Persönliche Schutzausrüstung wird intelligenter und stärker vernetzt
Vielleicht ist Sicherheit nicht gerade der erste Anwendungsbereich, der einem in den Sinn kommt, wenn die Konzepte Industrie 4.0 und Smart Factory erwähnt werden. Dennoch wird selb...
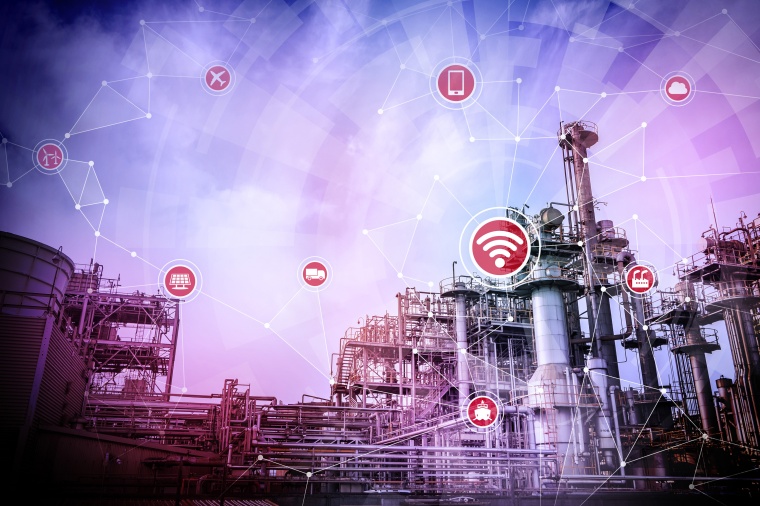
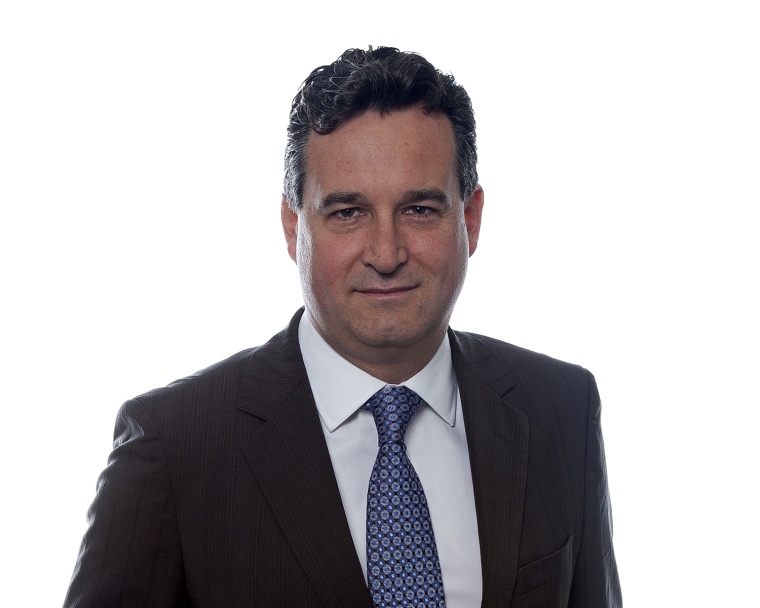
Vielleicht ist Sicherheit nicht gerade der erste Anwendungsbereich, der einem in den Sinn kommt, wenn die Konzepte Industrie 4.0 und Smart Factory erwähnt werden. Dennoch wird selbst persönliche Schutzausrüstung (PSA) vom Typ „Low-Tech“ immer intelligenter und stärker vernetzt. Im Folgenden erklärt Thomas Negre, Global Director für den Bereich Gasdetektion und vernetzte Mitarbeiter bei Honeywell Industrial Safety, warum vernetzte Sicherheit in den Smart Factories von heute eine zentrale Rolle spielt und den Schutz der Mitarbeiter sowie die Produktivität verbessert.
