Pepperl+Fuchs auf der Hannover Messe 2017
Industrie 4.0 ist Ausdruck für eine vernetzte Welt von Produktionsanlagen, in der Datenströme das wertschöpfende Lebenselixier bedeuten. Doch wo kommen die Daten her und welchen N...
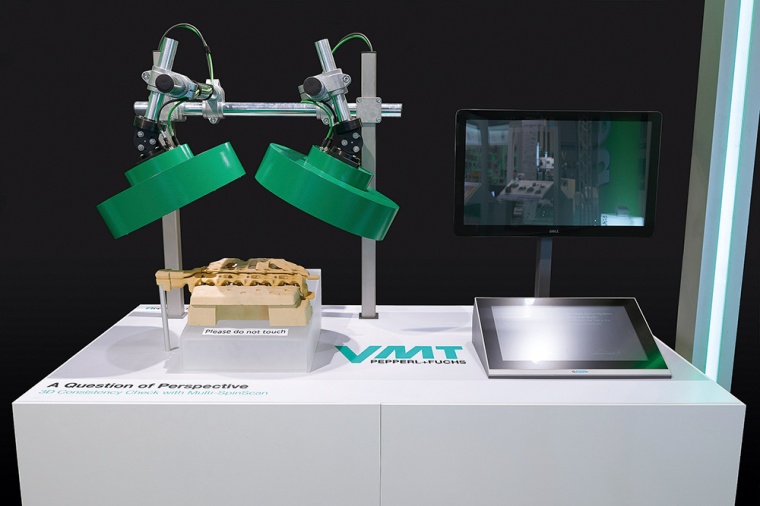
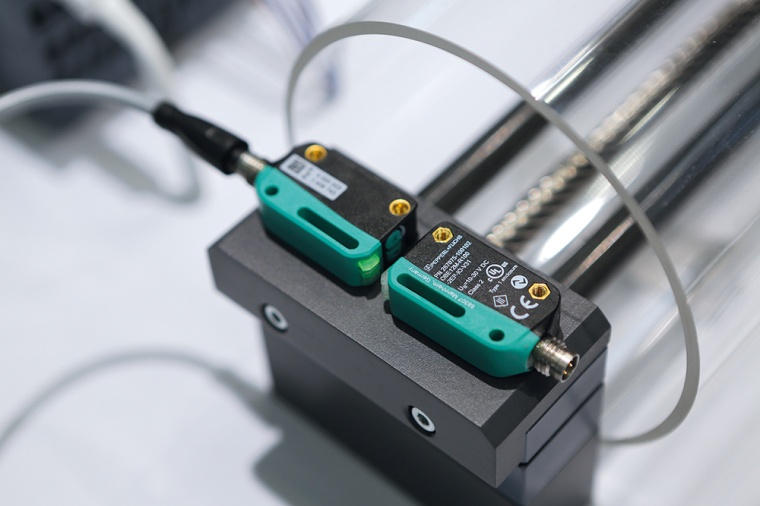
Industrie 4.0 ist Ausdruck für eine vernetzte Welt von Produktionsanlagen, in der Datenströme das wertschöpfende Lebenselixier bedeuten. Doch wo kommen die Daten her – und welchen Nutzen haben sie für die Fertigung? Auf der Hannover-Messe 2017 machte Pepperl+Fuchs die Datenströme sichtbar. Auf einer drei mal vier Meter großen Videowand und einem ebenso großen Videoboden konnten die Besucher die Produkt-und Datenströme im zwischen realer und virtueller Welt verfolgen.
Ein überdimensionaler aufgeklappter Laptop zeigte am Hannover-Messe-Stand von Pepperl + Fuchs eindrucksvoll, welchen Weg die Sensordaten vom physischen Objekt durch den Datenlayer als Zwischenschicht hindurch bis in die virtuelle Datenwelt der Cloud nehmen. Der Videoboden repräsentierte die reale Objektwelt, in der Fahrzeugkarossen transportiert oder Rohrleitungen und Ventile einer Chemieanlage dargestellt werden. Die Interaktion mit diesen realen Objekten löst einen entsprechenden Datenstrom in der virtuellen Welt der Videowand aus. Diese liefern dem Anwender wertvolle Zusatzinformationen zu den realen Objekten oder wichtigen Ver- und Entsorgungsprozessen, die im Hintergrund ablaufen.
Das Exponat demonstrierte je einen Anwendungsfall aus der Fertigungsindustrie und der Prozessindustrie. Der erste Fall aus dem Fabrikumfeld zeigte die Konfiguration von kundenindividuellen Fahrzeugen im Sinne einer „Stückzahl 1“-Produktion – der zweite Fall aus der Prozessindustrie ein automatisiertes Asset-Management für den Anlagenbau. Hierbei werden die Daten von Prozesskomponenten aus dem Feld automatisiert erfasst und in ein cloudbasiertes Managementsystem übertragen. Da die Prozesskomponenten nicht nur statische Identifikationsdaten, sondern parallel auch dynamische Zeitreihendaten aus ihrem Lebenszyklus übermittelten, konnte neben der reinen Bestandsverwaltung auch ein vorausschauendes Wartungsmanagement visualisiert werden.
