meist gelesen
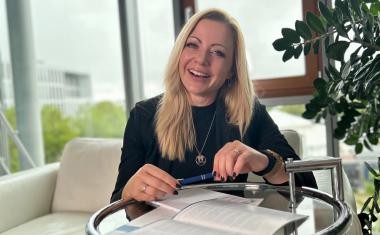
Schutz für exponierte Personen und wohlhabende Familien
Personenschutz für Vermögende: Christina Schwung über Risiken, Schutzkonzepte und digitale Bedrohungen
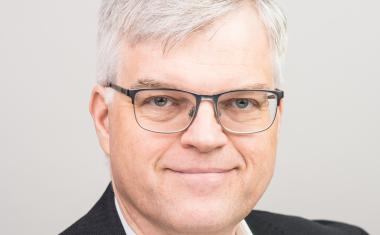
Maschinensicherheit im Kontext von KI und Security – Cyber Resilience Act: Neue Anforderungen für Maschinenbauer
Cyber Resilience Act & Maschinenverordnung: Neue Sicherheitsanforderungen für Maschinenbauer in vernetzten Industrieanlagen
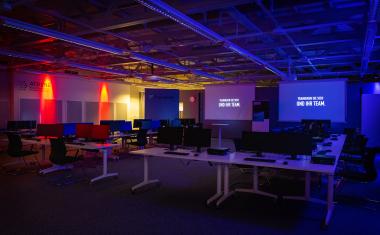
Risikovorsorge durch Cybertrainings – realitätsnah auf der "Cyber Range"
Wird ein Unternehmen Opfer eines Cyberangriffs, dann haben sich Angreifer in der Regel über längere Zeit in mehreren Schritten zu ihrem Ziel vorgearbeitet
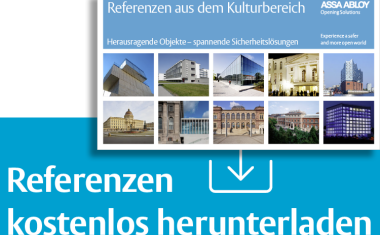
Zutritt steuern, Werte schützen – Schließtechnik für Kulturstätten
Öffentlich zugängliche Kulturinstitutionen sind mit unschätzbaren materiellen und immateriellen Werten ausgestattet.
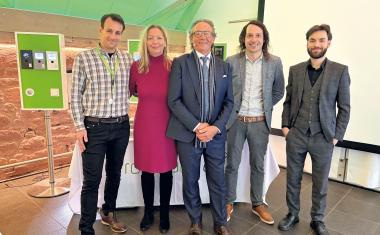
Frogblue International Partner Conference 2025: Innovationen und Zukunftsvisionen
Die Veranstaltung bot eine Plattform für den Austausch von Innovationen, Strategien und Zukunftsvisionen im Bereich der Gebäudeautomation und Zutrittskontrolle bis hin zu Einblicken in Kameratechnik.