Maschinensicherheitsnormen in der Praxis: Teil 2
Für die Sicherheit von Maschinen gibt es drei Gruppen von Normen, nämlich die Gruppen A, B und C. In einer mehrteiligen Artikelserie für GIT SICHERHEIT befasst sich Jens Rothenburg...
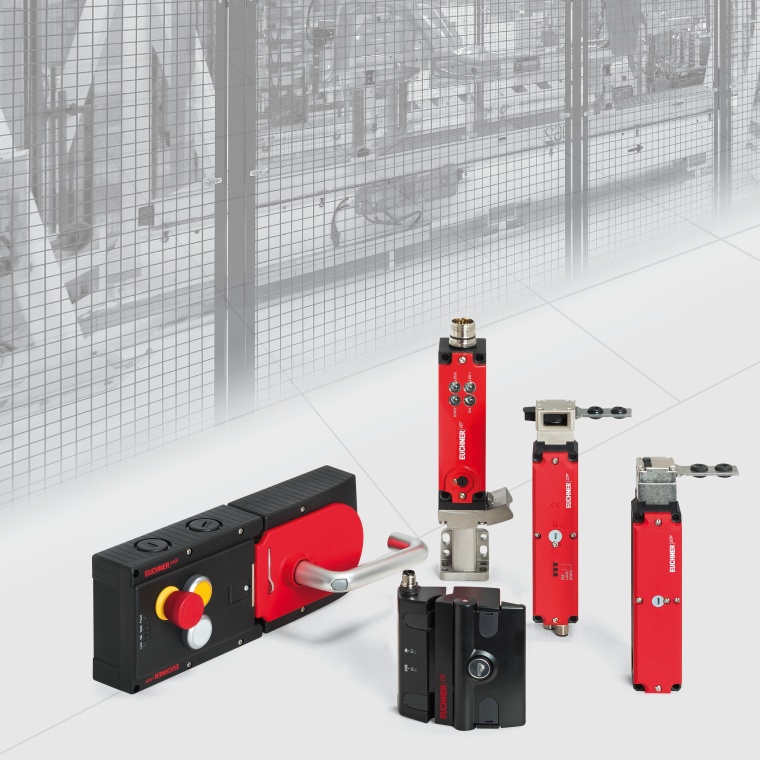

Für die Sicherheit von Maschinen gibt es drei Gruppen von Normen, nämlich die Gruppen A, B und C. In einer mehrteiligen Artikelserie für GIT SICHERHEIT befasst sich Jens Rothenburg von Euchner vor allem mit den übergeordneten A- und B-Normen – und der Frage, wie sie im praktischen Umgang gut zu nutzen sind. Jens Rothenburg ist im Produktmanagement von Euchner tätig. Er betreut außerdem Normengremien, Berufsgenossenschaften und Verbände. Mit dem Thema „Risikobeurteilung“ setzt der folgende Teil 2 die in GIT SICHERHEIT 9/2017 mit der Einführung in das Thema begonnene Serie fort.
Im Anhang I der Maschinenrichtlinie wird in Europa gefordert, dass jeder Hersteller oder sein Bevollmächtigter eine Risikobeurteilung für jede Maschine erstellt, bevor diese in den Verkehr gebracht wird. Es gibt unterschiedliche Methoden, um eine solche Analyse durchzuführen. Leitsätze zur Risikobeurteilung finden sich in der EN ISO 12100. Diese Norm beschreibt grundsätzliche Risiken die entstehen können und nennt einige Methoden – ohne diese näher zu erläutern –, mit denen eine Risikobeurteilung durchgeführt werden kann.
Risikobeurteilung mit der EN ISO 12100
Eine generelle Strategie, wie das Risiko einer Maschine gemindert werden muss, ist einer der Hauptpunkte in der Norm. Es muss ein dreistufiges Verfahren angewendet werden.
Im ersten Schritt muss durch eine geeignete Konstruktion das Risiko sich zu verletzen so weit möglich minimiert werden. Beispielsweise sollten alle Kanten so ausgeführt werden, dass sich niemand daran verletzten kann. Quetsch- und Scherstellen die z. B. durch Abdeckungen vermeidbar sind, müssen dementsprechend ausgeführt werden.