Neben diesem weithin sichtbaren Highlight-Exponat wurden in dem benachbarten Solutionspark Industrie 4.0 themenverwandte Anwendungsfälle anschaulich umgesetzt. Die Exponate repräsentieren funktionierende Systemaufbauten für Asset-Management und Predictive Maintenance. So zeigte das Exponat „Automated Asset Administration“ eine Anwendung aus der Fertigungsindustrie und das Exponat „IoT für Process Automation“ eine verfahrenstechnische Anwendung aus der Prozessindustrie.
Automatische Bestandsverwaltung
Moderne Sensoren liefern neben den reinen Mess- oder Prozessdaten eine Vielzahl an Zusatzinformationen, die von der klassischen Maschinensteuerung in aller Regel nicht vollumfänglich ausgewertet werden können. So besteht die Kernaufgabe der Steuerung in der echtzeitfähigen Verarbeitung aller prozessnotwendigen Regelgrößen, um eine reibungsfreie und effiziente Funktion der Maschine zu gewährleisten. Die Zusatzinformationen aus den smarten Komponenten hingegen würden die Komplexität bei der funktionalen Auslegung der Maschine deutlich erhöhen. Um jedoch die wertvollen Zusatzinformationen aus smarten Komponenten dennoch wirtschaftlich nutzen zu können, steht eine andere Informationsverarbeitungsstrategie zur Verfügung. Bei dieser Strategie eröffnet ein nachrüstbares Gateway den Zugang zur untersten Funktionsebene von Sensoren und Aktoren und leitet sowohl Typ- als auch Instanzdaten der Komponenten an eine Datenplattform im Internet. Dieser Datenzugriff geschieht völlig rückwirkungsfrei und ohne die regelungstechnische Funktion der Maschine zu beeinflussen.
Der Demonstrator „Automated Asset Administration“ entstand in Zusammenarbeit zwischen Pepperl+Fuchs, der Hilscher Gesellschaft für Systemautomation und der SAP SE. Er zeigt, wie leicht die funktional unabhängige Mustermaschine mit einem Anschluss an die Datenplattform versehen werden kann. Diese Cloud-Plattform erfasst sowohl typbezogene Identifikationsdaten wie Hersteller, Artikelnummer und Geräte-ID, als auch instanzbezogene Daten wie den aktuellen Firmwarestand oder Funktionsdaten der Komponente selbst, die als Zeitreihe über ihren Lebenszyklus hinweg gespeichert werden.
Die Identifikationsdaten liefern ein elektronisches Abbild der Maschinen- oder Anlagestruktur und garantieren so auch beim Tausch von Komponenten den Datenabgleich zwischen der eingebauten Hardware und dem zugehörigen, digital gespeicherten Parametersatz. Ein solcher Abgleich hat den Vorteil, dass neben der automatischen Aktualisierung des Maschinen- oder Anlagenplans, die Austauschkomponente im Hintergrund auch gleich die betriebsnotwendige Dokumentation laden kann. Eine solche elektronische Überprüfung ermöglicht es darüber hinaus, unzulässige Austauschkomponenten zu identifizieren. Dieses Vorgehen wahrt die Funktionsgarantie und gewährleistet auch über viele Jahre hinweg einen sicheren Betrieb der Anlage.
Neben der Erfassung der Identifikationsdaten liefert das Protokoll – basierend auf Prozess- und Zustandsdaten – auch den tatsächlichen Betriebszustand der Maschine zurück. Die Betriebszustände werden in der Cloud-Plattform überwacht und können so nicht nur den Wartungsbedarf der Komponente ermitteln, sondern auch Prognosen für künftige Wartungseinsätze ableiten.
IoT for Process Automation
Im Gegensatz zur Fertigungsindustrie haben sich in der Prozessindustrie aus verschiedenen Gründen Datenbussysteme noch nicht flächendeckend durchgesetzt. So werden in solchen verfahrenstechnischen Anlagen bis zum heutigen Tage viele Feldgeräte wie Stellventile oder Messgeräte für Durchfluss, Druck, Temperatur oder ähnlichen Messgrößen noch über eine 4-20mA Stromschleife angeschlossen.
Diese klassisch-analoge Signalübertragung zwischen Leitrechner und Feldgerät unterstützt nur eine reine Sollwertübertragung bei Aktoren oder einfache Messwertübertragung bei Sensoren. Ein bidirektionaler Datenaustausch im Sinne einer echten Kommunikation bleibt aus.
Dennoch haben moderne Feldgeräte auch heute schon meist umfangreiche Intelligenz an Bord, die über ihre Identität oder ihren Betriebszustand informieren könnte. Auf Basis dieser Zusatzinformationen können beispielsweise Ventile den eigenen mechanischen Verschleiß bewerten oder Durchfluss-Messgeräte Korrosion und Abrasion erkennen. Obwohl die eingesetzten Feldgeräte üblicherweise auch das digitale Hart-Protokoll unterstützen, bieten die meisten Anlagen, vor allem die älteren, keine geeignete Infrastruktur, um die Hart-Signale auszuwerten. Die wertvollen Zusatzinformationen bleiben weitgehend ungenutzt.
