Fakten-Check: Warum gibt es ein IT/OT-Sicherheitsproblem?
Dr. Gunther Kegel, Vorstandsvorsitzender der Pepperl+Fuchs SE sowie Präsident des ZVEI, im Interview über Herausforderungen und Sicherheitsrisiken der Anbindung Operativer Technologien (OT) an Informationstechnologien (IT).
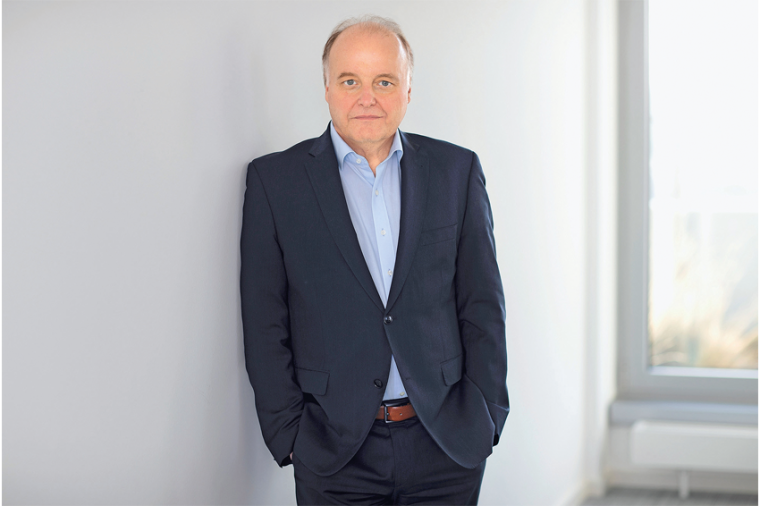
Die Vernetzung von Maschinen und Anlagen gilt als grundlegende Voraussetzung für die Realisierung des Zukunftsprojekts Industrie 4.0. Durch die Anbindung Operativer Technologien (OT) an die Informationstechnologien (IT) ergeben sich jedoch eine ganze Reihe neuer Herausforderungen und Sicherheitsrisiken.
Zu einem großen Teil geht es dabei um die Abwehr und um das Vorbeugen von möglichen Cyberattacken auf die Operative Technologie, weshalb in diesem Zusammenhang von „Industrial Security“ gesprochen wird. Die potenziellen Schäden eines solchen Angriffs können für ein Unternehmen von existenzieller Natur sein. Wie groß die Gefahr von Cyberattacken und deren Folgen von Seiten der Unternehmen weltweit selbst eingeschätzt wird, belegt das Allianz Risk Barometer 2022. Demnach bewerten die Befragten „Cyber Incidents“ mit 44 % als größte Gefahr, noch vor der Unterbrechung des Geschäftsbetriebs etwa durch Lieferkettenunterbrechungen.
Trotz dieser Einschätzung schreitet die Vernetzung von OT und IT weiterhin voran – und wird sogar auf allen Ebenen forciert. Doch wieso gehen betroffene Unternehmen dieses enorme Risiko ein – und warum ist eine Vernetzung von OT und IT abseits geläufiger Schlagworte überhaupt sinnvoll? GIT SICHERHEIT macht den Fakten-Check mit Dr. Gunther Kegel, Vorsitzender des Vorstands der Pepperl+Fuchs SE und Präsident des ZVEI.
GIT SICHERHEIT: Herr Dr. Kegel, seit einigen Jahren wird nun bereits die Vernetzung von Maschinen und Anlagen als unabdingbare Voraussetzung für die Wettbewerbsfähigkeit industrieller Produktions- und Logistikprozesse betrachtet. Hand aufs Herz: Worin genau bestehen nun abseits der mantraartig vorgetragenen Buzzwords wie „Smart Factory“ oder „AI Manufacturing“ denn tatsächliche die Vorteile bei der Vernetzung von Maschinen und Anlagen – und nennen Sie unseren Leserinnen und Lesern einmal ein konkretes Beispiel?
Dr. Gunther Kegel: Als auf der Hannover 2013 der damaligen Kanzlerin der „acatech“- Abschlussbericht übergeben wurde und darin der Begriff Industrie 4.0 geprägt wurde, hatten wir alle noch wenig konkrete Vorstellungen, wie die horizontale Vernetzung des „Shopfloors“ und die vertikale Vernetzung mit dem „Officefloor“ aussehen würde. Auch die Anwendungen und der jeweilige Nutzen waren noch nicht klar bezifferbar. Die Hoffnung lag eben auch stark in ganz neuen, disruptiven Geschäftsmodellen, die auf einem digitalisierten „Shopfloor“ überhaupt erst entstehen können. Mit einer Vielzahl von „Leuchtturm-Projekten“ haben wir seitdem versucht, Anwendungen zu finden, deren Digitalisierung neue Geschäftschancen oder verbesserte bestehende (Geschäfts-)Prozesse nachweisbar hervorbringen. Das war viel schwerer als zunächst angenommen!