Wenn die mit dem ersten Schritt getroffenen Maßnahmen nicht ausreichen, um alle Gefahren zu eliminieren oder zu minimieren, dann müssen im zweiten Schritt technische Maßnahmen zur Risikominderung eingesetzt werden. Das sind in erster Linie einmal sogenannte trennende Schutzeinrichtungen, die verhindern, dass die Gefährdungsstelle überhaupt zugänglich ist.
Das würde natürlich bedeuten, dass die Maschine komplett umschlossen werden muss, was in der Praxis nicht möglich ist. Deshalb werden für den notwendigen Zugang Türen oder Klappen eingebaut. Diese Zugänge, sogenannte bewegliche trennende Schutzeinrichtungen, müssen mittels Sicherheitsschaltern dem Risiko der dahinter liegenden Gefahrenstelle entsprechend, abgesichert werden. Wenn also ein hohes Verletzungsrisiko besteht, muss eine qualitativ hochwertige Absicherung vorgesehen werden.
Im dritten Schritt muss sich der Benutzer der Maschine mit einer persönlichen Schutzausrüstung selbst schützen. Das ist an vielen Stellen unumgänglich, muss aber auch auf diese Stellen beschränkt bleiben. Die Maßnahmen müssen in der Dokumentation der Maschine aufgeführt werden. Unter Umständen müssen darüber hinaus Warnhinweise angebracht werden, wenn es keine technischen Möglichkeiten mehr gibt.
Lebensphasen der Maschine
Des Weiteren informiert die EN ISO 12100 darüber, welche Lebensphasen einer Maschine abgesichert werden müssen und welche verschiedenen Gefahren zu berücksichtigen sind.
Als Lebensphasen sind aufgeführt:
- Transport, Montage und Installation;
- in Betrieb nehmen;
- Verwendung;
- Demontage, außer Betrieb nehmen und Entsorgung.
Bei den Lebensphasen sind auch Aufbau und Abbau einer Maschine enthalten. Phasen, die von vielen Maschineherstellern nicht beachtet werden, bei denen aber eine sehr große Gefahr für das Personal besteht.
Zudem listet die Norm eine große Anzahl an Aufgaben während des Betriebs einer Maschine auf, die alle beurteilt werden müssen:
- Einrichten
- Prüfen
- Einlernen (Teachen)/Programmieren
- Umrüsten
- Anlauf
- alle Betriebsarten
- Maschinenbeschickung
- Entnahme des Produktes aus der Maschine
- Stillsetzen der Maschine
- Stillsetzen der Maschine im Notfall
- Wiederherstellung des Betriebs nach Stau oder Blockierung
- Wiederanlauf nach außerplanmäßigem Stillsetzen
- Fehlersuche und Fehlerbeseitigung (Eingreifen der Bedienperson)
- Reinigung und Sauberhaltung
- präventive Instandhaltung
- Fehler behebende Instandhaltung
Bei all diesen Aufgaben müssen Gefährdungen in der Risikobeurteilung berücksichtigt werden. Falls eine Gefahr vorhanden ist, muss diese entsprechend der Risikobeurteilung gemindert werden.
Ein zusätzlicher, häufig sehr schwierig zu beurteilender, Punkt der Risikoeinschätzung ist das unbeabsichtigte Verhalten eines Bedieners oder die vernünftigerweise vorhersehbare Fehlanwendung einer Maschine. Auch Störungen an einer Maschine, beispielsweise durch Ausfall eines Bauteils, sind zu berücksichtigen.