Der Demonstrator „IoT für Prozess Automation“ zeigt, wie diese Lücke einer fehlenden Datenkommunikation geschlossen werden kann. Die Lösung liegt in einem parallelen, funkbasierten Kommunikationskanal, der in der Lage ist, die Zusatzdaten im Sinne des Internet of Things (IoT) bereitzustellen. Der Vorteil dieses neuen Datenkanals ist, dass er völlig rückwirkungsfrei und ohne Eingriff in die vorhandene Prozesssteuerung entsteht.
Rein technisch basiert der Datenkanal auf der Wireless-Hart-Technologie. So werden die Feldgeräte einfach mit Wireless-Hart-Adaptern, sogenannten Bullets, nachgerüstet. Diese bauen zusammen mit dem Wireless-Hart-Gateway ein drahtloses Netzwerk zwischen den einzelnen Stationen auf. Eine spezielle Software, der IoT-Agent, wird auf das Gateway geladen und sorgt für die korrekte Übertragung der Gerätedaten an die Cloud-Plattform im Internet. Die Konfiguration des Gateways erfolgt mit Hilfe eines intuitiv bedienbaren Applikationsprogramms, das auf unterschiedlichsten Betriebssystemen laufen kann.
Die in der Cloud bereitgestellten Daten können von nachgelagerten IT-Anwendungen genutzt werden. So ermöglichen weiterführende „IoT-Services“ Dienste wie Condition Monitoring oder Predictive Maintenance. Aber auch eine für den Anlagenbetrieb überaus wichtige Bestandsverwaltung wird durch die Funktion des Asset Managements unterstützt.
Datenverfügbarkeit und Datentransparenz stellen ein wesentliches Kernelement vernetzter Produktionssysteme dar. Die Basistechnologien dafür sind heute schon vorhanden. Solange einheitliche Standards fehlen, gilt es, die vorhandenen Technologien mit Kreativität und Engagement zu orchestrieren. Wie das gelingen kann, zeigte Pepperl+Fuchs sehr eindrucksvoll in seinem Solutionspark Industrie 4.0.
Meist gelesen
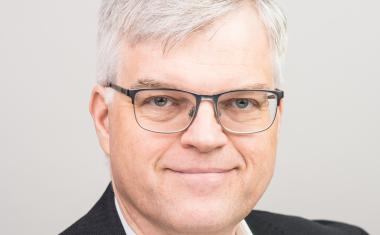
Maschinensicherheit im Kontext von KI und Security – Cyber Resilience Act: Neue Anforderungen für Maschinenbauer
Cyber Resilience Act & Maschinenverordnung: Neue Sicherheitsanforderungen für Maschinenbauer in vernetzten Industrieanlagen
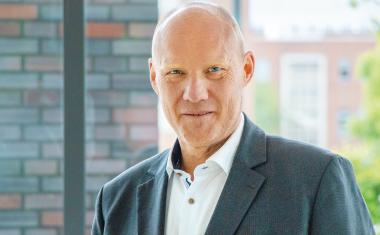
VIP-Interview: Andreas Maack, Chief Security Officer bei Volkswagen
GIT SICHERHEIT im Interview mit Andreas Maack, Leiter Konzern Sicherheit & Resilienz und Chief Security Officer der Volkswagen AG.
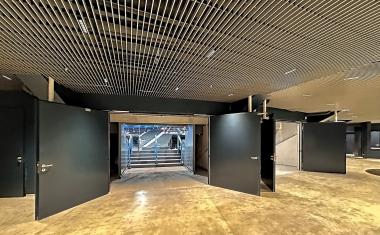
Brandschutztore für den SAP Garden in München
Diese multifunktionale Arena, die Platz für bis zu 11.500 Zuschauer bietet, eignet sich zudem für eine Vielzahl von Veranstaltungen und erfordert dementsprechend höchste Sicherheitsstandards.
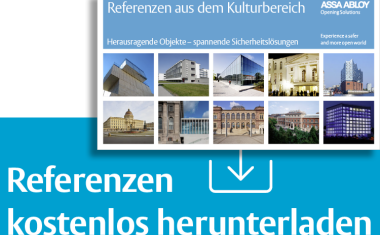
Zutritt steuern, Werte schützen – Schließtechnik für Kulturstätten
Öffentlich zugängliche Kulturinstitutionen sind mit unschätzbaren materiellen und immateriellen Werten ausgestattet.
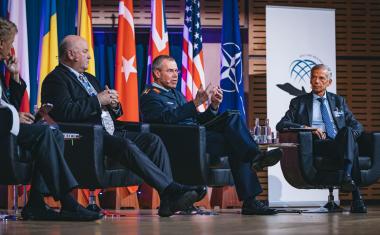
Euro Defence Expo und NATO JAPCC parallel zur Security Essen 2026
Vom 22. bis 25. September 2026 wird die Euro Defence Expo (Eudex) ihre Premiere in der Messe Essen begehen – gleichzeitig mit der jährlichen Konferenz des NATO Joint Air Power Competence Centre sowie der Security Essen.