Wir wissen heute, dass die Digitalisierung des Shopfloors mit proprietären Lösungen zwar Effizienz fördern kann, in der Regel aber kein neues, digitales Geschäftsmodell hervorbringt, weil die Skalierung an den vielen proprietären Ansätzen scheitert. Es wurde schnell klar, dass für die Digitalisierung des Shopfloors zunächst ein genormtes, verbindliches Datenformat entwickelt werden muss, das die Daten selbst, aber auch die auf den Content bezogenen Meta-Daten vollständig beschreibt.
Dieses Datenmodell heißt „Verwaltungsschale“ bzw. „Asset Administration Shell“ und wurde auf der Plattform Industrie 4.0 vordefiniert. Heute wird dieses Datenmodell in einer Vielzahl von Teilmodellen, die alle individuelle Anwendungen unterstützen, in der von ZVEI und VDMA neu gegründeten „Industrial Digital Twin Association“ weiterentwickelt und in den entsprechenden Gremien genormt. Wenn alle in einer Anlage oder Maschine verbauten Komponenten durch das jeweilige Teilmodell der Verwaltungsschale beschrieben sind, können (neue) digitale Applikationen auf der Ebene des „Officefloors“ ohne großen Aufwand und mit der Möglichkeit schneller Skalierung entstehen. Erst so wird ein industrielles, digitales Ökosystem entstehen. Der „Shopfloor“ wird zum „Industrial Metaverse“.
Die einfachste praktische Anwendung ist hier das „digitale Typenschild“. Anstatt jedes Produkt mit einem schwer lesbaren Typenschild zu versehen und jeweils Sicherheitsdatenblätter und rudimentäre Betriebsanleitungen in Papierform beizufügen, wird zukünftig jedes Produkt mit einem individuellen QR-Code versehen. Der Anwender kann den QR-Code mit einem mobilen Endgerät lesen und bekommt aus dem „Product-Lifecycle-Management-System“ des Herstellers alle für das „Teilmodell digitales Typenschild“ erforderlichen Daten z. B. in Form einer dynamischen Web-Seite, die die standardisierten Daten für alle Hersteller in gleicher Form darstellt. Der Anwender kann so alle produktrelevanten Daten komfortabel einsehen und der Hersteller spart das Beilegen von Papier und zumeist auch noch kleiner Plastikbeutel. Allein für unser Unternehmen Pepperl+Fuchs wären das 20 Mio. Seiten Papier und 10 Mio. Plastikbeutel. Beides verursacht je 100 t CO2 im Jahr. Dabei wäre der Komfort für den Anwender sogar deutlich gesteigert.
Den von Ihnen genannten Vorteilen stehen die unabwägbaren Risiken entgegen, die eine Verschmelzung von IT und OT mit sich bringen. Einmal ans Netz gebracht, wird ein zuvor virtuell unerreichbarer Komplex externen Zugriffen zugänglich gemacht. Ein Angreifer muss nur einen einzigen Schwachpunkt in der bestehenden Architektur finden, um verheerende Schäden anzurichten.
Dr. Gunther Kegel: Die Anwender sind sich der Gefahr sehr bewusst, schließlich ist jeder schon Opfer von Cyber-Attacken auf dem „Officefloor“ geworden. Daraus haben sich eine Vielzahl möglicher Strategien entwickelt. Viele Firmen werden z. B. ihren „Shopfloor“ digitalisieren und so Effizienz steigern, Transparenz erhöhen und digitale Technologien z. B. im Bereich von „Condition based Maintenance“ oder „Predictive Maintenace“. Eine Verbindung mit dem „Officefloor“ oder direkt mit dem Internet wird zunächst aber untersagt. In einem weiteren Schritt geschieht die Kopplung dann über sichere, bewährte „Edge-Technologien“, die sicherstellen müssen, dass keine unberechtigten Zugriffe auf den „Shopfloor“ ausgeführt werden.