Industrie 4.0 verwandelt die verarbeitende Industrie. Die sogenannte vierte industrielle Revolution wird von einem beispiellosen Anstieg der Datenverfügbarkeit, Rechenleistung und Konnektivität sowie von neuen Formen von Mensch-Maschine-Interaktionen getragen, der den Verantwortlichen der Industriekonzernen helfen soll, bessere Entscheidungen schneller zu treffen, Betriebskosten zu sparen und die Effizienz und Produktivität zu steigern. Mit anderen Worten: Es geht darum, Fabriken intelligenter zu machen. Aber Industrie 4.0 setzt sich dank der neuesten Fortschritte in der vernetzten Sicherheitstechnik auch im Bereich der industriellen Sicherheit durch. Wenn die Unternehmen ihre Mitarbeiter wirksamer schützen können, verhilft ihnen dies zu einem Wettbewerbsvorteil, da viele Kosten im Zusammenhang mit dem Sicherheitsmanagement reduziert werden.
Traditionell papierbasiert
Die Europäische Rahmenrichtlinie über Sicherheit und Gesundheitsschutz bei der Arbeit (Richtlinie 89/391 EWG) verpflichtet Arbeitgeber, geeignete Präventivmaßnahmen zu ergreifen, um die Arbeit sicherer und gesünder zu gestalten, wobei die Bedeutung neuer Formen des Sicherheits- und Gesundheitsmanagements im Rahmen der allgemeinen Managementprozesse betont wird.[1] Vor diesem Hintergrund – und angesichts des wachsenden Bewusstseins für die hohen Geldbußen und Reputationsschäden, die sich aus Verstößen gegen die Sicherheitsvorschriften oder einfach aus der Nichtbeachtung der aufsichtsrechtlichen Bestimmungen ergeben können – haben viele Unternehmen im Laufe der Jahre Datenbanken angelegt, über welche die Expositionswerte ihrer Mitarbeiter erfasst werden und die zur besseren Verwaltung und Wartung der von ihnen verwendeten Sicherheitsausrüstung beitragen. Dennoch war und ist dies traditionell ein papierbasierter Prozess, der die manuelle Eingabe von Daten zu Arbeitsschutz und zur Gesundheit erfordert – trotz der Verfügbarkeit von Softwareanwendungen zur Vereinfachung der Aufgabe.
Dieser unsystematische Ansatz kann die Mitarbeiter letztendlich in Gefahr bringen, insbesondere in großen Fabriken, in denen die manuelle Eingabe von Daten äußerst schwierig zu bewältigen ist. Die Sicherstellung, ob PSA und andere Schutzvorrichtung ordnungsgemäß gewartet werden, ist dadurch erschwert. Auch lässt sich schwer feststellen, ob die Schutzausrichtung für den vorgesehen Zweck geeignet und auf dem neusten Stand ist sowie den Vorschriften entspricht. Darüber hinaus muss sichergestellt werden, dass die Mitarbeiter sie korrekt verwenden. Angesichts dessen, dass häufig mit weniger Mitteln mehr getan werden muss und dass die Sicherheitsfachkräfte heute für immer größere Aufgabenbereiche zuständig sind, kann es sein, dass sich PSA-Inspektionen auf regelmäßige Werksprüfungen oder Stichprobenkontrollen beschränken. Außerdem sind sie zeitaufwendig und kostspielig und können die Produktivität beeinträchtigen. Zudem können sie Unternehmen potenziell in die Lage bringen, Bußgelder zahlen zu müssen. Zum Beispiel können kleine und mittlere Unternehmen (KMU) damit rechnen, bis zu 45.000 EUR pro Jahr für die Einhaltung der Gesundheits- und Sicherheitsvorschriften auszugeben, am Ende aber eine Geldstrafe von durchschnittlich rund 130.000 EUR zahlen zu müssen, wenn sie eines Verstoßes für schuldig befunden werden.[2]
Sicherheitsausrüstung intelligenter machen
Hier bietet sich die Gelegenheit, die Einhaltung der Vorschriften mit einer verstärkten Automatisierung zu verbinden. Der Schlüssel liegt darin, die Sicherheitsausrüstung intelligenter zu machen. Werden in die persönliche Schutzausrüstung Sensoren oder RFID-Technologie (RFID: Radiofrequenz-Identifizierung) integriert, werden sie zu Spitzengeräten im Internet der Dinge, die Daten sammeln und übertragen können – was die Datenerfassung beschleunigt und die Genauigkeit sowie die Effizienz steigert. In diesem Datensammlungssystem dient der mobile, vernetzte Mitarbeiter als der Mittelpunkt des Konzepts.