Beispiele für Gefährdungen
Vielfach werden auch nicht alle Gefährdungen bedacht, die von einer Maschine oder Anlage ausgehen können. Deshalb finden sich auch Beispiele für die verschiedenen Möglichkeiten der Gefährdung im Anhang der Norm:
- Quetschen durch bewegliche Teile
- Quetschen durch fehlende Standfestigkeit der Maschine oder eines Maschinenteils
- Stromschlag oder tödlicher Stromschlag aufgrund von Teilen der elektrischen Ausrüstung, die im Fehlerzustand spannungsführend geworden sind
- bleibender Gehörverlust durch anhaltende Exposition gegenüber Lärm, verursacht durch stanzende Teile
- Atembeschwerden durch Inhalation toxischer Substanzen
- Störungen des Bewegungsapparates durch ungesunde Körperhaltung oder eine sich wiederholende Tätigkeit
- Verbrennung durch Kontakt mit Material hoher Temperatur
- Hautentzündung (Dermatitis) durch Kontakt der Haut (dermale Exposition) mit toxischen Substanzen
Diese Liste ist keineswegs vollständig. Im Anhang B der Norm finden sich noch deutlich mehr Gefährdungen. Es soll sensibilisiert werden, nicht nur die offensichtlichen Gefahren durch mechanische Gefährdungen zu beachten, sondern eben auch andere Arten der Gefahr für den Menschen.
Die Risikobeurteilung selbst besteht aus den Abschnitten:
- Risikoanalyse, bestehend aus
- der Festlegung der Grenzen der Maschine
- der Identifizierung der Gefährdungen, und
- der Risikoeinschätzung, und
- Risikobewertung.
Das alles zusammen genommen stellt eine sehr komplexe Aufgabe für den Konstrukteur einer Maschine dar.
Meist gelesen
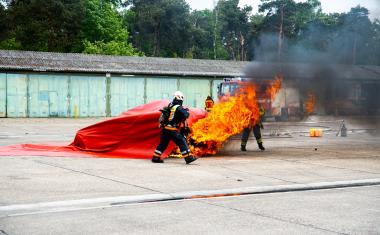
Lithium-Ionen Energiespeicher: Abwehrender und vorbeugender Brandschutz
Lithium-Ionen-Technologie: Hohe Energiedichte, vielseitig einsetzbar, aber auch Risiken im Brandschutz beachten
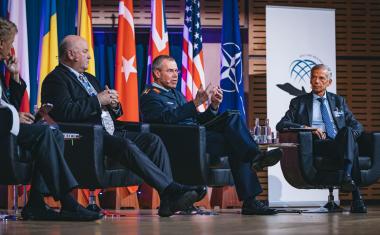
Euro Defence Expo und NATO JAPCC parallel zur Security Essen 2026
Vom 22. bis 25. September 2026 wird die Euro Defence Expo (Eudex) ihre Premiere in der Messe Essen begehen – gleichzeitig mit der jährlichen Konferenz des NATO Joint Air Power Competence Centre sowie der Security Essen.
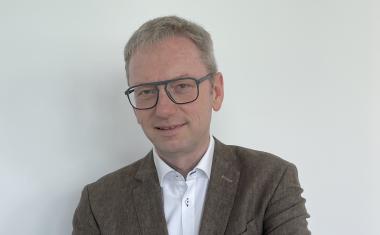
VDMA-Einheitsblatt 24994: Lithium-Ionen-Batterien im Fokus
VDMA 24994 Anforderungen und Prüfverfahren für Lithium-Ionen-Schränke im Interview mit Priorit erläutert
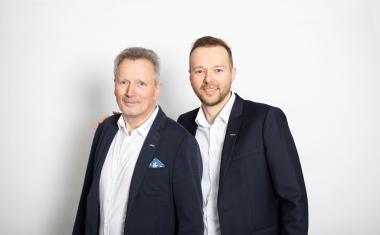
Partner des Fachhandels – Ein Gespräch mit Jürgen Hövelmann von EPS-Vertrieb
Sicherheitslösungen mit Tradition & Innovation: EPS-Vertrieb stellt das Ajax Fire-System vor
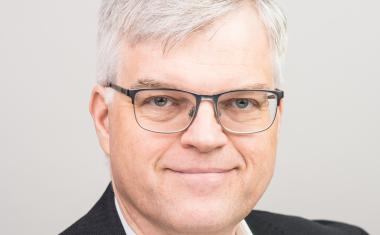
Maschinensicherheit im Kontext von KI und Security – Cyber Resilience Act: Neue Anforderungen für Maschinenbauer
Cyber Resilience Act & Maschinenverordnung: Neue Sicherheitsanforderungen für Maschinenbauer in vernetzten Industrieanlagen