Wie gesagt, man kann die Digitalisierung einschränken, Zugänge blockieren und Schreibrechte einschränken, aber wenn man ein industrielles, digitales Ökosystem aufbauen will, in dem neue, disruptive Geschäftsmodelle entstehen können, kommt man um eine kontrollierte Öffnung nicht herum. Wir schauen doch alle neidvoll auf die amerikanischen „Hyper-Scaler“ und die unfassbare Wirtschaftskraft, die diese wenigen Unternehmen entwickelt haben. Amazon allein investiert jährlich deutlich mehr Geld in Forschung und Entwicklung als die gesamte Elektro- und Digitalindustrie in Deutschland. Wenn wir ähnliche Erfolgsgeschichten wollen, werden wir auch Risiken eingehen müssen.
Die OT hinkt im Bereich Cybersicherheit der IT um viele Jahre hinterher. Hinzu kommt, dass die „Dienstzeit“ operativer Technik häufig wesentlich länger ist als die der IT. Was wären zentrale Schritte für ein Unternehmen, um die bestehende OT vor Cyberattacken zu schützen?
Dr. Gunther Kegel: Die bestehenden, vor Jahren installierten Systeme so mit den Techniken des Internets zu verknüpfen, ist zunächst einmal wenig sinnvoll. In der chemischen Industrie werden heute noch immer weit mehr als 90 % der Signale von Prozesssensoren (z. B. Druck, Füllstand, Durchfluss und Temperatur) über die analoge 4…20 mA Schnittstelle mit überlagertem, digitalem „HART“-Signal übertragen. Diese Systeme sind auf Grund der sehr spezifischen Protokolle und Medien und den minimalistischen Verbindungen mit der IT-Welt gegen „allgemeine“ Cyberattacken sehr robust, aber der Nutzen in digitalen Geschäftsmodellen eben auch sehr eingeschränkt.
Erst wenn ein nennenswerter Teil des Shopfloors mit digitalen Komponenten und Systemen ausgerüstet ist, die die entsprechenden Internet-Technologien nutzen, wird es vielversprechend aber auch gefährlich. Die Vorgehensweise zur Risikominimierung unterscheidet sich dabei wenig von den Vorgehensweisen der Risikominimierung gegen funktionale Fehler: Die möglichen Angriffsszenarien müssen analysiert, der mögliche Schaden einer Cyberattacke ermittelt und geeignete Digitalisierungs- und Cybersicherheitskonzepte implementiert werden. Szenarien- und Konzepte müssen dann stetig an die wachsende Bedrohung und die technischen Möglichkeiten der Risikoabwehr angepasst werden – aufwendig und teuer. Viele digitale Geschäftsmodelle werden sich auf Grund dieser Cyber-Security-Kosten nicht mehr rechnen und ggf. ganz in der analogen oder zumindest gekapselten Welt verbleiben.
Welche Entwicklung erwarten Sie bei der Vernetzung von OT und IT in den kommenden Jahren?
Dr. Gunther Kegel: Der Shopfloor wird sich in den kommenden Jahren digitalisieren und mit dem Datenmodell der Verwaltungsschale werden wir einen industriellen Datenraum aufspannen, der die Entwicklung auch disruptiver Anwendung massiv fördert. Dazu wird es meines Erachtens notwendig auf diesen industriellen Datenraum über eine industrielle Plattform zuzugreifen. Die Plattform bekommt die Aufgabe, Geschäftsmodell für Geschäftsmodell, Teilmodell für Teilmodell alle notwendigen Transaktionen und Security Anforderungen bereitzustellen.
Dabei sollte die Plattform nicht als gigantisches, niemals endendes Software-Projekt gesehen werden – schon heute haben wir zu viele Plattformen ohne den notwendigen „Traffic“. Die Plattform muss sich aus konkreten Implementierungen einzelner Teilmodelle zusammensetzen, die Zug um Zug realisiert werden. Für jedes Teilmodell wäre so von Anfang an der notwendige „Traffic“ gewährleistet. Anwender und Hersteller, brauchen dann ihr Datenmodell bzw. Datenteilmodell jeweils nur einmal an die Plattform koppeln und nur einmal entsprechende Transaktionen einrichten. Denkt man z. B. an „Micro-Payments“ beim Zugriff auf komplexe Teilmodelle der Verwaltungsschale, so würde diese Transaktion einmal verbindlich für die Plattform aufgesetzt.
VDMA und ZVEI versuchen zurzeit gemeinsam diese Idee einer „wachsenden“ Plattform in einer gemeinsamen Institution unter dem Begriff „Manufacturing-X“ aufzusetzen. Damit ließe sich die Erfassung des „Carbon-Footprints“ aller verbauten Komponenten genauso erfassen wie die Lieferkette oder eine „Full-Material-Declaration“. Alles auf Knopfdruck verfügbar! Glaubt man dann noch an die Entstehung vieler neuer, disruptiver Geschäftsideen, wird das Ganze eine kraftvolle Vision.