Mit Hilfe einer Bluetooth-Verbindung können Mitarbeiter nun zum Beispiel automatisch einen tragbaren Gasdetektor oder ein anderes Gerät mit ihrem Smartphone verbinden. Dank der Kombination aus drahtloser Konnektivität, der neuesten Software und Cloud-Technologie können Sicherheitsfachkräfte mittels Laptop oder Smartphone sofort sehen, welcher Mitarbeiter das Gerät benutzt und ob dieses alle wichtigen Eigenschaften erfüllt: ob das Gerät in Bezug auf die Einhaltung der Vorschriften auf dem neuesten Stand ist und wann es zuletzt gewartet wurde und auch ob der Mitarbeiter für den Umgang mit seiner Sicherheitsausrüstung angemessen geschult wurde. Sicherheitsfachkräfte können innerhalb von Sekunden auf diese Informationen zugreifen und erhalten darüber hinaus eine Fülle anderer Daten, wie z. B. Gaskonzentrationswerte, die Anzahl der Sicherheitsvorfälle in einem bestimmten Zeitraum und aktuelle Daten zu Zustand und Funktionsfähigkeit von Gerätesensoren.
Vernetzt und datengestützt
Die Automatisierung von Abläufen zur Einhaltung der Sicherheitsvorschriften ist nicht die einzige Möglichkeit, Techniken der vernetzten Sicherheit einzusetzen, um die Herausforderungen in den Smart Factories zu bewältigen. Von der Automobilindustrie bis hin zur Luft- und Raumfahrtindustrie ist die Umstellung auf vernetzte Sicherheit in vielen Umgebungen mit hohem Risikopotential bereits Realität, wie etwa in zugangsbeschränkten Bereichen. Dies hat gezeigt, wie ein datengestützter Ansatz Leben retten kann.
Von Gasflaschenschränken in Halbleiterwerken bis zu den Flügeln einer Boeing 747 sind zugangsbeschränkte Bereiche in der Fertigung weit verbreitet und gehören zu den gefährlichsten Umgebungen für die Mitarbeiter. Diejenigen, die sich in solchen Bereichen aufhalten, können Risiken wie Sauerstoffmangel (oder manchmal auch Sauerstoffanreicherung), Exposition gegenüber toxischen oder entflammbaren Gasen, hohen Lärmpegeln und Stürzen ausgesetzt sein. Die Einsicht in die biomedizinischen Werte dieser Mitarbeiter (Herzfrequenz, Körpertemperatur, Atemfrequenz) sowie ihrer Expositionswerte in Echtzeit ist von größter Bedeutung, um die Mitarbeiter in einer potenziell gefährlichen Situation warnen und, wenn nötig, Notfallrettungseinsätze leiten zu können. Es ist entscheidend, die Gaskonzentration und die Position eines Mitarbeiters zu kennen, der das Bewusstsein verloren hat, bevor die Retter in Aktion treten. Nur so können sie mit der richtigen Ausrüstung zum Schutz gegen die Gefahren ausgestattet werden, mit denen sie es zu tun haben.
Vernetzung wird Teil des Smart Factory-Ökosystems
Da die Konnektivität nun zugänglicher und erschwinglicher wird, weitet sich die vernetzte Sicherheitsinfrastruktur auf Bereiche außerhalb der Umgebungen mit hohem Risikopotential aus und wird nach und nach Teil des Smart Factory-Ökosystems. Insbesondere das Smartphone hat sich zu einem vielseitigen Knotenpunkt für die Datenerfassung und -übertragung entwickelt. Dadurch erschließen sich ganz neue Möglichkeiten in Bezug auf die Sicherheit sowohl in Umgebungen mit hohem als auch in solchen mit geringem Risikopotential.
Es gibt mittlerweile mehrere Anbieter von Industrie-Smartphones, die ebenso benutzerfreundlich sind wie ihre Pendants für den privaten Gebrauch und gleichzeitig die robusten Anforderungen für industrielle Umgebungen erfüllen. Beispielsweise können Personen, die in explosionsgefährdeten Bereichen arbeiten, über ein mobiles Netzwerk für Gefahrenbereiche zertifizierte oder eigensichere Smartphones verwenden.
Wie bereits erwähnt, können Smartphones nun Verbindungen zu anderen Geräten wie etwa Gasdetektoren herstellen. Dadurch können auch Mitarbeiter, die keinen tragbaren Gasdetektor tragen, gewarnt werden, wenn durch ein stationäres Gaswarngerät in einem anderen Teil des Werks ein Gasleck erkannt wird. Sicherheitsfachkräfte können von jedem beliebigen Ort aus über ein Smartphone die Arbeitsschutz- und Gesundheitsdaten eines bestimmten Mitarbeiters einsehen und wenn nötig eingreifen. Dies kann z. B. dann der Fall sein, wenn der Mitarbeiter keinen Gehörschutz trägt, wo dieser erforderlich ist, oder wenn er diesen nicht richtig trägt. Die neuesten industriellen Smartphone-Apps bieten außerdem Funktionen wie On-Demand-Schulungen mit klaren visuellen Anweisungen und informieren sowohl den Mitarbeiter als auch die Sicherheitsfachkräfte darüber, welche Gasdetektoren und welche persönliche Schutzausrüstung (PSA) für die konkrete Aufgabe benötigt werden.
Die Daten werden außerdem gespeichert, so dass Sicherheitsfachkräfte Berichte über Mitarbeiter ausführen und ihre Exposition gegenüber gefährlichen Stoffen über einen längeren Zeitraum einsehen können. Dies ist entscheidend, um gegen gesundheitliche Probleme vorgehen zu können, bevor es zu spät ist. Diese Daten können dann auch als Grundlage für Entscheidungen zur Arbeitseinteilung herangezogen werden, so dass zum Beispiel die Exposition eines Mitarbeiters für den Verlauf einer bestimmten Schicht reduziert wird.
Produktivität steigern, Kosten senken
Diese Möglichkeiten der vernetzten Arbeitssicherheit, wie die Übermittlung der Daten eines Gasdetektors direkt an den Kontrollraum, können die Einhaltung der Sicherheitsvorschriften und das Monitoring der Arbeitssicherheit automatisieren und zudem die Produktivität steigern. Dies liegt vor allem daran, dass Mitarbeiter ihre Arbeit nicht alle paar Minuten unterbrechen müssen, um Informationen wie z. B. Gasmesswerte manuell zurückzusenden. Zudem können sich Mitarbeiter darauf verlassen, dass die von ihnen verwendete Ausrüstung für den jeweiligen Zweck geeignet ist und dass ihre Expositionswerte genau eingesehen werden können. So ist eine bessere Konzentration auf die Arbeit möglich, was die Gesamtproduktivität und -effizienz verbessert. Entsprechende Untersuchungen der Bundesanstalt für Arbeitsschutz und Arbeitsmedizin (BAuA) haben ergeben, dass die Sicherheit des Arbeitsplatzes, neben einem festen Einkommen, zu den wichtigsten Aspekten „guter Arbeit“ gehört. [3]
Wichtiger noch: Da die Techniken der vernetzten Sicherheit ein sofortiges Eingreifen und die Vermeidung gefährlicher Situationen sowie dauerhafter Erkrankungen ermöglicht, kann sie dabei helfen, die enormen Kosten möglicher Produktionsausfälle zu senken. Im vergangenen Jahr kam es in Deutschland zu 877.071 arbeitsbedingten Verletzungen, die für mehr als drei Fehltage sorgten.[4] Pro Jahr kann dies zu einem Produktionsverlust von bis zu 46 Mrd EUR führen.[5] Der vernetzte Mitarbeiter ist ein gesünderer, besser geschützter und produktiverer Mitarbeiter.
Anpassung an das digitale Zeitalter
Mit Blick auf die Zukunft ist zu sagen, dass die Vorteile der Automatisierung von Sicherheitsmanagementprozessen offensichtlich sind, aber eine Herausforderung für die Sicherheitsexperten für Smart Factories darin besteht, festzustellen, wie sich das wachsende Datenvolumen effektiv verwalten lässt. Früher waren die Sicherheitsfachkräfte für den gesamten Verwaltungsprozess im Zusammenhang mit der Sicherheitsausrüstung verantwortlich – von der Beschaffung bis zur Schulung und Inspektion. Ganz allgemein wird die Zusammenarbeit zwischen den verschiedenen Beteiligten – von PSA-Herstellern bis hin zu Software- und Telekommunikationsanbietern – für die Entwicklung einer vollständig vernetzten Lösung entscheidend sein, mit der die Smart Factories der Zukunft sicherer gestaltet werden können.
Der Arbeitsschutz entfernt sich eindeutig immer weiter von seiner „analogen“ Vergangenheit und passt sich dem digitalen Zeitalter an. Er spielt eine bedeutende Rolle beim Wandel in den Fabriken zu Zeiten von Industrie 4.0. Die Möglichkeit, Daten zu Arbeitsschutz und -gesundheit effizienter zu sammeln und zu analysieren, wird nicht nur dafür sorgen, dass die Mitarbeiter in Smart Factories besser geschützt sind, sondern erhöht auch die Effizienz und die Produktivität. Letztlich erwarten die Mitarbeiter ihrerseits, dass die Technik, die ihnen bei der Arbeit an die Hand gegeben wird, ebenso benutzerfreundlich ist wie jene, die sie zu Hause verwenden. Die vernetzte Sicherheit kann ihnen dabei helfen, genau das zu erreichen.
Business Partner
Honeywell Industrial Safety - Honeywell Safety Products Deutschland GmbH & Co. KGKronsforder Allee 16
23560 Lübeck
Deutschland
Meist gelesen
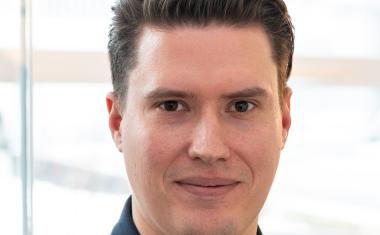
VDMA-Einheitsblatt 24994: Einheitliches Prüfverfahren für die Zertifizierung von Lager-/Ladeschränken für Lithium-Ionen-Akkus
In einer Zeit, in der die sichere Lagerung und das Laden von Lithium-Ionen-Batterien immer wichtiger werden, setzt das VDMA-Einheitsblatt 24994 neue Maßstäbe und definiert klare Anforderungen an Sicherheitsschränke.
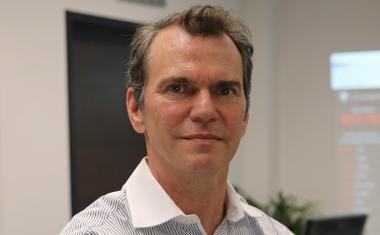
Globale Sicherheitsstrategien der DHL Group
Frank Ewald von der DHL Group über globale Sicherheitsstrategien und die Herausforderungen der Logistikbranche im Interview
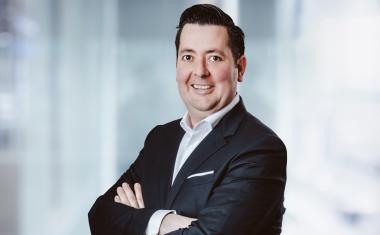
Disruptiv aus Überzeugung - Interview mit Carsten Simons über technologische Unabhängigkeit, mutige Weiterentwicklung und die Zukunft der mobilen Videoüberwachung
LivEye-Chef Carsten Simons über Disruption, technologische Unabhängigkeit und das neue Überwachungssystem NSTR
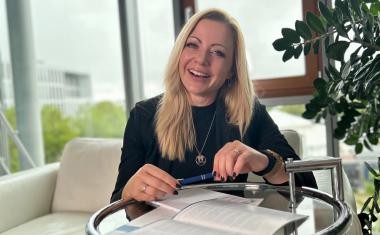
Schutz für exponierte Personen und wohlhabende Familien
Personenschutz für Vermögende: Christina Schwung über Risiken, Schutzkonzepte und digitale Bedrohungen
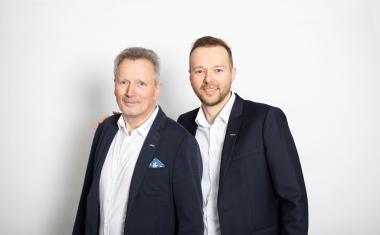
Partner des Fachhandels – Ein Gespräch mit Jürgen Hövelmann von EPS-Vertrieb
Sicherheitslösungen mit Tradition & Innovation: EPS-Vertrieb stellt das Ajax Fire-System vor